Krones company history
Join us on our journey from a family business to a technology group.
1951 – 1965
1951
The company is founded
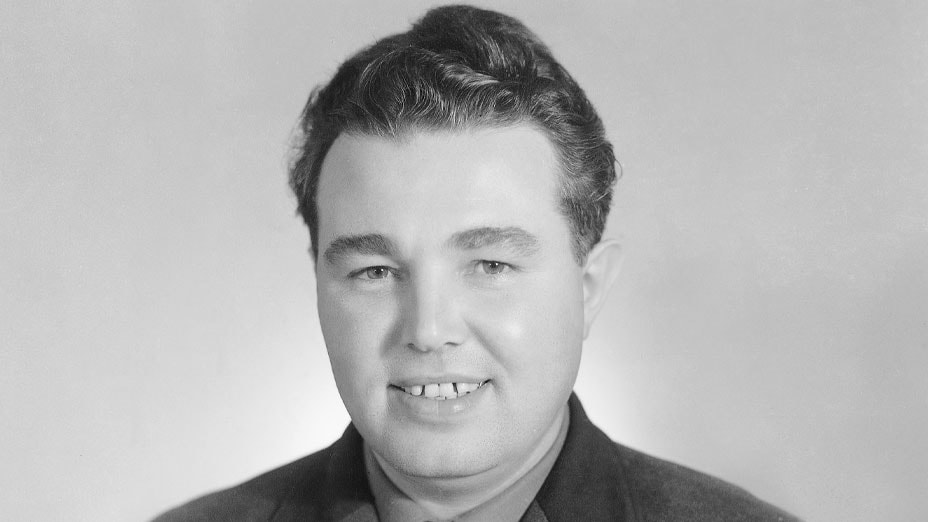
Hermann Kronseder starts to manufacture labellers.
Built by Hermann Kronseder himself, a qualified master mechanic and electrician, the workshop measures about 100 m2 and constitutes the production facility for the semi-automatic labellers. All the equipment the founding father needs is a lathe, a drilling machine, and a sanding block.
1952
A striking visual image at the start-up
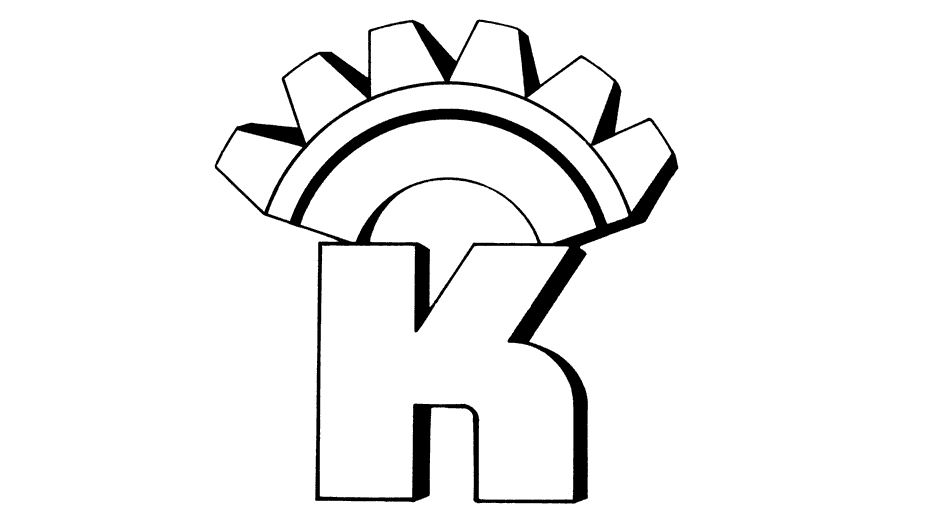
Right from the start-up of his business, Hermann Kronseder realises the value of recognition: soon after the company was set up in 1951, its first logo is designed. It shows a stylised "K" (for "Krones") and above it a crown from a gearwheel segment.
Marketing in the 1950s
A brochure is created for the very first machine. The logo, a "K" with a gearwheel section, and an easy-to-remember company name (an abbreviation of the family name "Kronseder") are designed to catch the customer's eye immediately. 3,000 breweries receive the first brochure from "Krones".
Success with semi-automatic labellers
The Krones St 1500 and Piccolo models are premiered.
A machine comprising just 150 parts: the St 1500, in steel construction, labels 1,500 bottles an hour on six bottle supports. The successor model Piccolo?, with its enclosed cast housing and a bottle table made of light-metal, can already handle 2,100 bottles an hour.
1953
The boss takes care of it
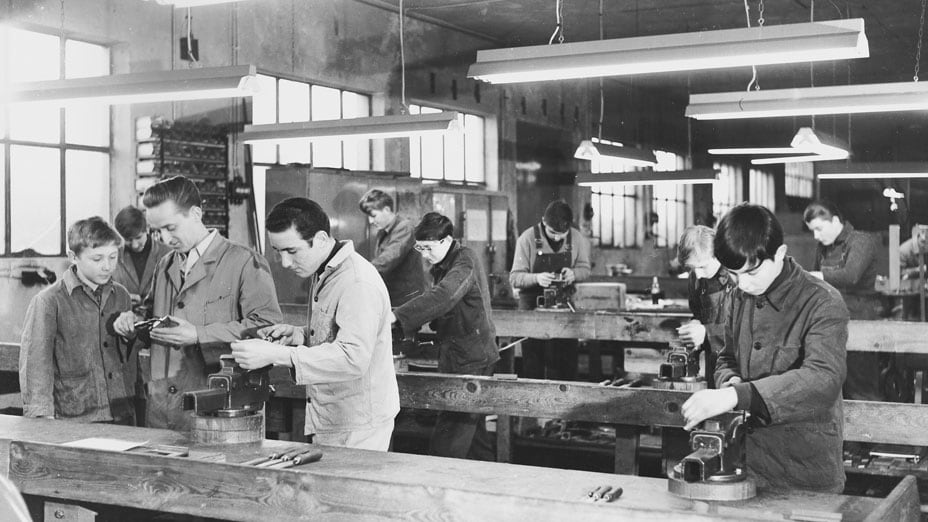
Very soon, Hermann Kronseder has his first employee to help with the production work. As from 1953, there are trainees as well: following a personal interview with the proprietor, and a handshake between the parents and the master craftsman, the youngsters kick off their careers as machinery mechanics.
1954
On-site erection
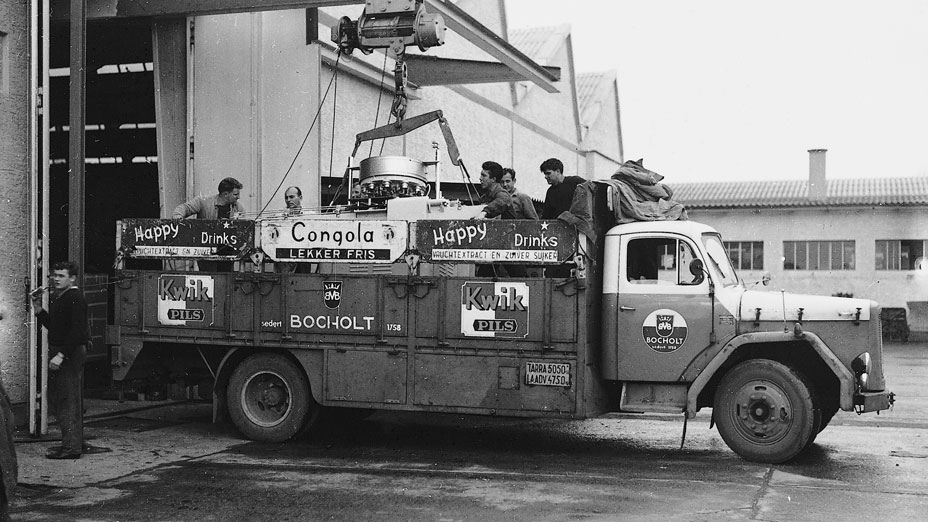
Comprehensive knowledge of the machines and a willingness to get your hands dirty are the best preconditions for erection jobs in these early years. The staff from the production hall thus come into contact with the clients and often build up personal relationships with the breweries' employees.
1956
The first automatic labelling capability
The Super labels up to 4,500 bottles an hour. This higher output is a result of "walking upright" - for the first time, the bottles are labelled standing up instead of lying down. This puts an end to the laborious insertion and removal of the bottles by hand.
1958
A professional presence
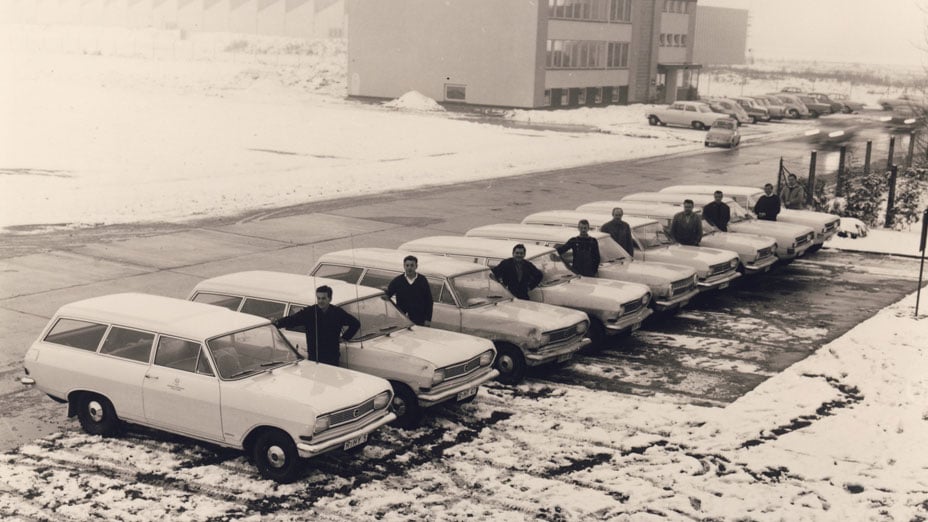
Eye-catching oval "Service" stickers on customer support vehicles symbolise a cornerstone of the company's success: comprehensive service support for the machines featuring fitters trained in-house, providing responsive on-the-spot assistance for the beverage plants involved.
1959
Precise information
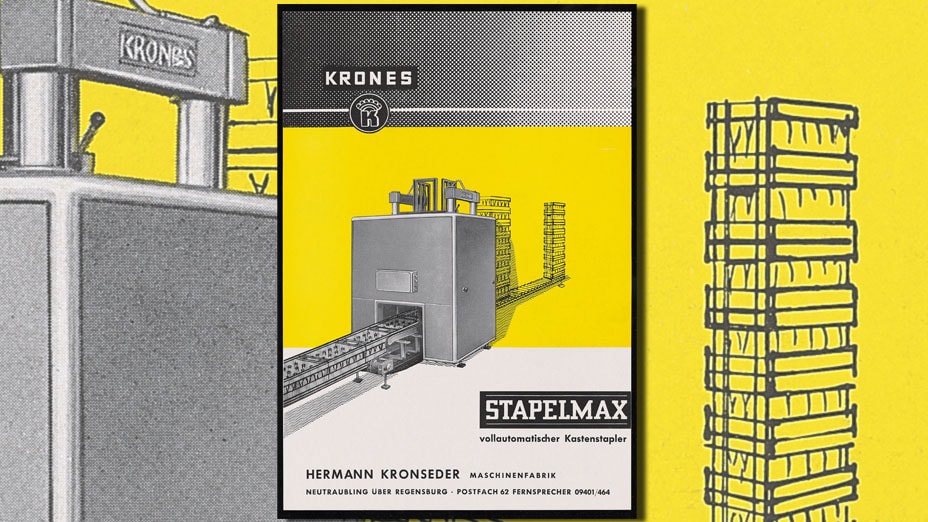
"The sector’s best brochures" - accurate, highly detailed information forms the basis for sales operations right from the start.
With technically informative, clearly formulated texts and photos showing the machines from the right perspectives, the client receives precise information on the kit concerned. Even though the machinery portfolio is still relatively small, the importance of advertising is very highly regarded.
The product portfolio expands
With the packer and unpacker (up to 1,800 crates an hour), Krones unveils smart solutions for other parts of a beverage plant - a line of business that in the mid-1960s is discontinued in favour of prioritising the development of labellers.
Easier stacking of beverage crates
Swing-stopper bottles weighing 800 grams have to be stacked in wooden crates - a daily routine for warehouse staff in the 1960s. With its Stapelmax, Krones eases their workload and ups the speed as well: 1,200 crates an hour can be simply and efficiently moved inside the warehouse.
The first press coverage
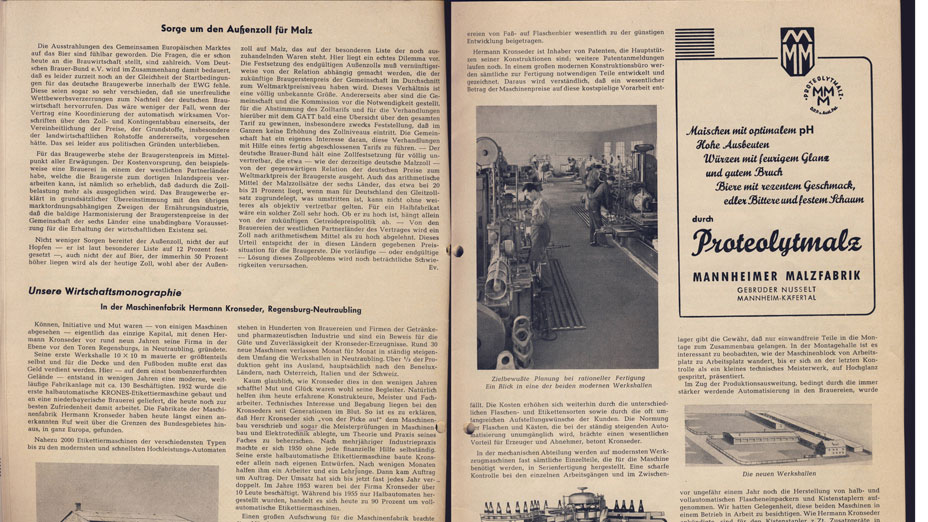
The magazine reports on the machines' high levels of dependability and the intensive commitment "of the owner, who spends far more than the normal amount of time working in the plant". Moreover, the change-over from draught to bottled beer provides more opportunities for the company to grow.
The first patent
For every technical detail in his labellers, Hermann Kronseder always asks himself if there isn't a simpler solution. Patent Specification No.1045312, "Feeding device for labels," is the first document reflecting the proprietor's continuous flow of inventive ingenuity.
1960
Brewing history - a tradition-steeped craft
What does a brewery's bottling hall look like in 1960? What do the staff have to do and how do Krones' machines support the production operation? The film shot at the Quentzer Brewery in Baden-Württemberg reveals quite a lot of history ....
1961
The Rotix - a machine with new label gluing
The labelling cylinder with vacuum suction nozzles removes the label from the magazine and guides it past the fixed-position gluing roller. The bottle is labelled as it passes. Rated at 50,000 bottles an hour, this is currently the world's fastest labeller.
The first export orders
The new packers meet with keen interest among Japanese breweries, and Hermann Kronseder becomes familiar with Japanese customs. The successful relationship with the Japanese partners is very soon supplemented by an agreement to produce packers under licence.
The company evolves
The steady uptrend continues - the first expansion of the production area becomes necessary. With an office now added, professionalised procedures are in place for business contacts and manufacturing operations.
1962
The Prontomatic
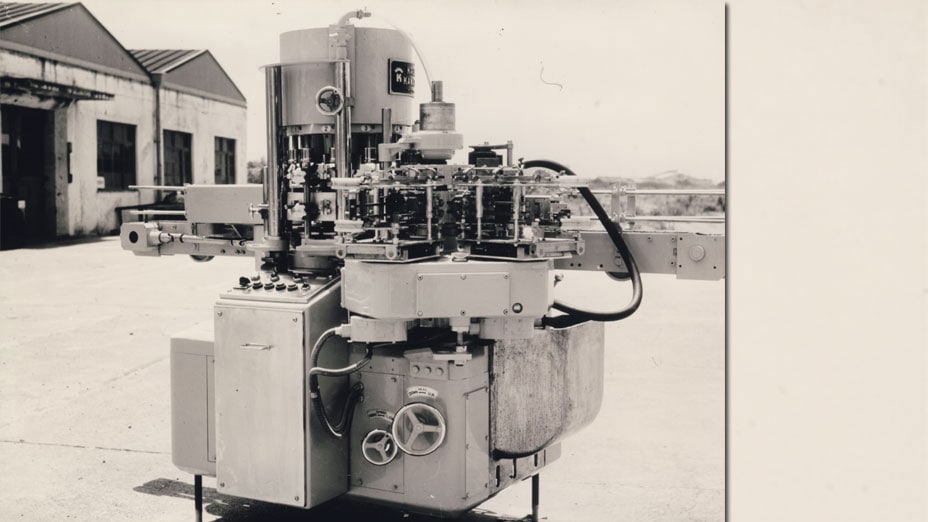
With simplified gluing and label transfer - for body and shoulder labels - and improved drive and housing construction, the Prontomatic is well received by the market. Thanks to its output of up to 24,000 bottles an hour, the machine is first choice for Japanese breweries.
The Employees' Council
Now, ten years after the company was founded, there are around 450 people working for Krones. By setting up an Employees' Council for representing the entire workforce to the owner, intra-company communication and staff welfare are handled in a mutually supportive spirit.
1966 – 1980
1966
Penetrating the US market
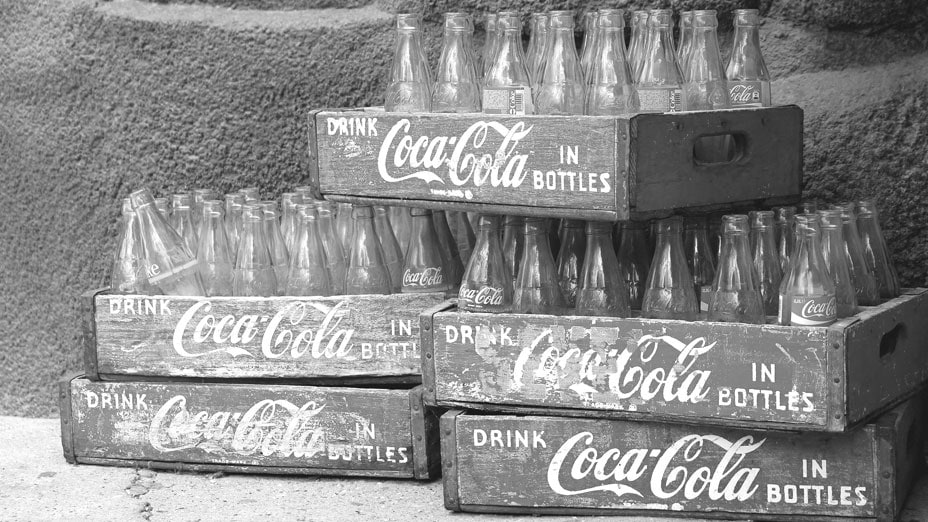
The American beverage producers are changing over from bottles with burned-in lettering ( ACL) to actual labels. For Krones, this is an opportunity to supply the American market with labellers. (Picture source: Rike / píxelio.de)
Exports - foundation for growth
Krones' own agencies in the USA and France constitute the first step towards cultivating the international markets. Meetings in the national language, rapid-response customer contacts - the beverage producers in the USA and the French vintners are soon persuaded of the machines' quality.
1967
New customers in the UK
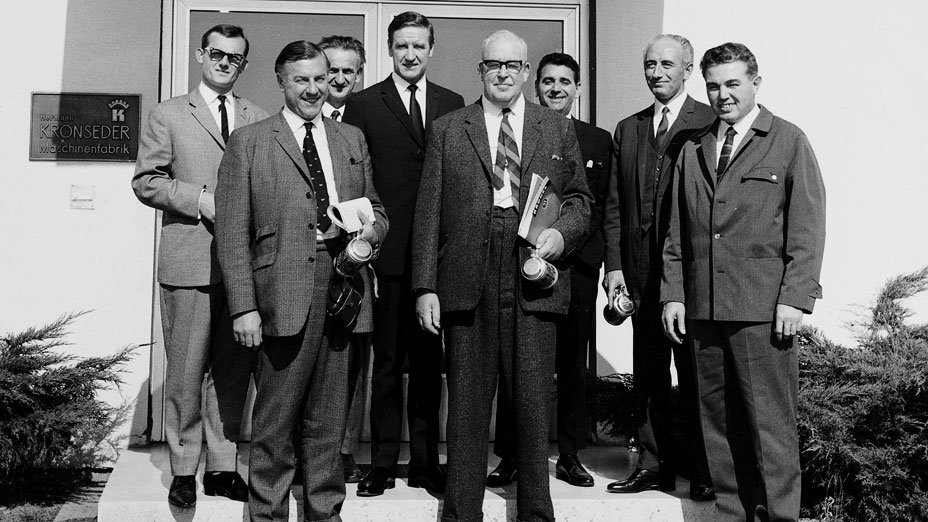
Modern-day marketing: a competition in an English trade periodical. The main prize: a tour of the plant in Neutraubling plus a visit to one of the brewery clients. This idea proves persuasive: Krones gains the first customer.
1968
A continuous flow of bottles
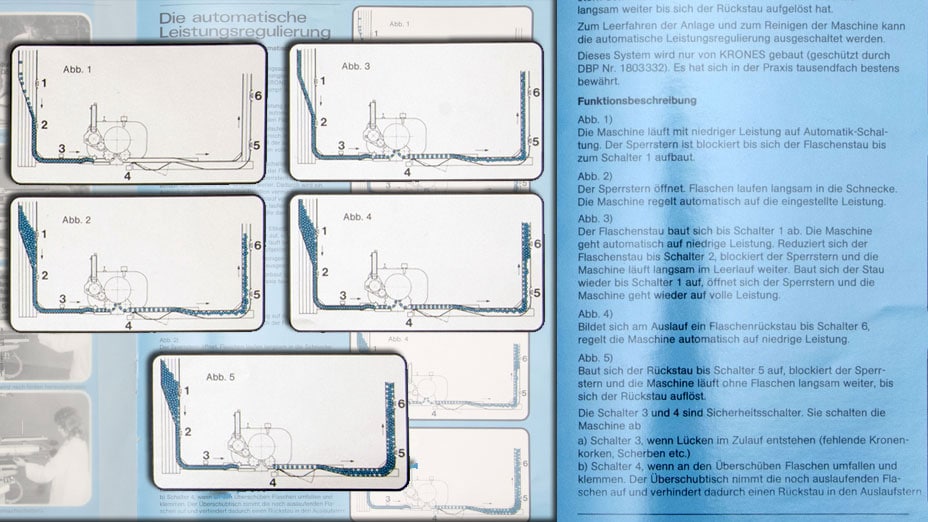
Irregular bottle feed had previously often led to malfunctions at the labeller. The newly developed bottle stop creates a continuous flow of bottles, so that several labellers can be supervised by a single person.
In tune with the times: the new logo
In 1968, a new design is introduced for the company's name, with angular, elongated letters. At first, it is frequently combined with the existing "K" logo. With bordered letters, during the 1970s it evolves into a contemporary-styled corporate logo.
1969
An inventor with the courage to innovate
A nostalgic backward glance to Krones in the 1960s. What do the workshops and the offices look like? With a precise view of the machines in the film, Krones was even back then using state-of-the-art cinematography to provide its clients with detailed information.
1970
A milestone for high-speed labelling
A fixed label magazine and the oscillating movement of the aluminium pallets for label removal enable outputs of 36,000 bottles an hour to be achieved. The label gripper on a rotating cylinder removes the label from the pallet and transfers it to the bottle.
Empty-bottle inspection
With the first empty-bottle inspector, visual monitoring of the empty bottles in a beverage plant is now automated. Till then, the detection rate was around 30 per cent, depending on how often the inspection personnel were replaced.
Spare parts deliveries - arriving promptly
Fast replacement of wear parts is the most important factor for successful high outputs in beverage plants. In order to assure clients in the USA a dependable supply of spares, these are dispatched over the Atlantic by air freight on the very same day.
Focusing on the target groups
With advertising rigorously focused on the target group involved, Krones puts the beverages' visual appeal on centre stage. Upmarket dress for bottles, for example, is combined with an appropriate social backdrop like sport.
1971
Labellers for every output range
Robusta, Universella, Supermatic and Starmatic are labellers for the output range from 4,500 to 30,000 bottles an hour. For the high output range, the Solomatic, rated at 60,000 bottles an hour, is premiered at the 1971 Interbrau.
1972
Extended workbench
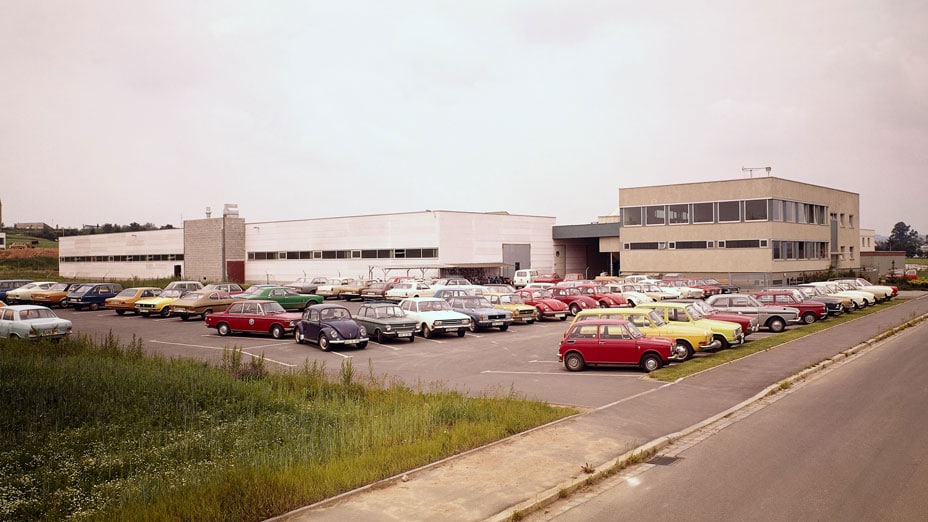
Additional production capacities are created with the branch factory in Nittenau.
Capacity upsizing with branch factories: at the new production facility in Nittenau, around sixty staff from the surrounding region are employed at first. Control cabinets and electronic equipment can now be manufactured in-house.
Eye-catchers indeed
Models from in-house provide extra publicity on the cover of the German brewing trade periodical "Brauwelt".
Models from the firm itself are prominent when in 1972 Krones advertises perfect bottle dress on the cover page of the trade periodical "Brauwelt". The captivating young ladies ensure Krones plenty of attention in the sector.
1973
Refills simplified
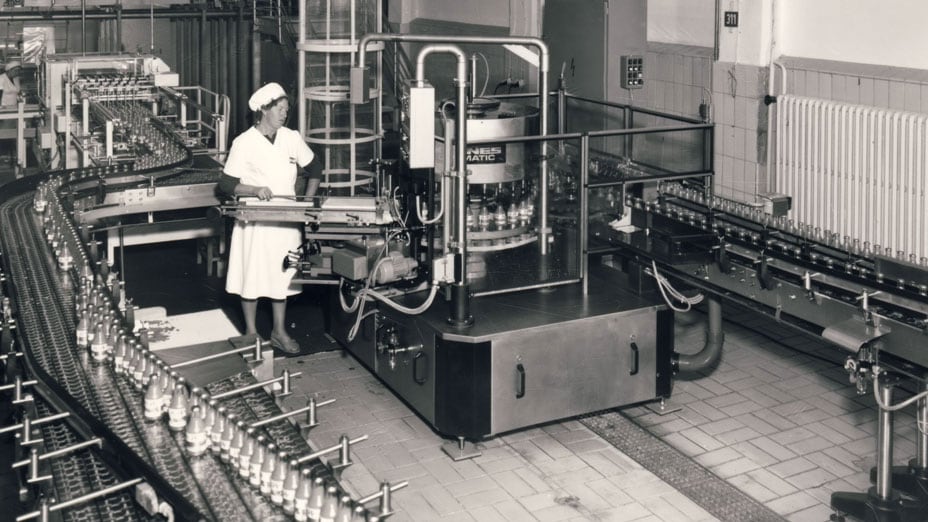
The label magazine enables the number of refill procedures to be reduced for high-speed machines.
At a machine speed of 50,000 bottles an hour, and given three labels per bottle, the operator has to continually refill the label magazines. With the Krones Magazine Pack (a reserve magazine), these refill procedures can be reduced to 20 an hour.
1974
Portfolio expansion
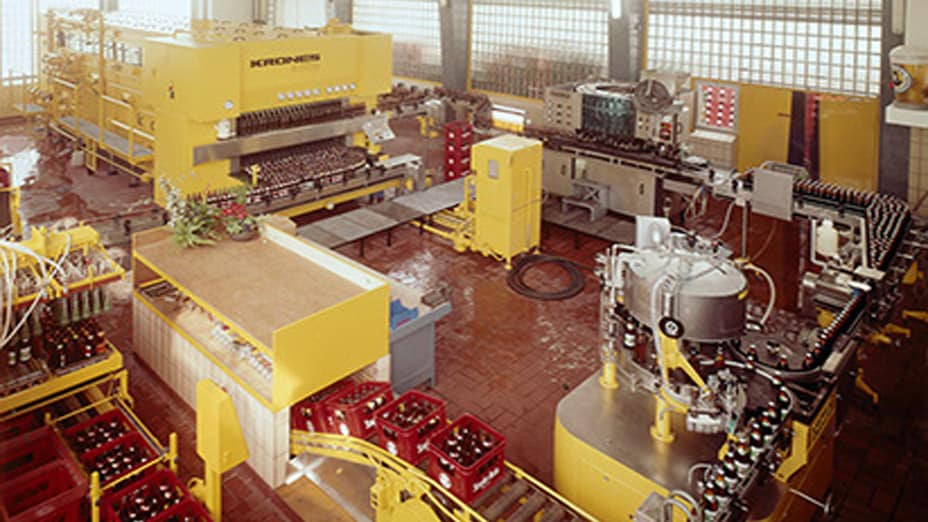
Bottle washers, too, fit in neatly with the portfolio. Contistella and Contiranta - these are the fine-sounding names of the "washing machines" from Krones' product range. The single-end, single-bath machines are available for outputs of between 5,000 and 30,000 bottles an hour.
New bottle guides for reduced noise emissions
With the newly developed polyurethane material, containers are guided in the bottling hall with less wear and lower noise levels.
Less noise, less wear and tear, less bottle breakage - this is how Krones advertises the new material polyurethane for bottle guides and infeed/discharge starwheels. Besides enhanced wear-resistance the material offers a 30 dB reduction in noise levels inside the bottling hall.
A new product line: filling technology
New in the portfolio: a filling system with a central bowl, initially conceived together with an associate. Whereas previously the labellers had often merely completed a line from another vendor, Krones can now offer the entire wet end with a filler of its own.
1975
Successfully serving the market
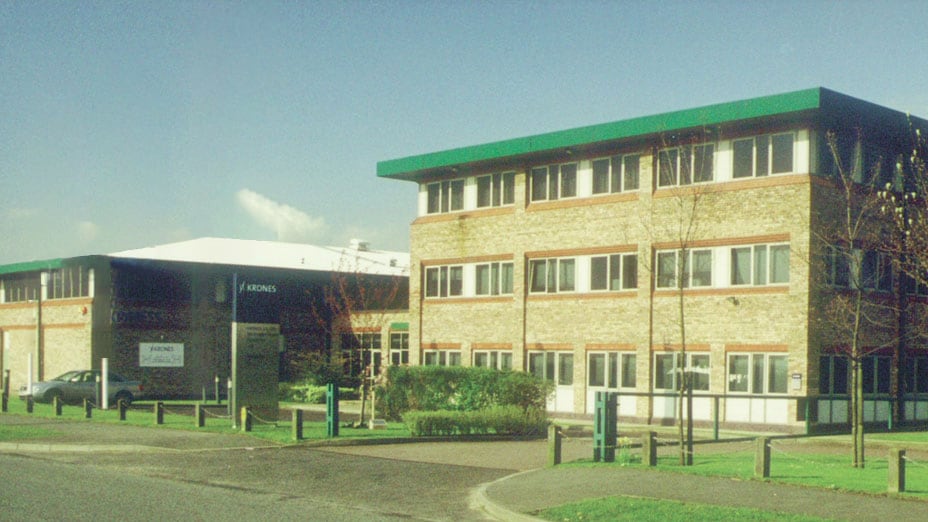
Tried-and-tested partners: the English agency (a long-serving specialist for Krones on the English market) joins forces with Krones to set up the subsidiary in the UK. This assures intensive support for this market as a long-term commitment.
Path-breaking
Linked directly without a conveyor: a monobloc comprising a filler, a closer and a labeller.
The Krones monobloc, comprising a filler, a closer and a labeller, has been designed to do without intermediate conveyors - back then an entirely outlandish machinery configuration. The thinking behind this idea was to simplify control of the machines using only a single operator. Today, this is the acknowledged state of the art ...
1976
Compact knowledge
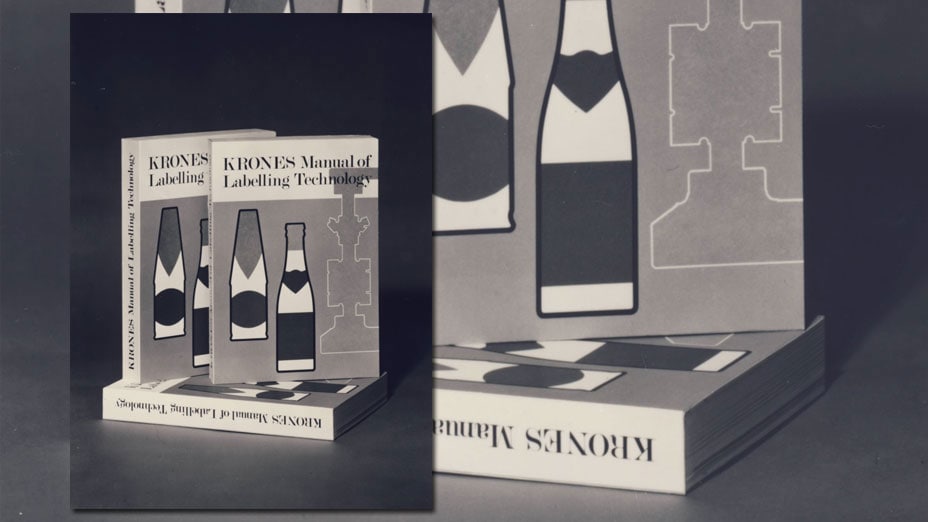
Krones is a service provider and a partner to its clients - the first Manual of Labelling Technology contains all the important things you need to know about labels and labellers. Because even back then, perfect functioning of the machines concerned depended on comprehensive knowledge of the labels, adhesives and mechanical engineering involved.
1978
Labelling with Krones
What defines the products' visual image on the market? Correct, the label. Intensive development work ensures that the client gets precisely the labeller that is suitable for his products.
1979
Clients' projects in the Krones Magazine
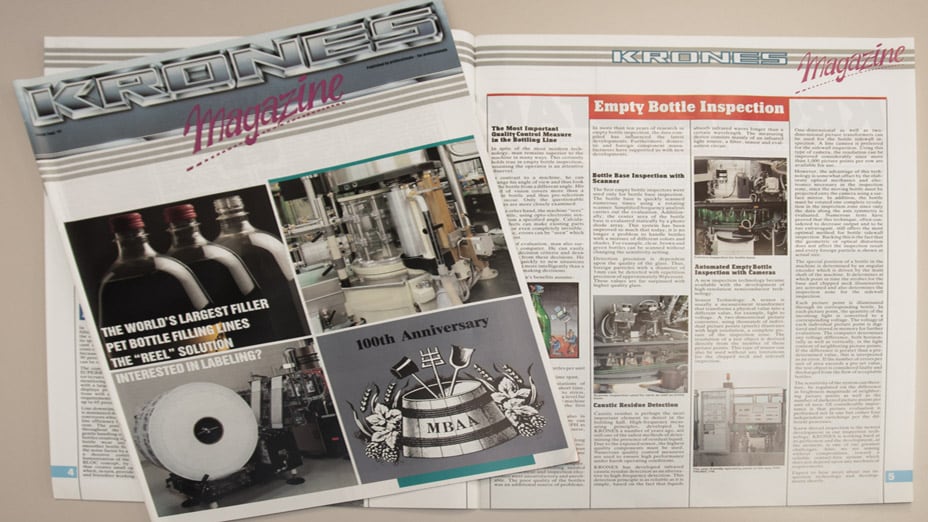
The Krones Information, initially as a typewritten circular, provides answers to technical questions and news of the latest references and machines. This keeps the firm in touch with its clients as is being done nowadays in a "slightly" altered form with the Krones Magazine.
Well-informed staff
Handy-sized and nonetheless informative - with the first issue of a staff newsletter, Krones offers all its employees a rapid overview of technical innovations and important orders, plus extensive lists of references.
1980
Growth
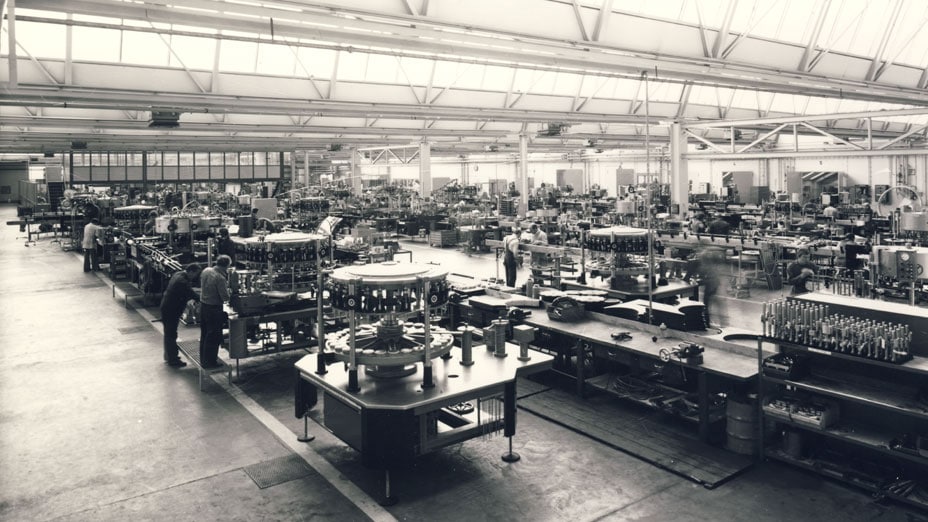
Construction projects in Neutraubling, Nittenau and Franklin, USA: a 3,000 m2 expansion in Neutraubling, new machine tools and a CNC-controlled large-size drilling machine in Nittenau, and production area upsizing in Franklin ensure improved delivery capabilities.
A significant change
In order to keep pace with the company's continuous growth, Hermann Kronseder converts what used to be Krones GmbH & Co. KG into a stock corporation. This legal form enhances confidence in the group's capital and management structure for international transactions with major accounts.
Can-do service support
Krones keeps all the essential parts in stock, and can thus at need swiftly deliver the desired spares to the beverage plants and breweries concerned. In the 1980s, around 200 staff are on duty round the globe in service support.
Precise technical presentation
Krones' brochures of the 1980s return to a technical depiction of the machines. Illuminatingly precise photographs highlight technical details and innovative solutions. Mechanical engineering is now complemented by electronics.
Labels conquer the whole wide world
Advertising is important - with information on its broad portfolio of labellers, Krones provides all its clients with insights into the technology and requirements involved in the labelling process.
On the spot in South America
Fast reachability is a cogent argument when it comes to penetrating new markets. The foundation of Krones do Brasil Ltda in Sao Paulo ensures rapid-response spare part deliveries and fast contact with clients in South and Central America.
1981 – 1995
1982
The company expands
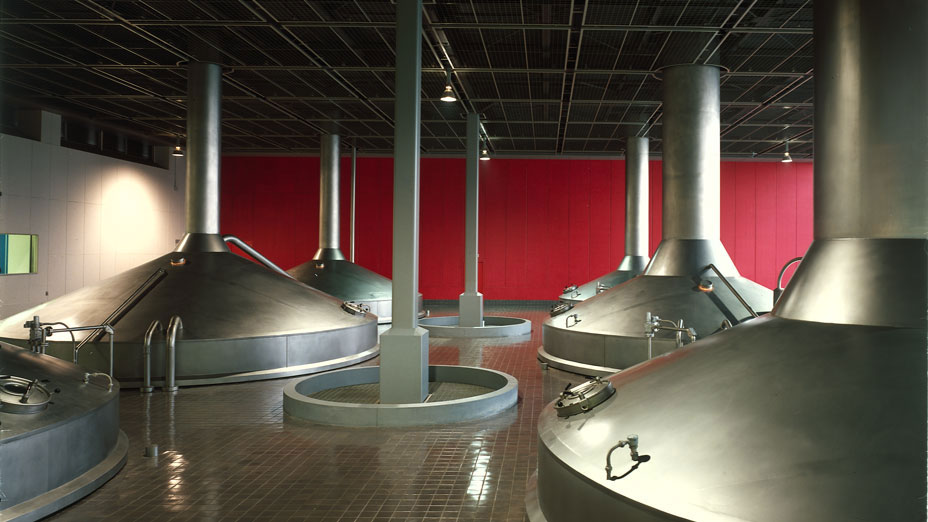
With a turnover meanwhile amounting to 210 million DM, Krones is an attractive partner in the beverage industry. By acquiring stakes in companies like the Freising-based brewhouse manufacturer Anton Steinecker Maschinenfabrik, Krones is now able to expand its product portfolio to include brewing equipment.
Conveyors - success on a slippery slope
The densely crowded flow of bottles on the conveyors between the machines often causes malfunctions in bottling operations. This problem is solved by the newly developed Glideliner, a conveyor combination with a slight slope and different speeds.
A monobloc featuring a bottle inspector
The Löwenbräu Brewery in Munich orders a Superbloc with an integrated inspector: with its speed of 50,000 bottles an hour, this raises machine monobloc synchronisation to new high-performance levels, and from now on is an integral part of filling technology concepts.
1984
New subsidiary in Japan

Rigorous market servicing: the business previously handled by a sales associate in Japan is now grouped together in Krones Japan Company Ltd. Thus for the first time Krones also has a presence in Asia with a sales team of its own.
A milestone in brewing process technology
At the time of the "second energy crisis", intensive thought is devoted at Steinecker on how to save energy in the brewing process, leading to the development of continuous wort boiling, in conjunction with the Research and Teaching Institute for Brewing (VLB) in Berlin and the Bergische Löwenbrauerei Brewery in Cologne, part of the Brau & Brunnen Group.
Successful IPO
Issuing shares at a price of 460 DM each puts the financing of Krones AG and its stock distribution on a new foundation. With this corporate refocus, public awareness of the company is strengthened, and its long-term survival assured.
1985
High-speed bottle inspection
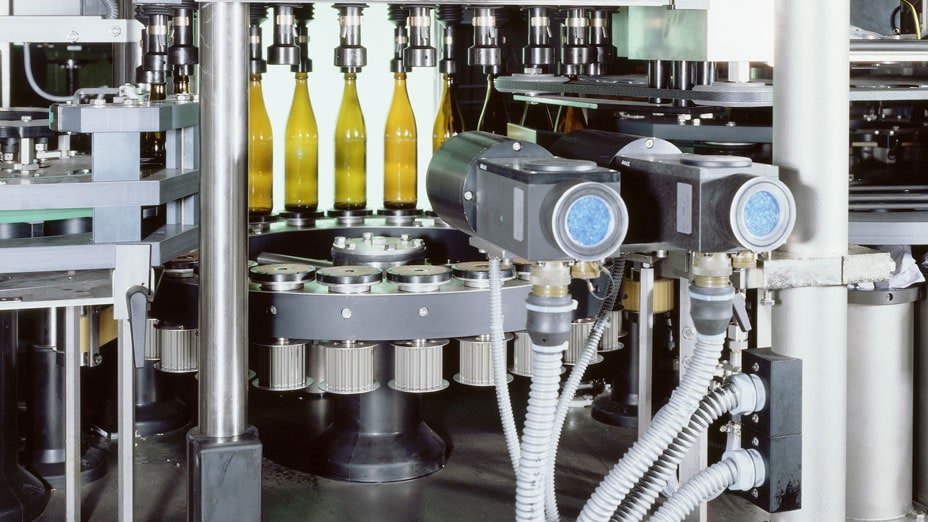
A technological quantum leap: instead of the previous rotating mirrors, camera technology from Japan is used. Electronic evaluation of the images acquired permits speeds of up to 55,000 bottles an hour.
Accurate fill levels
A new beer filler is premiered at the Interbrau in 1985. For bottling beer, three-chamber systems had hitherto been the custom, in order to avoid contact with the return gas. The Krones filling system, by contrast, even returns product to the ring bowl during the correction phase.
New glue roller - lengthy lifetime
Thanks to a design enhancement in the stability of the labelling station, the rubber glue roller previously used can be replaced by glue pallets made of metal. The new steel glue roller achieves a significantly lengthier lifetime.
Bottle dress with wrap-around labels
The driving force behind all development work continues to be a tight focus on the market. Dressing bottles in reel-fed wrap-around labels offers fresh options. With the Contiroll, Krones opens up another category of labelling for its clients.
1986
New: training courses for clients
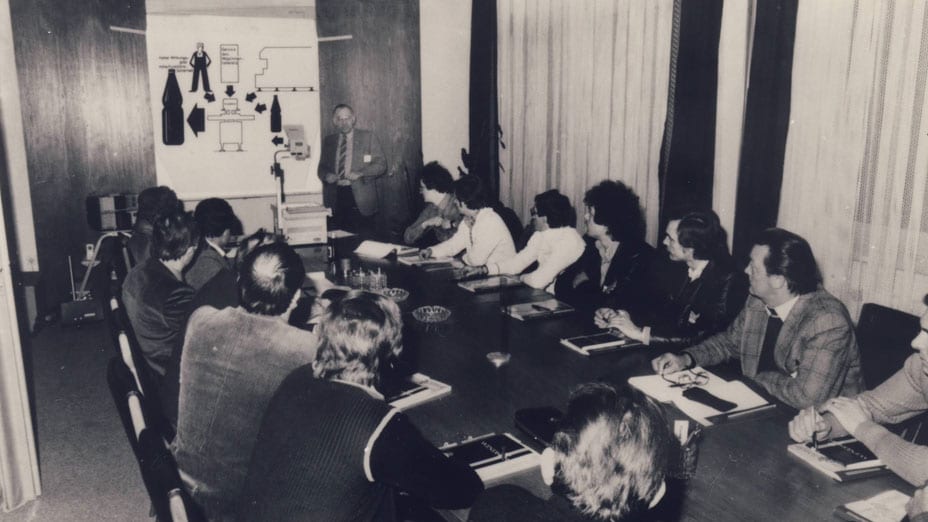
"Rigorous training and everything you need to know about inspectors", is what the new seminars from Krones offer. The training, and the personal contact with technicians from Krones AG, are extremely well received by participants in the initial seminars.
Togetherness
Some tennis enthusiasts having a friendly match to relax after work. The Krones Tennis Club is set up, and is soon playing in Regensburg's Business and Civil Service League. Other disciplines are soon added: football, table tennis, badminton.
1987
Into the future with PET bottles
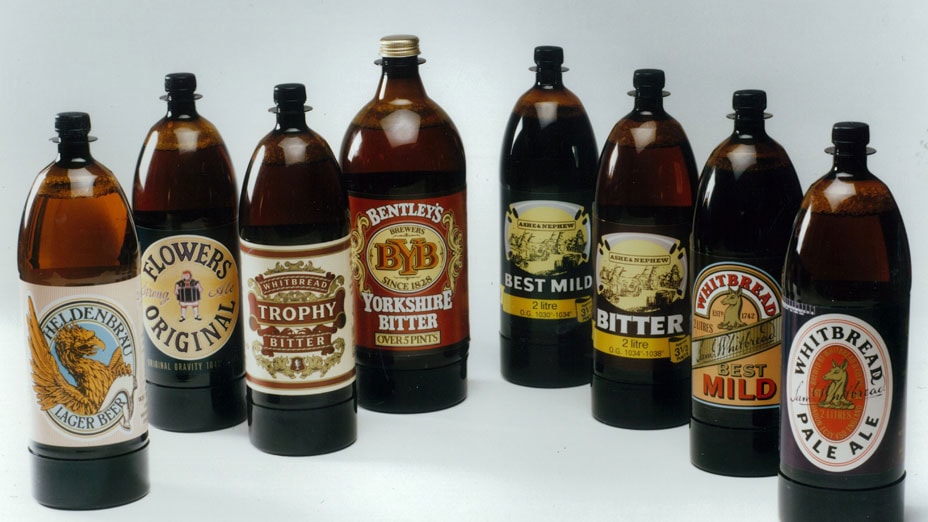
The PET bottle kicks off its career with Krones. First of all come filling systems with bottle plates, e.g. in long-tube design at the English Whitbread Samlesbury Brewery. The first filler with neck-handling goes to the Polar Brewery in Venezuela.
Service support for Jagenberg labellers
The news that Jagenberg AG is to discontinue production of labellers and transfer its aftersales support operation to Krones AG confirms Krones' status on its chosen market. The long-standing competition between these two companies has thus been decided.
The ABC of labelling technology
Machine operators are supported by precise instructions. With the film from the Service Department, everyone knows what he has to do.
1988
Service facility in the Far East

The growing importance of the Chinese market is already apparent in the 1980s. For rapid-response on-the-spot support of the Chinese clients with service specialists, Krones signs a service agreeement with China.
Alliance with China
Chinese government agencies and Krones sign a licensing agreement for manufacturing the Universella labeller with a rating of up to 24,000 bottles an hour. In addition, training courses are agreed in Neutraubling and in Guangzhao/PR China.
Bottle washers from Flensburg
Zierk, the Flensburg-based manufacturer of bottle washers, sells all its stock to Krones under a succession arrangement. With patents like rotary jetting units and the infeed and discharge concept, Krones is able to upsize its market share.
Training in China
Krones supports the foundation of China's first National Brewery College in Wuhan.
Basic and advanced training is a key issue. When the Brewery College in Wuhan is set up, Krones provides part of the technical equipment, thus enabling the Chinese students to benefit from hands-on training with state-of-the-art technology.
1989
Purposeful commitment to staff welfare
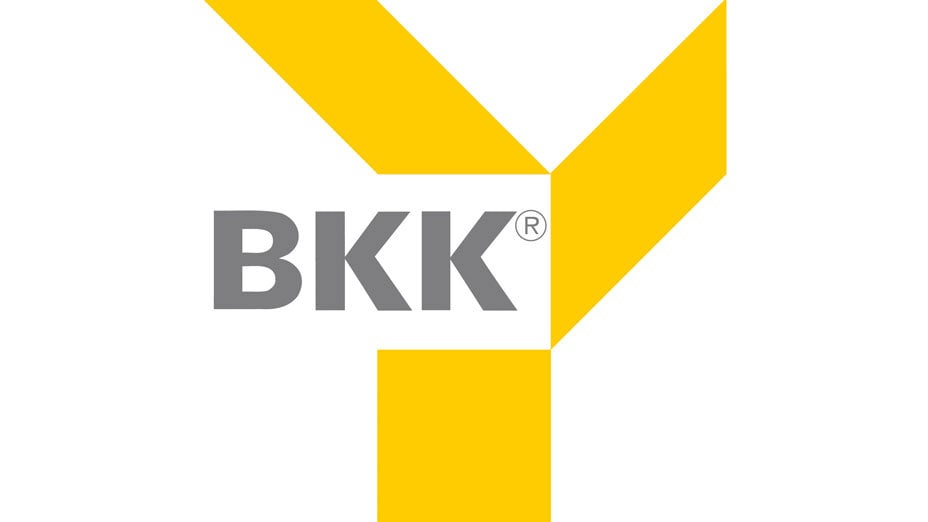
In order to give its employees an affordable option when choosing their health insurance provider, Krones sets up its own company health insurance scheme, designed to ensure high-quality preventive health care in the Krones BKK.
1990
Back in the portfolio: the dry end
The foundations are laid for the present-day concept of a complete-system vendor: the Roundpac, a packer/unpacker with a vertical path and continuous operation, and the Palmaster, a single-column palletiser, are premiered for the dry end.
Artistic brochures: the aesthetics of engineering
Harmonised brochure design with attractive machinery details.
Harmonised design of Krones' brochures is achieved during the 1990s. Their visual concept is based on large-size photographs of attractively portrayed machine details. Documentary images of the machines are replaced by the aesthetics of engineering.
Inventor's Oscar
Hermann Kronseder is awarded the Diesel Medal in Gold.
The ultimate recognition for inventive ingenuity: the German Institute of Inventions awards the Diesel Medal in Gold, and the Faculty of Brewing, Food Technology and Dairy Science at TUM (Technische Universität München - Munich Technical University) awards an honorary doctorate to Hermann Kronseder in 1993.
1991
Electronics for filling technology
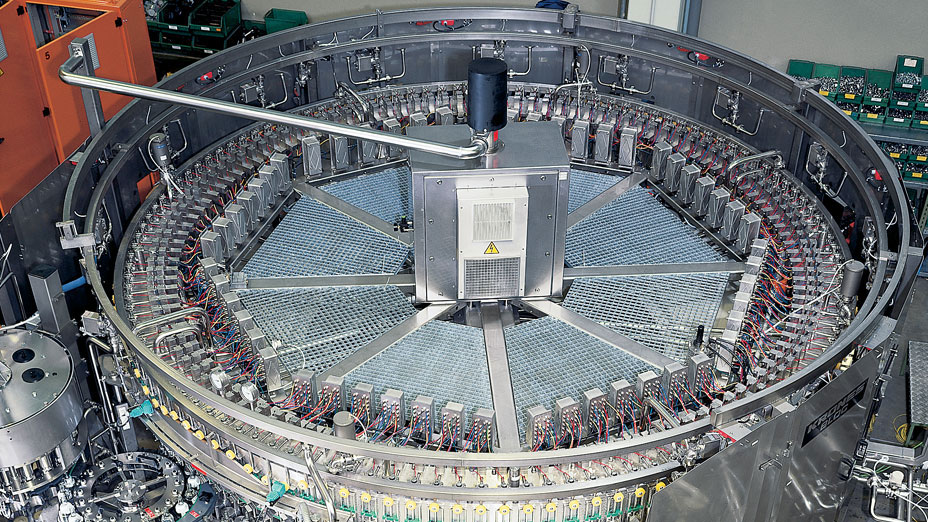
The development of electronic modules reaches the beverage industry: the filling systems, purely mechanical up to then, can now be fitted with electronic actuation. Krones offers this for the first time in the early 1990s, in the shape of the Sensometic filling system.
Automation in the brewhouse
PCs enable the brewer to track the brewing process: the Botec process control system documents all the functions concerned and logs the production data. The modern-day brewer can thus control all the sequences involved in the brewhouse from his screen.
1992
Energy-economy
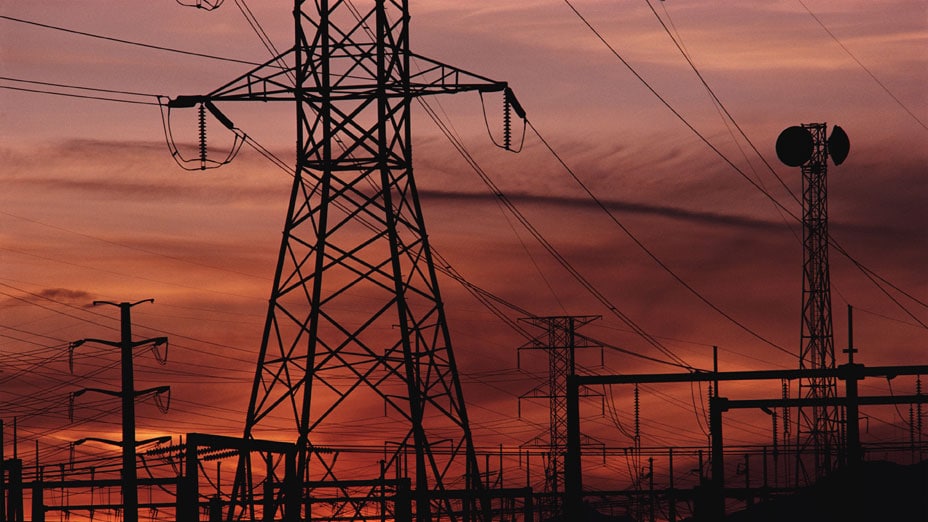
This supplement to the energy supply concept at the facility in Neutraubling provides a thermal ouput of 2.99 MW, corresponding to an electrical rating of 0.99 MW.
The superbloc with a touchscreen
NT technology is the keyword for inspector design in the 1990s - with the large-scale order from the Thurn and Taxis Brewery in Regensburg for installing a new Superbloc, a touch-screen for operating the machines is premiered in the bottling line.
Beer-sterile filling
Steam-rinsing the bottle prior to filling is designed to ensure a high level of hygiene in filling operations, so as to achieve an improved shelf-life for the beer. The steam surge, which lasts 1.5 seconds, can be regarded as a preliminary stage in the development of aseptic filling systems.
1993
A global presence
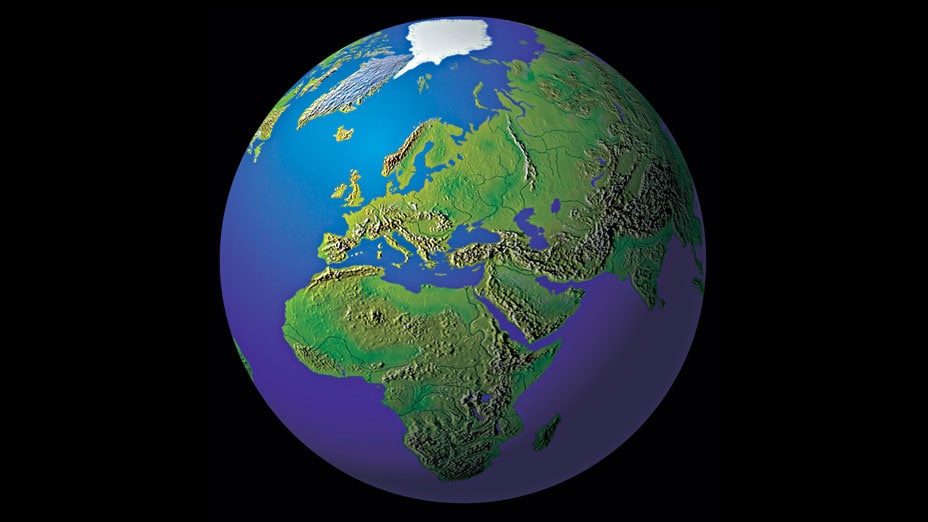
In line with the firm's corporate philosophy of preferably serving the market through subsidiaries of its own, Krones opens agencies in South Africa, Venezuela, Argentina, the Czech Republic and in the Netherlands.
Music on the factory floor
With seating of 1,116 people, plus orchestra and choir platforms accommodating a total of 200 performers, a factory hall in Neutraubling is the venue for a rather special event: Ludwig van Beethoven's 9th Symphony is presented in one of the production halls for fillers and labellers.
1994
Certified can-do competence
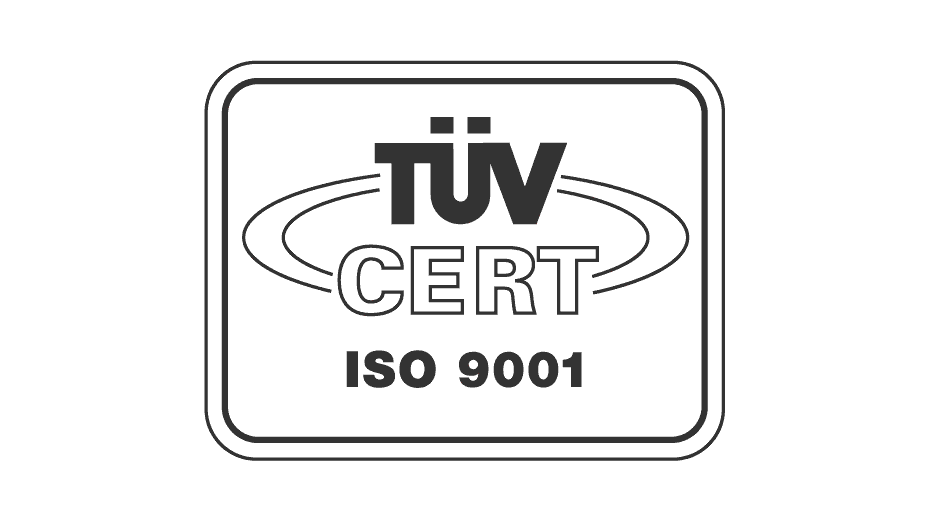
Trackable business processes are guaranteed by certification under ISO 9001. With this set of standards, now being adopted more and more widely, Krones puts in place a consistently harmonised quality management system for its operational procedures and for a process of continuous improvement.
Customer satisfaction in figures
The filler with the serial number 1,000 is a volumetric can filler with 125 filling valves, which is installed at the Macardle Moore Brewery (part of the Guinness Group) in Dundalk, Ireland. The machine is rated at 1,200 cans a minute.
Evolving into a complete-system vendor
Following changes in the shareholder structure at Steinecker, there is an opportunity to acquire a majority holding in Steinecker and integrate it into Krones AG. The concept of operating as an all-inclusive vendor for brewery technology is thus coming gradually closer to realisation.
1995
Fast availability for Chinese clients
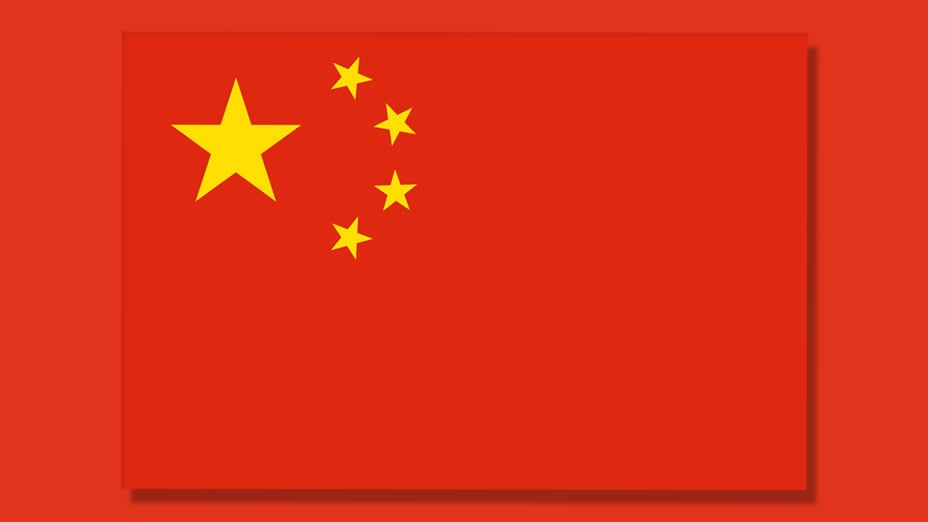
With major investments being made by Chinese beverage companies, fast contacts in line with Chinese business practice are vital. Krones is the first European packaging machinery manufacturer to set up an office in Beijing.
The world's biggest can filler
South America's two biggest brewing conglomerates, Antartica and Brahma, opt for the can as their beverage package. Three Volumetic high-speed fillers are delivered, each rated at 120,000 cans an hour, and with a carousel diameter of six metres.
Huge order from China
The biggest order so far in Krones AG's entire history covers the delivery of a new brewery with an annual output of 1 million hectolitres, plus the expansion of the existing brewery to reach an annual output of 1.5 million hectolitres.
The filler in a cleanroom
As an "up-to-the-future pilot line", Krones unveils a new line at Coca-Cola Radeberg. After being washed, glass and PET bottles are passed into a cleanroom, and via a tunnel filled with sterile air from the rinser to the Sensometic VP-VI-BSF filler.
1996 – 2010
1996
A new man at the helm
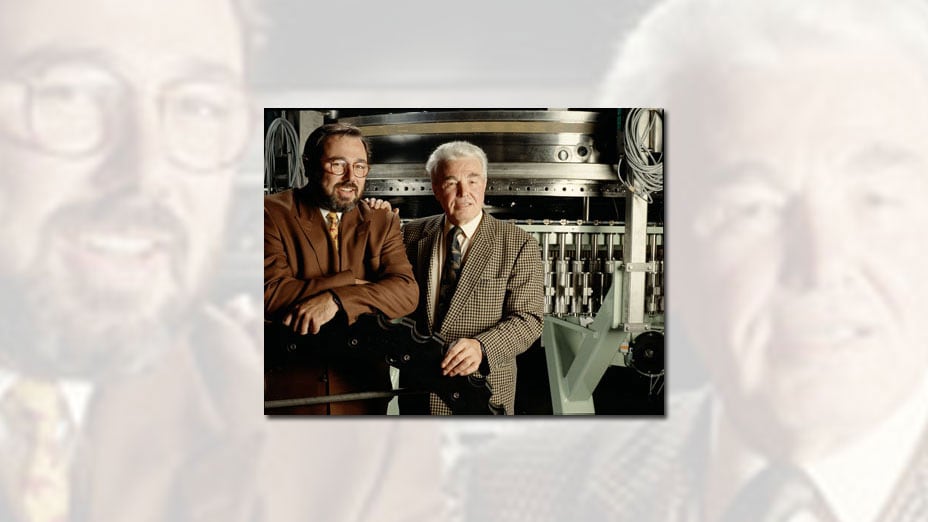
Krones is employing almost 7,600 people in the group worldwide. This is the basis for Volker Kronseder when he takes over as Executive Board Chairman. After 45 active and fruitful years in his company, Hermann Kronseder moves to the Supervisory Board.
Spiragrip
The lightweight, heat-sensitive, returnable PET bottles necessitate special conditions. The new Spiragrip washer guides the lightweight bottles dependably through baths with moderate temperatures suitable for handling PET.
Online!
Always at the leading edge of contemporary advances: the new options offered by the internet are for Krones an exciting opportunity for communication. Under www.krones.de, you will find extensive information on the company and its product portfolio - illustrated with a jolly matchstick man.
Anything that flows
The continual search for additional lines of business and a logical path forward for the company's evolution bears fruit: a ketchup filler is sold in the Netherlands. This is made possible by using flow-metered quantitative measurement in the filling system.
1997
An expanding market for PET bottles
A compactly dimensioned two-storey machine for warming up the preforms and stretch blow-moulding them on a footprint of just 12 m2 is the solution for the future-friendly market of PET bottles. Approving feedback from the major soft-drink bottlers as well confirms the successful start of this technology.
Robot technology for palletising
Complex work sequences are no problem for the new Robogrip packaging and palletising robot. A rotary movement of 360°, four user-programmable movement axes, and carrying capacities of up to 155 kg provide abundant scope for handling a wide spectrum of different bottles and packs.
Packing and palletising technology added
Krones takes over part of the insolvent Kettner GmbH in Rosenheim.
Max Kettner GmbH has an enviable reputation in the sector for packers and palletisers. Following a series of flawed strategic decision-making, however, the company has to give up. Krones acquires some of its divisions, and groups together packer and palletiser production in Rosenheim.
1998
Continuous beverage blending
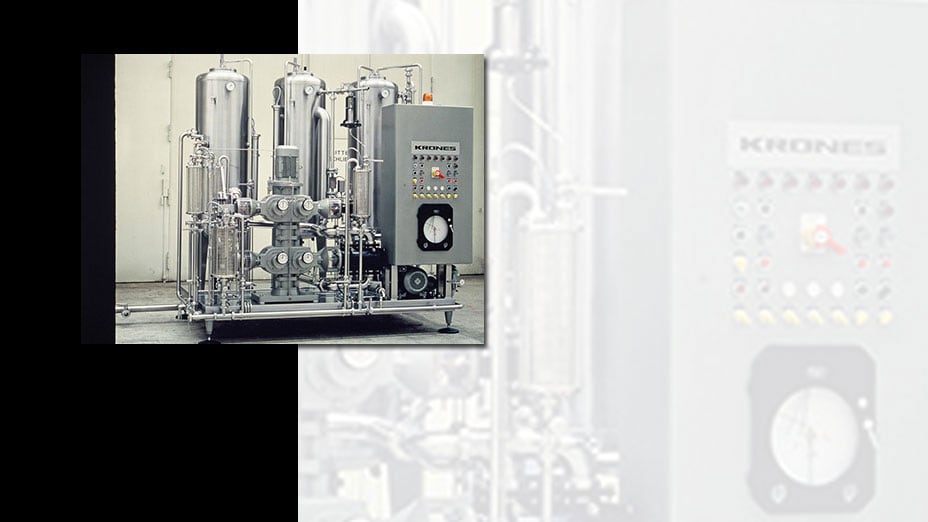
The product portfolio is steadily expanded: to coincide neatly with the Intervitis trade fair for fruit juice and wine producers, the MSF mixer is unveiled - a compact system for blending and carbonating beverages.
It's direct contacts that count
The Russian market is growing. In order to support further progress in Eastern Europe and Asia with rapid-response on-the-spot capabilities, the subsidiary Krones o.o.o. is founded in Moscow.
1999
Sleeve labelling
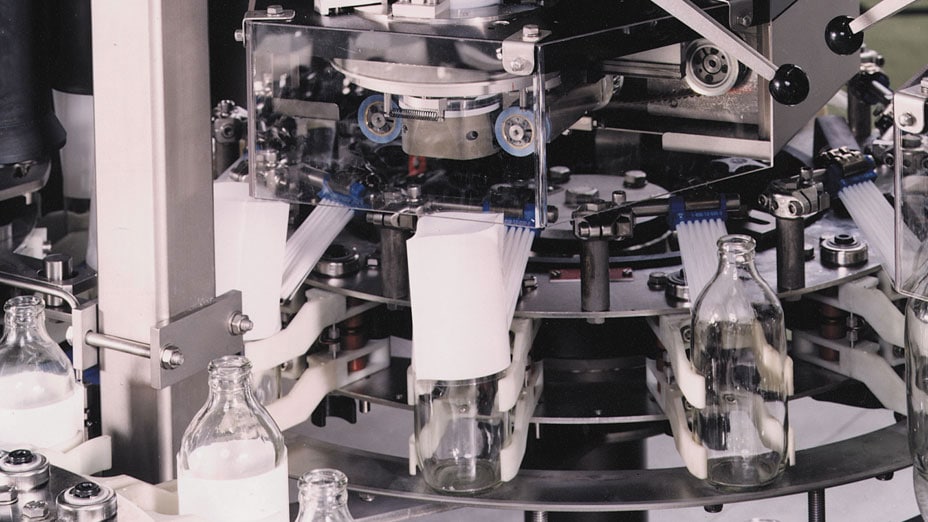
With the Stretchmatic, Krones offers a labeller for applying sleeves: this rotary machine dresses PET bottles in sleeve labels that are pulled onto the bottle as a tubular film and then shrunk onto the bottle's contours in a steam tunnel.
On the spot in person
Successful teams look after the national markets of Kazakhstan and the Ukraine. In India, a subsidiary is set up in Bangalore. At the beginning of the new millennium, around 1,400 staff are working in Krones' subsidiaries abroad.
The first environmental prize
The energy-intensive brewing process is optimised at Steinecker in numerous development projects: the sectoral experts pay recognition by awarding Steinecker an Environmental Prize in 1998 for the Ecotherm internal boiling system and in 1999 for Merlin.
2000
Fit for the future with IMPULSE
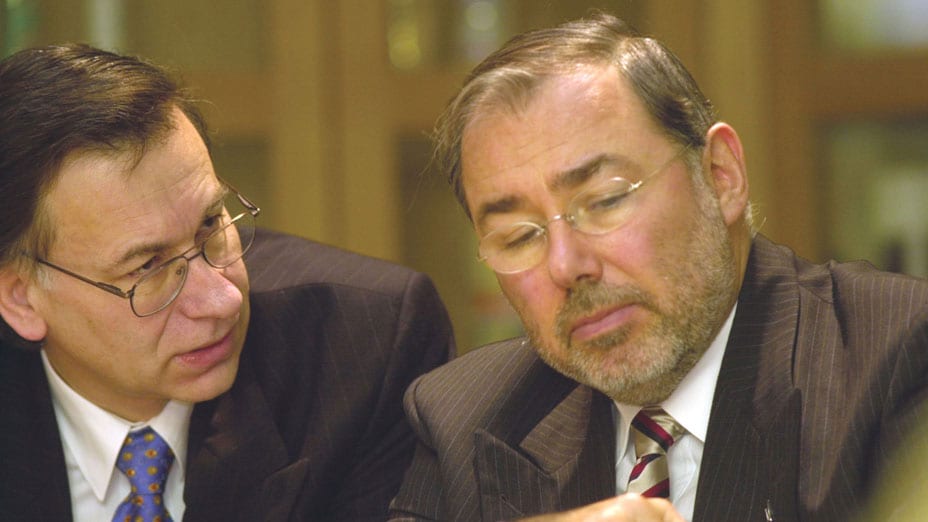
With IMPULSE, Krones launches a programme for the company's future development. By identifying superordinate strategies, the initiative aims to drive forward more effectively staff's identification with Krones and to upgrade their professional skills.
Wort boiling with Merlin
The new concept of passing a thin film of wort over a cone enables a total evaporation of just 4 % to be achieved, with concomitant energy savings in the brewing process. In addition, the system scores highly in terms of taste stability and beer quality.
Gable-type tabletop sets a new trend
The modified design for the previously level surfaces of the filler's front table is simple, but effective. A hipped-roof-style construction enables liquids to drain off automatically. Today, this is the standard option for hygiene-enhanced filling concepts.
A new level of convenience in procurement
Aftersales service support is upgraded still further by introducing eBusiness in spare parts operations. With Krones eGate, the electronic procurement catalogue, clients select the spares they want, clarify their availability, and trigger an online purchase order.
IT and intralogistics
Important building blocks for complete lines.
The flow of information is gaining steadily in importance. New IT solutions for production data acquisition, process control systems and intralogistical concepts enable Krones to operate as a complete-system vendor for the entire process chain in beverage plants.
Trend towards non-returnable containers
The new Variopac and Wrapapac packers ensure dependable secondary packaging on the way to the retailer.
With systems for film packaging of containers and for packing containers in full-depth cartons, the packer specialists in Rosenheim unveil machines designed to meet the ongoing trend towards compact-size packs for non-returnable containers.
Responsively communicative
Modern logos and a new corporate design are introduced for the parent company and its subsidiaries. The pictograph shows two stylised arrowheads, slightly offset, symbolising dynamism and purposefulness. The company name follows in slimline lettering.
2001
Comprehensive production data
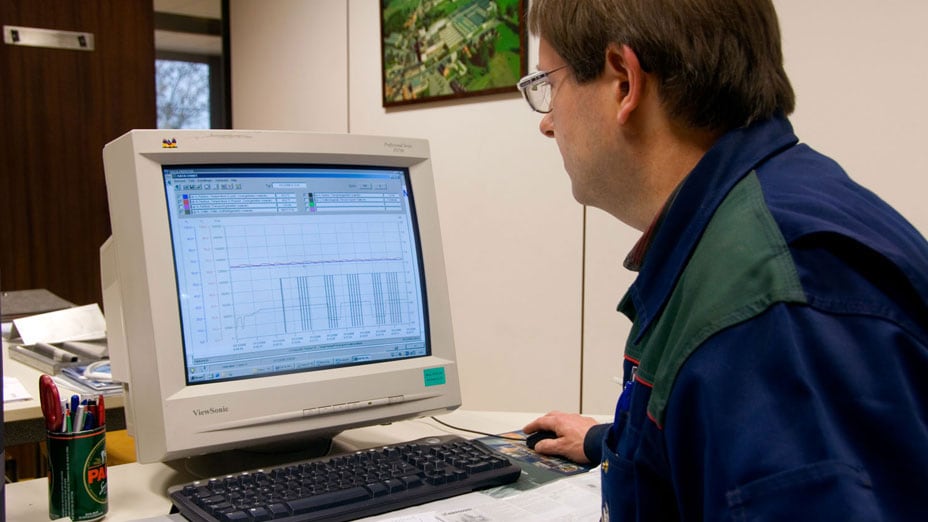
The LDS acquires and documents all production and process data in a filling and packaging line. The data recorded can be used for evaluating efficiency levels, monitoring quality or for analysing malfunctions.
A new concept for the stretch blow-moulding machine
Speed counts for beverage bottlers. The Contiform S, a design-enhanced stretch blow-moulding machine, offers an output of 1,600 bottles an hour in one blow-moulding station. This is achieved by reducing the number of transfer points for preforms and bottles inside the machine.
The monobloc idea extended
The continuingly rising share of PET bottles in the packaging mix triggers the development of the blow-moulder/filler monobloc. The Contiform Bloc combines a blow-moulding machine and a filler, has a minimised footprint, hygienic design, and manages without any conveyors between the machines.
The innovation for labelling
The modularised machine is a true innovation in labeller design: a basic machine to which the labelling station required at any one time is docked. This modularised system is Krones' response to ever-smaller product batches and frequent dress change-overs.
2002
High performance in the brewhouse
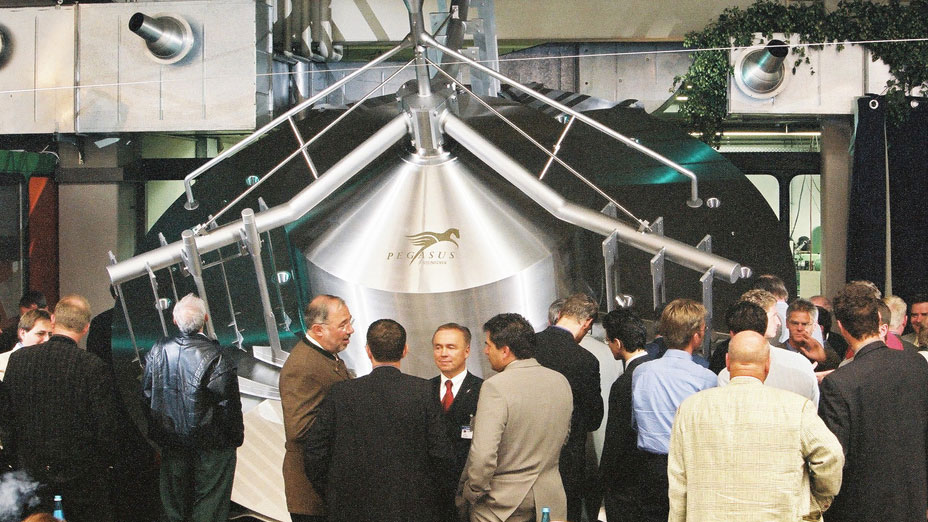
The newly designed lauter tun enables high outputs to be achieved in the brewhouse. Salient features of this innovative lautering system include a flow-optimised configuration for the mash feed, and fast extract removal thanks to a new arrangement of the sources.
Enhanced hygiene for canned beer
For the first time in Brazil's brewing industry, there is a Taxomatic labeller up and running, fitting foil to can lids as hygienic protection. The first user is the Petropolis Brewery in Rio de Janeiro State, with its Crystal and Itaipava beer brands.
Krones' debut in milk bottling
The foaming characteristics make it difficult to use traditional level-controlled fillers for milk. But for volumetric fillers, its conductivity is too low. This is why Krones introduces a new filling system with a weighing cell, ensuring an ultra-accurate filling function.
Bottle-to-bottle recycling
Recycling PET as a raw material becomes a constituent part of the corporate stategy. To make PET available for re-use in bottle production, concepts for bottle-to-bottle recycling are examined, and included in the Krones portfolio.
Accurate ampoule labelling
For the Aventis pharmaceutical group, Krones develops a self-adhesive labeller to pharmaceutical standards with a high output of 60,000 cylindrical ampoules per hour. The machine dresses glass ampoules with nominal volumes of 1.7 and 3 millilitres.
42,000 bottles an hour
The biggest PET-Asept line so far built by Krones has been operating at St-Alban-les-Eaux, France, since the beginning of 2002. The contract bottler of brands like Lipton Ice Tea is now running its production line at speeds of up to 42,000 bottles an hour.
2003
Stromboli - the new generation of internal boilers
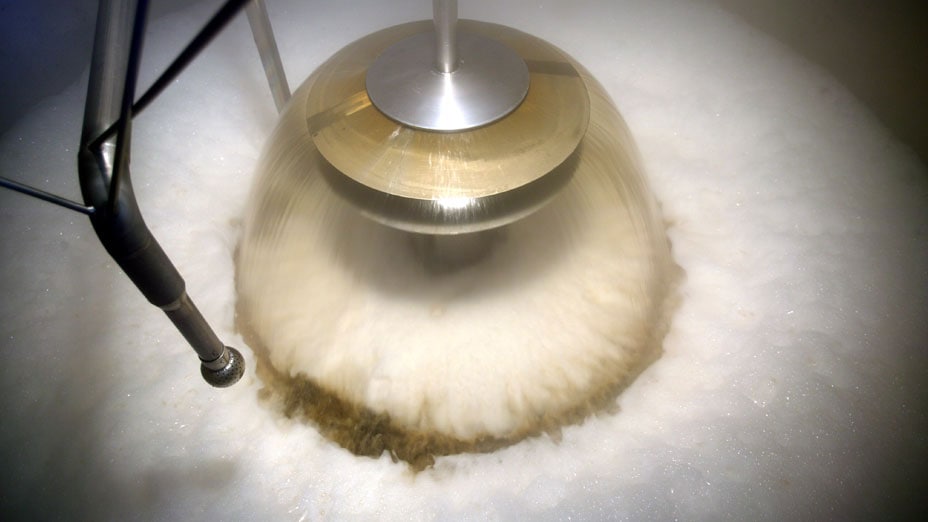
The combination of pump-assisted wort recirculation and natural recirculation in the Stromboli internal boiler improves still further the energy balance in the wort boiling process. This retrofittable system is (after Merlin) another step forward in the thrust for gentle wort boiling coupled with low total evaporation.
The specialists for small outputs
By acquiring a stake in the Kosme Group, Krones offers mid-tier clients attractive first-time-user models. The Austro-Italian group produces fillers, labellers and packers, plus inline stretch blow-moulding machines for the low output range.
LCS Lifecycle Service
Service capabilities are of paramount importance for beverage machinery manufacturers. In order to assure continuous support for the clients and machines involved, the entire maintenance and repair business is grouped together in the Lifecycle Service (LCS) Division.
Corporate competence in plastics
One of Krones' biggest investment projects is the Centre for Plastics Technology, completed after 15 months of construction work. Seven Contiform laboratory stretch blow-moulding machines and numerous testing facilities provide a comprehensive foundation for future development projects.
2004
Knowledge for everyone
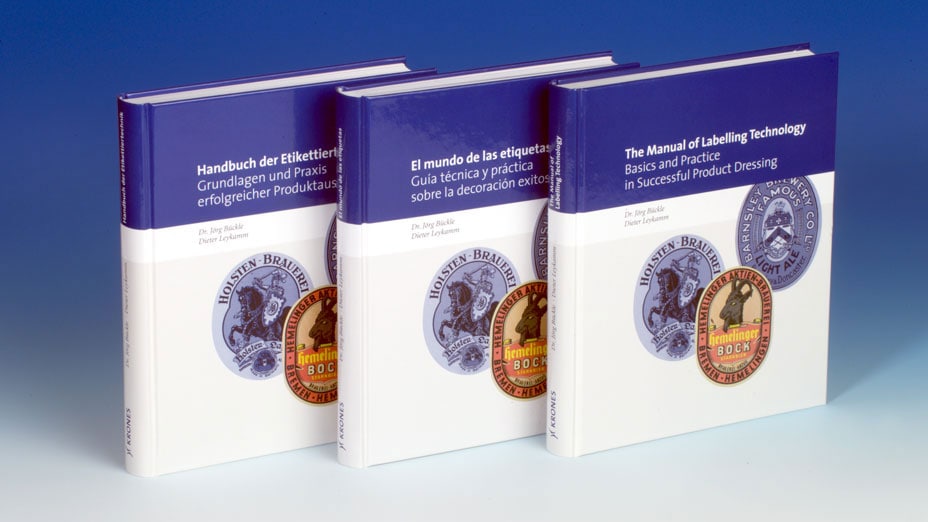
Following the revised edition of the Manual of Labelling Technology, Krones publishes the Manual of Filling Technology and the Manual of Packing and Palletising Technology. This continues a tradition of offering compact reference books on the technology used in the beverage industry.
Global premiere
Latte di Brecia, Italy, is the first dairy in the world to bottle milk with a 90-day shelf-life in 1.0-litre and 0.5-litre PET containers. Krones supplies the aseptic filling technology: a compact PET-Asept line plus a Contiform S for producing the PET bottles.
An ugraded presence on the stock market
In order to increase the attractiveness of Krones' shares on the stock market, the preference shares, hitherto without any voting rights, are converted into ordinary shares. With this measure, 46 % of the stock is now in diversified ownership. The Kronseder family holds 54 % of the stock.
New service centre in China
The very substantial growth rates on the Chinese market lead to a further strengthening of the firm's presence in China. The establishment of a production facility for spare parts and a training centre contribute towards comprehensive service support for China's beverage producers.
Shaping the future together
First-class training of the staff, and their highly motivated commitment, are the foundations of the company's success. With investments in the German facilities, and increased trainee numbers, Krones is preparing prudently for the future. In return, a flexible worktime scheme is introduced.
2005
Telesupport
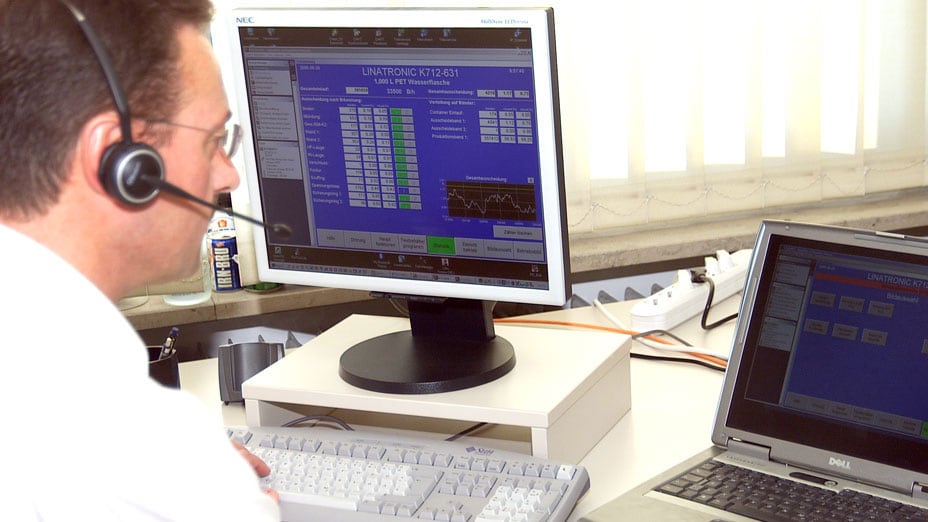
With its Teleservice capability, Krones is able to establish a link to a machine's control system over the telephone network. This means Krones' machinery specialists can check parameters, analyse malfunctions and remedy these directly.
ShakesBeer
A newly conceived heating system and a flow-optimised agitator provide a technological upgrade to the mashing process. Higher mash quality, shorter mashing times and significantly reduced energy consumption are the advantages for breweries who opt to use ShakesBeer.
Completely automated
The mutually harmonised IT process control technology for production, packaging and logistics ensures maximised transparency. Thanks to the comprehensively comprehensible displays of process steps and production data, plants can operate more flexibly and run their production operations more efficiently.
Hygiene-enhanced filler concept
The new filler, with its tubular ring bowl, integrates improved-hygiene technology. The surfaces have been downsized, and the filler's front table is now no longer necessary, since the system operates with servo-drive technology and does without mechanical drive components.
Synergised knowledge
Practical applications are purposefully prepared with state-of-the-art pilot plant equipment.
Development work and product testing require perfect technical equipment. With investments in a Filling and Process Pilot Plant, the Filler Centre and the Technology Centre, the company's technological lead is progressed, and capacities created for client-specific testing.
Best overall strategy
The optimisation of all business and production processes is being continuously progressed. The award of the Mechanical Engineering Strategy Prize at the German Mechanical Engineering Summit shows that the business community, too, has taken note of how effective Krones' initiatives are proving.
2006
red dot design award for mechanical engineering
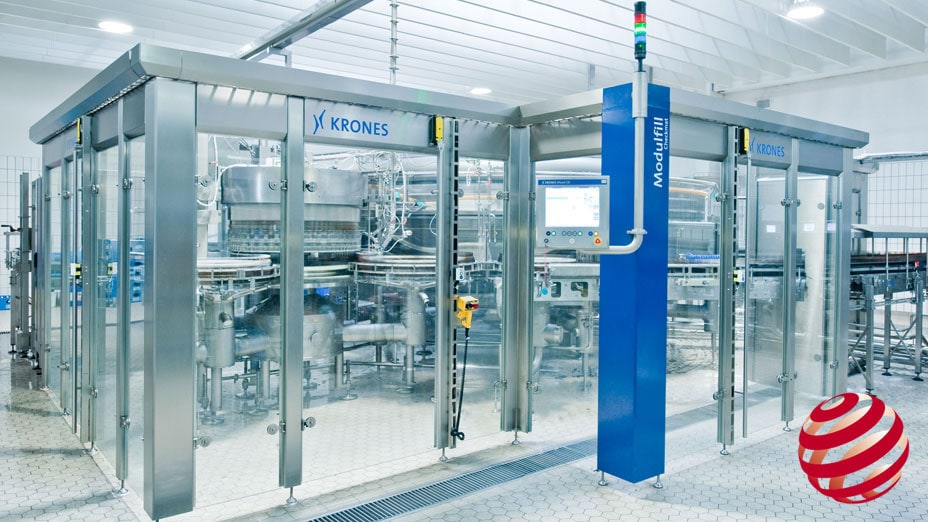
For the new, harmonised product styling over the entire range of machinery, all the way through to the operator interface, Krones received the 2006 red dot product design award, one of the world's most coveted design prizes for aesthetic appeal.
Musical instruments instead of tools
Orff's classic "Carmina Burana" bring an entirely different soundscape into the filler hall.
A new perception of acoustics is offered by a performance of Carl Orff's "Carmina Burana" in Krones' filler hall. Where otherwise machines for beverage filling are produced, the drinking ballads of the Middle Ages are sung against a modern-day backdrop.
LCS upgrades
Long useful lifetimes and high machine outputs are much appreciated in all beverage plants. Thanks to upgrades from Life-Cycle Service, older Krones machines with long years of operation behind them can be retrofitted with the very latest technology.
Greenfield breweries
Three projects with a main-contractor remit for breweries in Vietnam, producing an annual output of between 100 and 400 million litres, demonstrate the abundant confidence that brewery operators in this country (and in the rest of the world besides) place in Krones.
German facilities upgraded
In Neutraubling, the new Assembly Centre for Filling Technology - six halls with a total area of around 18,000 m2 - goes into operation. The new Labelling Centre enables client-specific tests to be run, and basic research conducted for optimum labelling processes.
16,800 feet above sea level
At 16,800 feet above sea level in the Himalayas, the water of the Tibet Glacier Mineral Water company bubbles up from the rock. At a "mere" 14,200 feet, a Krones bottling line rated at 24,000 PET bottles an hour has been installed, plus a Contiform S14 stretch blow-moulding machine.
2007
A growing market for material flow technology
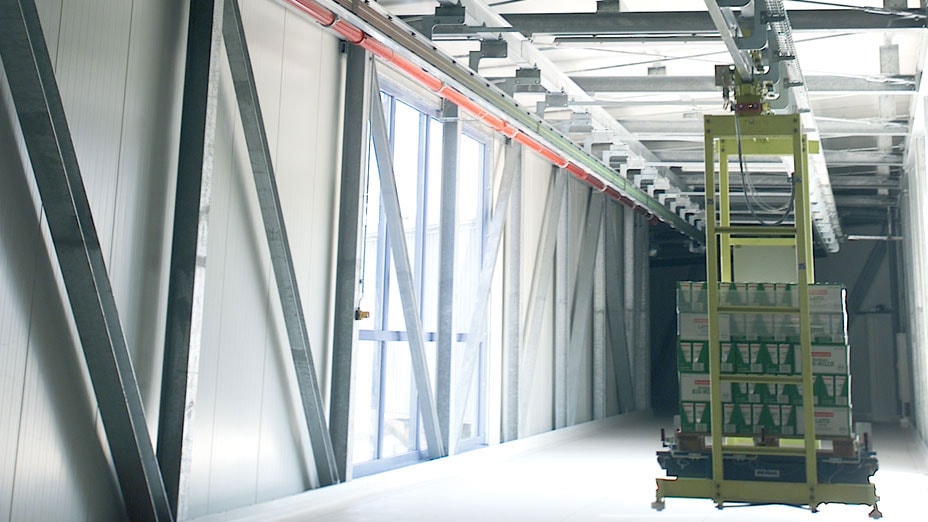
The field of intralogistics, with new warehousing and distribution centres, opens up efficiency gains for beverage plants above and beyond filling and packaging. The material flow concepts involved cover block-type and high-bay warehouses with automated storage and retrieval.
Pasteurisers with maximised efficiency
Thanks to treatment zones with a small water volume and a highly efficient heating system, the newly developed pasteuriser represents leading-edge technology in terms of resource-economy. Sturdy, long-lived conveyors ensure that the containers are dependably transported inside the pasteuriser.
Lightweights
One highlight of development work is the exceptionally light 0.5-litre PET bottle weighing just 8.8 grams. The biggest cost factor in producing PET bottles is the plastic. The bottle now developed requires up to 45 % less material than comparable containers on the market.
The Contiform success story
With its Contiform S series, Krones offers a concept that during its five years on the market has been exceptionally well received. So successfully, indeed, that in January 2007 the 500th Contiform of the S series left Krones's plant in Neutraubling.
2008
enviro
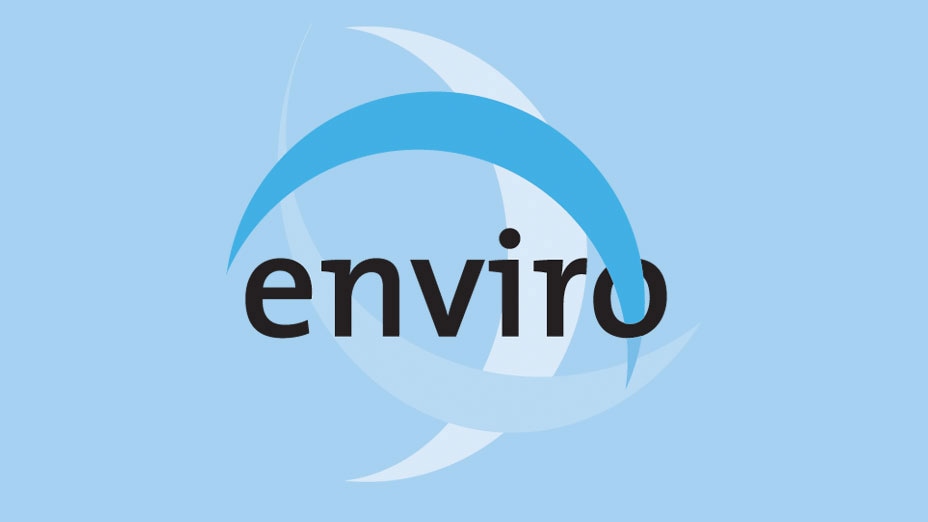
enviro stands for eco-compatible, efficient products from the Krones company. This programme, based on the idea of corporate social responsibility, aims to create an industrial standard for energy/media-economical and eco-compatible machines.
A presence in Africa
To meet the buoyant demand for beverage machinery in Africa, Krones opens an LCS Center in Johannesburg. A logistics center, service coordination for the entire continent, and spare parts management combine to ensure that the clients in Africa enjoy rapid-response service support.
Modulpal - for modularised palletising systems
With the Modulpal single-column palletising robot, Krones puts its range of palletisers on a fresh foundation. The salient features of this new family are the integrated servo-drive technology, the versatile gripper systems and the enhanced functional flexibility.
KROKI
The company's KROKI kindergarten enables staff to return very quickly to their jobs after giving birth. In this child day care centre, 42 of our staff's children are looked after in three groups by ten trained careers.
Individualised palletising patterns with Robobox
The fully automatic Robobox grouping system is a flexible functional unit for distributing non-returnable packs. Thanks to positive guidance of the packs and user-programmable layer patterns, the packs are optimally positioned prior to being palletised.
Maximised priority for sustainability
With the newly defined Corporate Guidelines, the Krones Group and its staff sign up to shared values and commit themselves to proactive and responsible sustainability. The newly formed CSR Committee monitors compliance with the CSR Guidelines.
An attractive employer
Krones is seen as an attractive and dependable employer, as evidenced by the payroll figures, rising continuously for what is meanwhile nine years. In 2008, the Executive Board and the Employees' Council welcomed the 10,000th employee.
6.6 grams
PET lite 6.6, with a material requirement of just 6.6 grams of PET for a bottle holding 500 ml of still water, constitutes a new milestone in the field of lightweight beverage containers. At the Brau Beviale trade fair, PET lite 6.6 is awarded the German Packaging Prize.
2009
Optimising maintenance work
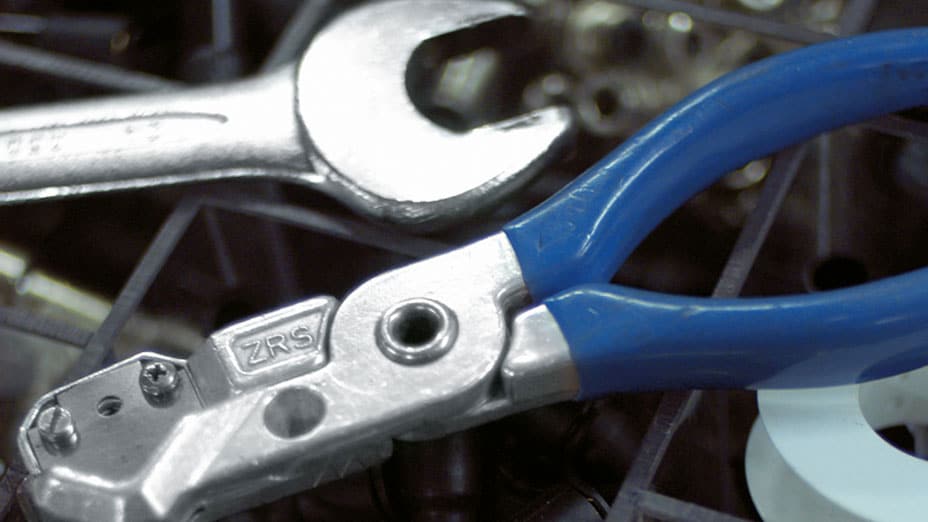
The KAM IT module manages the machines' operating data and creates maintenance plans. The work schedules for the maintenance staff are also drawn up automatically. In addition, the system monitors stock levels for spares and wear parts.
Perfect water quality
Optimum water quality is supplied by the Hydronomic water treatment system, featuring reverse-osmosis technology. The system has been certified under the enviro label, and consumes comparatively small amounts of energy, with economical use of rinsing water and cleaning chemicals.
ErgoBloc L and ErgoBloc D
Innovative monobloc concepts: the ErgoBloc L is a wet-end monobloc for producing, labelling and filling PET containers. In the dry end, the ErgoBloc D combines the Variopac Pro packer and the Modulpal palletising system with the Robobox grouping station.
A streamlined packaging system
The Varioline packaging system is designed for multi-stage processes like grouping loose containers into packs and then forming multipacks from them. This flexible system is able to create many different end-of-the-line packaging variants.
CombiCube B
The salient features of the compactly dimensioned CombiCube B brewhouse include a modestly sized frame construction, and standardised vessels for the mashing, lautering and wort boiling processes. The target group for this new development in brewhouse technology is breweries with an annual production output of up to 150,000 hl.
2010
A presence in the social media
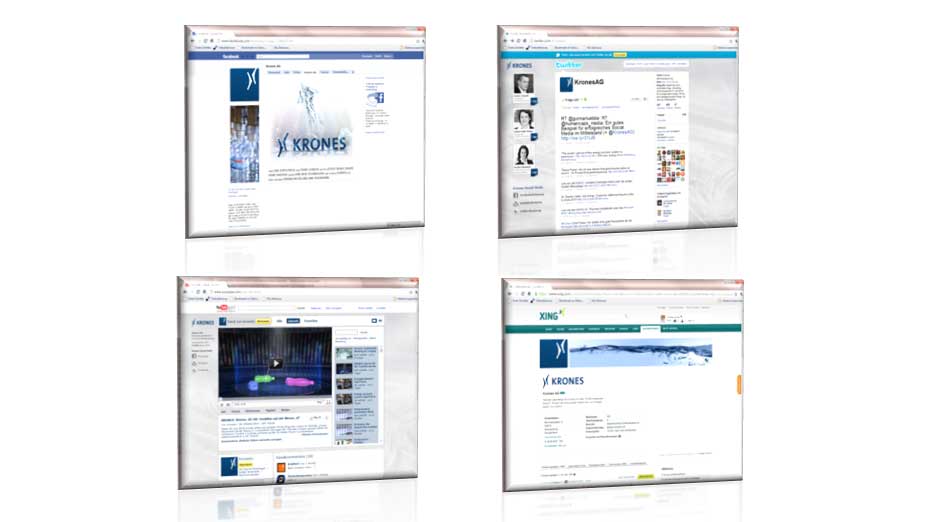
Krones is one of the first machinery manufacturers to set up its own pages on Facebook, Twitter and YouTube, so as to post texts, photos and films on the net. Target groups evolve into dialogue partners here, proactively participating in the communication.
Cross-facility production control
Trackable production statistics are of enormous importance for high line availability. Breweries with more than one production facility can perform cross-facility production planning with the aid of the higher-order Management Execution System (MES).
Maximised quality in all manufacturing steps
In the new pipe machining centre, a hundred employees machine more than 3,000 metres of stainless steel piping each week on an area of 5,300 square metres. Worksteps that used to be scattered over several different halls or even outsourced are now centralised, with concomitant savings in production costs and manufacturing times.
EvoGuard
In the shape of EvoGuard, as of now a high-performance series of valves "made by Krones" is available for the food and beverage industries. New details in terms of seal design and valve housing construction ensure that this series meets with keen interest.
EquiTherm - for energy-efficient brewing
EquiTherm removes energy from the wort after boiling, which is then used in the mashing process. The first user of EquiTherm, the Bergquell Brewery in Löbau, is now getting more than 30 % savings in terms of primary energy.
Buildings geared to sustainability
The new photovoltaic system produces approximately 148,000 kilowatt-hours of electricity, most of it utilised in the plant's own network. The building's cooling concept is equally innovative: groundwater is fed into the heating loops of the underfloor heating system.
60 packets of sugar form one layer
The Melnik Packaging Centre of TTD AG in Dobrovice, Czechia, handles approximately 100,000 tons of sugar a year. A Krones palletising system featuring a Robobox and a Modulpal performs layer grouping and palletising at a speed of 250 1-kg packets a minute.
2011 – now
2011
Strapping suffices
LitePac is a packaging concept for PET bottles featuring a horizontal strap and a vertical piece of strapping as a handle. This new form of packaging does without film-wrapping entirely, and in comparison to shrink-packs saves more than 65 % in terms of packaging costs.
All options for labelling
More and more individuality is being demanded in the labelling process. The DecoBloc is a combination of a modularised labeller interfaced with the requisite stations and a sleeve labeller. In rapidly changing markets, the DecoBloc meets all the relevant requirements.
2012
Juice with fruit chunks
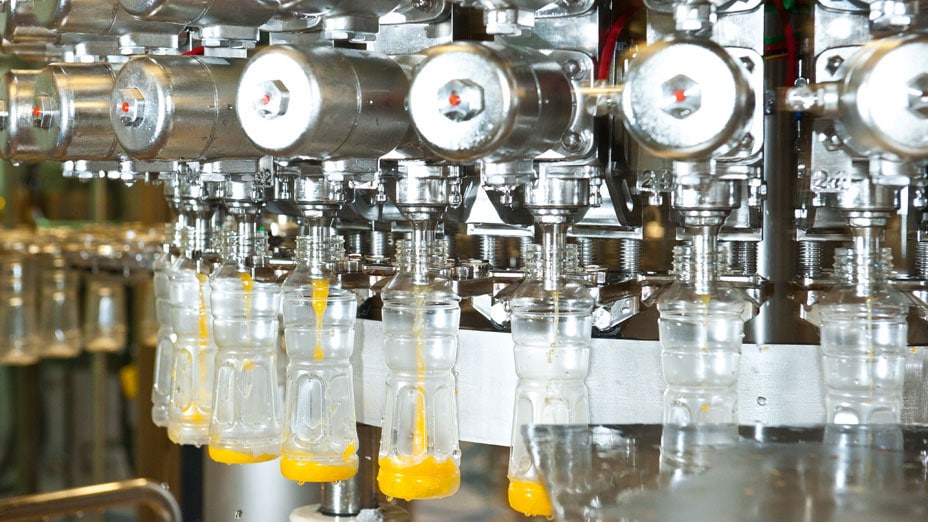
For the rapidly growing segment of juice beverages with fruit chunks, Krones offers the twin-flow process. Juice and fruit chunks are heated up and filled separately. The FlexiFruit dosing system ensures a precise proportion of fruit particles in the bottle.
A pilot for production
SitePilot is Krones' modularised software package for integrated production and logistics. It renders processes plannable and transparent, it documents and controls them. The individual modules inform the management and staff about all production and logistical processes.
New training centre inaugurated
With the new training centre, Krones possesses around 1,400 square metres of space for its instructional courses. In 2011, Krones trained a total of 432 young people in technical and industrial careers, and continues to prioritise appropriately qualified recruits from its own training programme.
Commitment to business ethics
In order to communicate questions of business ethics more effectively, Krones signs up to the United Nations (UN) Global Compact. Its guidelines apply worldwide for the fields of human rights, labour standards, environmental protection and combating corruption, and are binding on the companies involved.
2013
TÜV certification for Krones Brazil
The internationally recognised certificate for an integrated management system (IMS) covers quality, environmental protection and occupational safety.
Production of plastic containers in a cleanroom
In the Contiform AseptBloc, it’s the preforms that are already decontaminated, not the finished plastic containers. The monobloc thus ensures a sterile process chain from stretch blow-moulding to capping the aseptically filled bottles.
2014
Autonomous firm for valve technology operations

Evoguard GmbH handles all operations involving the development and marketing of its own series of valves and pumps. This wholly-owned Krones subsidiary now occupies a newly erected production building in Nittenau.
Krones as an employer
The news magazine “Focus” graded employers in conjunction with leading career networks in the German-speaking nations. In the “Machinery and Plant Construction, Multitechnologies” rankings, Krones came 18th nationwide, and 4th in Bavaria.
IMS certificate for Krones Machinery, Taicang/China
With the Integrated Management System (IMS), Krones has embraced the quality and HSE standards laid down in DIN EN ISO 9001, DIN EN ISO 14001, BS OHSAS 18001, and is now using these at its production facility in China as well.
Murau Brewery geared entirely to regenerative energy
In its brewing process, the Murau Brewery in Austria uses only CO2-neutral thermal energy that’s been regeneratively produced, an advance made possible by the EquiTherm system, which takes the entire energy required for mashing from the wort cooling process.
Syskron Holding set up for intralogistical projects
Syskron Holding develops products and services for the field of intralogistics, with which companies from the beverage filling and packaging sector can cost-efficiently handle their entire intra-plant goods flows.
Awards for Krones PET lite 9.9 carbonated
This bottle for carbonated beverages weighs a mere 9.9 grams and holds 500 millilitres. Krones’ designers have already won several awards. The main focus of their development work is on creating containers that are both marketable and eco-friendly.
Innovative container decoration with direct printing
DecoType prints on empty plastic containers: UV inks can create print height of up to 200 mm. This also covers container surfaces that traditional labelling cannot reach. The system won the 2014 Beverage Innovation Award 2014 in the "Best Technology Innovation" category.
2015
Krones: the right choice for craft brewers
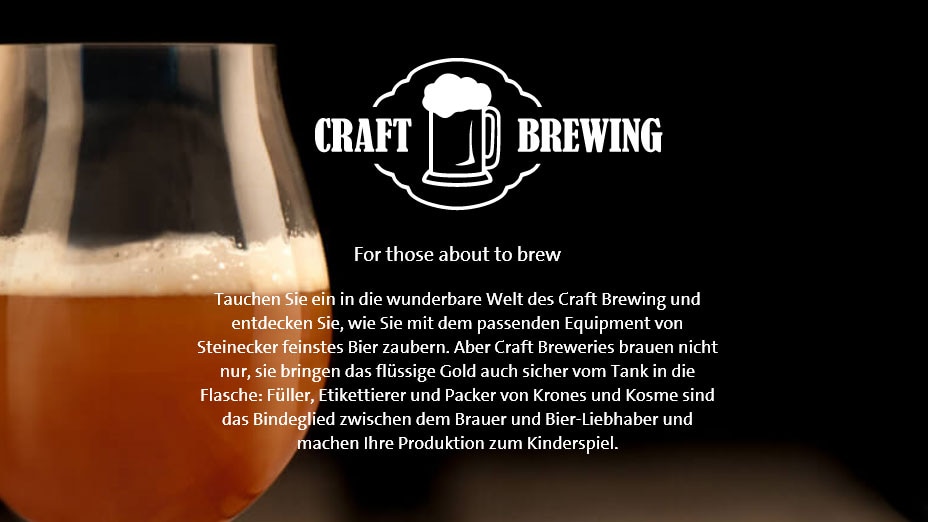
The compactly dimensioned MicroCube brewing system has been designed to produce brews of up to ten hectolitres in size. MicroCube consists of a brewhouse, a fermentation cellar, plus water, heat and refrigeration utilities. Krones has also developed the Craftmate, a can filler designed specifically for this customer grouping.
New training centre in Colombia
Training in South America in the staff’s native language: the operating and maintenance personnel thus acquire the skills they need for efficient line operation at beverage producers. Thus Krones Andina Ltda. makes a significant contribution towards advanced training of technical personnel in this region.
Krones acquires Gernep
With Gernep’s portfolio of labellers in the lower and medium output range, and the coverage of markets outside the beverage industry, Krones is expanding its own action capabilities in the Labelling Technology Division.
Prizes for innovative solutions
The Foodtec Award in Gold of the German Agricultural Society (DLG) for the VarioSpin product deaerator and the Oscar dell'Imballagio 2015 awarded by the Italian Packaging Institute for the DecoType container decoration machine triumphantly demonstrate: Krones’ innovative vigour earns repeated accolades from the sector.
Schaefer Förderanlagen- und Maschinenbau GmbH taken over
In the field of packaging technology, the takeover of Schaefer Förderanlagen- und Maschinenbau GmbH, Unterföhring, provides meaningful capability enhancement. Krones thus incorporates engineering and service support expertise for palletising solutions and Schaefer’s portfolio of patents.
SAP solutions for production logistics and intralogistics
With the acquisition of Triacos GmbH, Syskron Holding GmbH is widening its portfolio. Besides its own software products, the company is now also providing SAP standard solutions for the beverage industry, focusing primarily on production logistics and intralogistics.
2016
Volker Kronseder new Chairman of the Supervisory Board
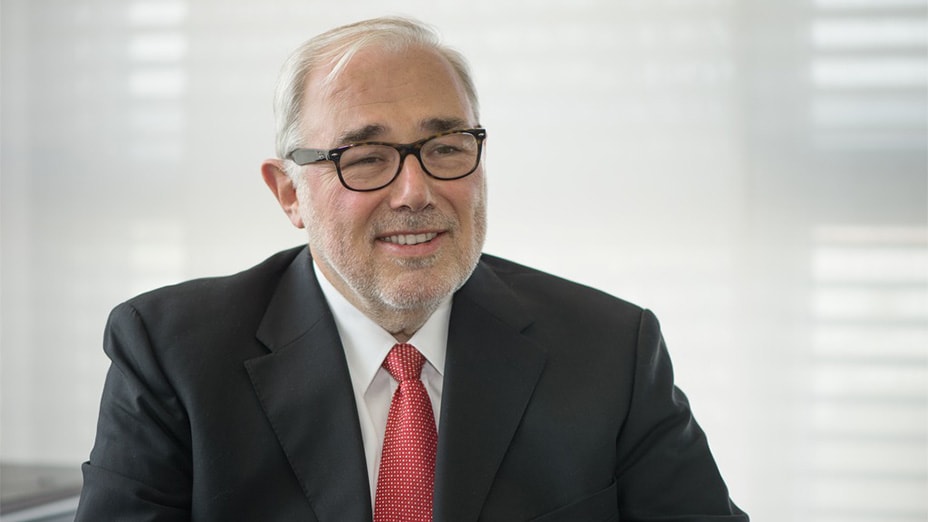
The Chairman of the Executive Board relinquishes operational responsibility at the end of 2015 and moves to the Supervisory Board in 2016.
After about 20 years as Chairman of the Board, Volker Kronseder reaches the age limit for Board members and leaves the Board. The 2016 Annual General Meeting elects him as the new Chairman of the Supervisory Board.
Expanded intralogistics offering
Krones acquires a majority stake in the Italian intralogistics and material flow expert System Logistics S.p.A..
System Logistics S.p.A. strengthens the Krones Group in intralogistics, material flow technology and warehousing. This covers the entire value chain in the beverage and food sector and expands the "one-stop shop" concept.
Bundled offer for the dairy industry
Milkron GmbH is a specialist in the dairy industry and thus expands its activities in process technology.
With the founding of Milkron GmbH, Krones is targeting processors of milk and dairy products. The subsidiary is the point of contact for complete dairies or even line adaptations and additions.
Share2Act: Knowledge transfer in production
Efficient production processes are everything: Share2Act provides all data in real time for a quick machine overview.
The developers at Syskron describe their new app as a kind of social network for the interaction of people and machines: each machine receives its own profile page with extensive information and data.
2017
Five seconds
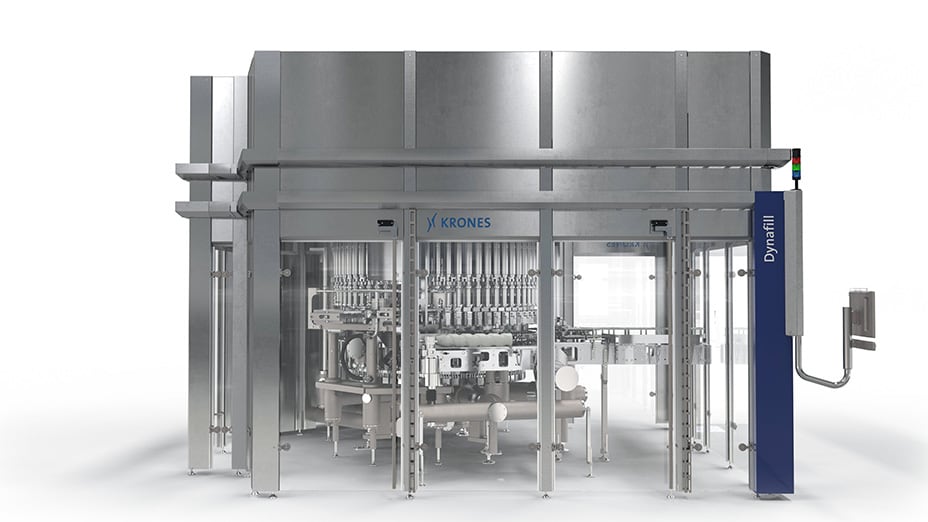
The innovative Dynafill filling system halves the time needed for filling and capping in beer bottling.
Filling and capping are done by a single functional unit in the Dynafill: good for beer quality, as the process takes place in a closed, low-oxygen atmosphere. The complete filling and capping process takes only five seconds.
Block solution - now also for cans
All-in-one: the Modulfill Bloc FS-C combines filler and seamer for can filling - completely from Krones.
In this harmonious system, filler and seamer play together perfectly. The Modulseam can seamer is the match winner here, because the new seamer from our own development makes the block solution possible in the first place.
The energy self-sufficient brewery wins
The "Brewery of the Future" concept wins the audience award of the Energy Efficiency Award 2017.
The winning figures of the efficient brewery with a production volume of 2.6 million hectolitres of beer: the concept saves 30 per cent electrical energy and around 60 per cent thermal energy compared to a standard brewery.
2018
One of the industry leaders in sustainability
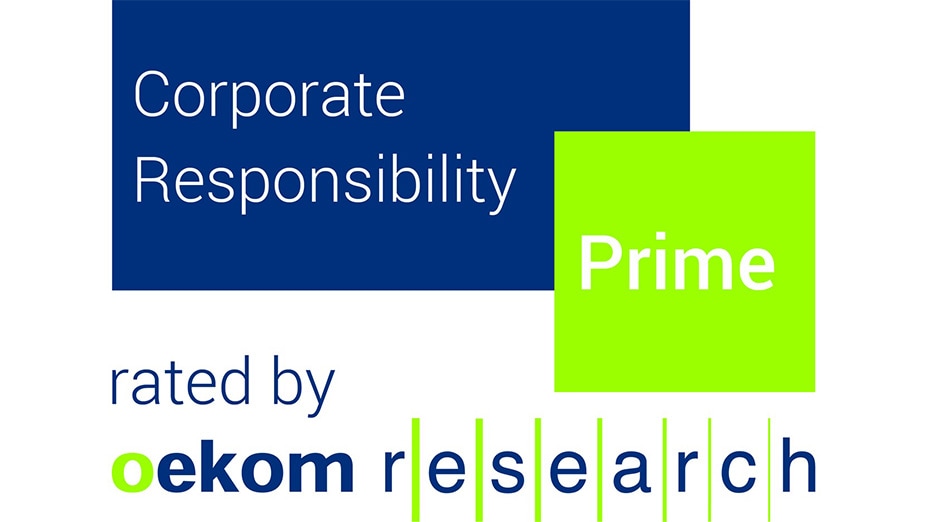
′B-′ Prime: Oekom-Research awards Krones AG a top score for its sustainability performance for the fourth time in a row.
Over 100 categories are examined. At Krones, a balanced work-life balance in the employees category and the economical use of media and energy in the eco-efficiency category are highlighted in particular.
New subsidiary for direct printing
Digital decoration technology for primary packaging is the speciality of the new subsidiary Dekron.
Following complete integration into the Krones Group, Till GmbH is renamed Dekron GmbH. The activities for printing beverage containers are bundled in the new subsidiary, and the DecoType series is being further developed.
Steinecker Brew Center opens
The world's most modern research brewery is now located at Krones' Steinecker plant.
The new brewing pilot plant - a five-hectolitre brewhouse with five vessels - is designed for all common international brewing processes. The flexible facility allows customers to test new process engineering solutions - including state-of-the-art IT technology.
Even more PET skills
With the acquisition of MHT Holding AG, Krones is supplementing its range of products for PET bottlers.
Moulds for the production of preforms for PET bottles are now also available in the group. With the know-how on injection moulds, customers can make their preform production even more efficient and material-saving.
Major project in PET recycling
The US company rPlanet Earth produces 36,000 tonnes of recyclate with Krones MetaPure.
The Californian PET recycler uses MetaPure to wash and decontaminate flakes from used PET bottles. The food-grade recyclate produced can be used for new preforms, containers or extruded films.
2019
New plant in Hungary goes into operation
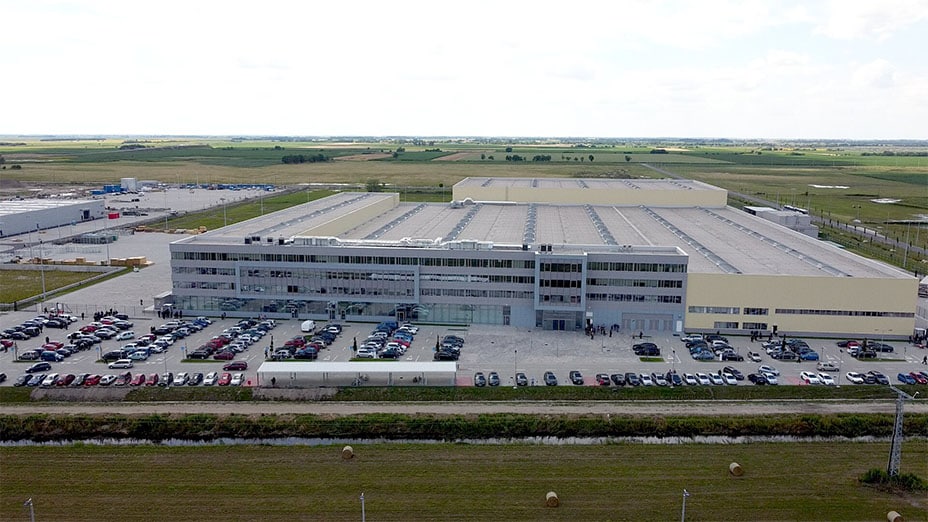
At the Debrecen facility, Krones starts operating a state-of-the-art production plant covering 150,000 square metres.
500 employees work at the new plant in Debrecen. They manufacture machine components - such as bottle cells or drip plates - and assemble plant components.
New filling technology in the compact class
Craftmate G is the new glass bottle filling system for small and medium-sized breweries.
The Craftmate G filler for glass bottles with an output of 24,000 containers per hour is perfect for users in the low output range. For can filling, the Craftmate C has already been proving its worth since 2015.
SMETA social audit passed again
Labour standards, health and safety, corporate integrity and environmental management are the audit categories of the social audit.
Social standards are often decisive when awarding contracts - especially for multinational manufacturers. In the audit conducted by the non-profit organisation SEDEX, the independent auditors confirm Krones' high standard of working conditions.
New centre for control cabinet production
The new control cabinet production at the Neutraubling headquarters offers shorter throughput times and higher productivity.
In the new building with 6,000 square metres of production space and 850 square metres of office space, automatic driverless transport vehicles and improved material flows ensure maximum efficiency.
Argos - Smart Glasses for real-time service
Put on the headset with smart glasses and off you go: Fast error analysis in real time.
Troubleshooting on the machine - made easy. With Argos, direct insight into the machine is possible during remote support. The Krones service employee can communicate with the line operator using augmented reality.
New building of the Krones Academy opened
1,500 square metres of hall space and 16 training rooms - that's what the new academy building at the group headquarters in Neutraubling offers.
Customers receive practical training on new technologies or older machine generations in order to achieve the highest possible performance. Train-the-trainer courses for the worldwide service centres are also being expanded.
2020
Focus on sustainable packaging concepts
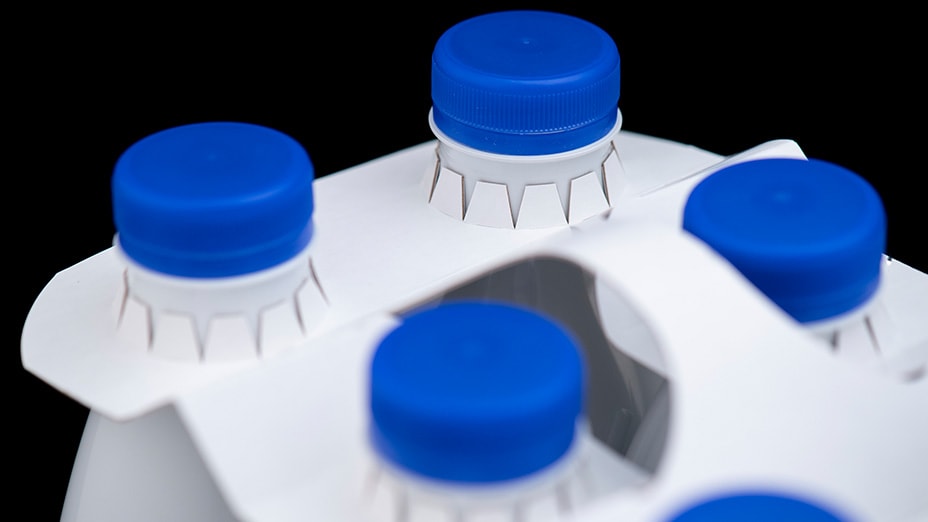
Reduce and recycle are the recipes for resource conservation - also in beverage packaging.
LitePac Top is a cardboard clip for disposable PET containers or cans. With the cardboard clip, the containers become stable packs - without film wrapping as with shrink packs. The consumer can conveniently dispose of the cardboard clip with the waste paper.
Waste water recycling as a system solution
Beverage production requires up to 80 per cent less water with Krones' closed-loop concept.
Thanks to the new HydroCircle system, the entire process water can be treated and water consumption can be significantly reduced. The system can also be retrofitted to existing plants.
Climate strategy: Ambitious goals adopted
Krones plans to reduce its greenhouse gas emissions by up to 80 per cent at all its locations worldwide by 2030.
The independent Science Based Targets Initiative (SBTi) confirms: Krones' climate targets contribute to limiting global warming caused by the greenhouse effect to 1.5 degrees Celsius.
Gold in sustainability
The international platform for CSR performance EcoVadis awards Krones the gold medal.
With the new climate strategy and an even stronger focus on the topic of human rights, Krones once again achieves a high rating after 2019. For clients, this means: Krones offers them the best performance in terms of sustainability.
Deep Learning for improved inspection results
High-precision error detection with deep-learning software prevents the incorrect rejection of perfect bottles.
The Linatronic AI trains with sample images. With the help of artificial neural networks, the highest hit accuracy is achieved in bottle analysis. Even water drops are now detected with a reliability of 99.9 percent.
Powerful water treatment plant
Superlative: The new plant at Makkah Water in Saudi Arabia is around three times larger than conventional plants.
For the plant modernisation in Jeddah, Krones is supplying high-speed filling technology and a Hydronomic water treatment system. It produces up to 3 x 110 cubic metres of water per hour and is one of the largest lines Krones has ever built.
CO2 -neutral filling plant for smoothies
A completely new factory for the production and bottling of smoothies is being built at the port of Rotterdam.
Smoothie and juice producer innocent commissions a CO2 -neutral bottling plant that also minimises water use. Four identical PET lines are to produce around 400 million chilled drinks a year.
2021
Investing in the future
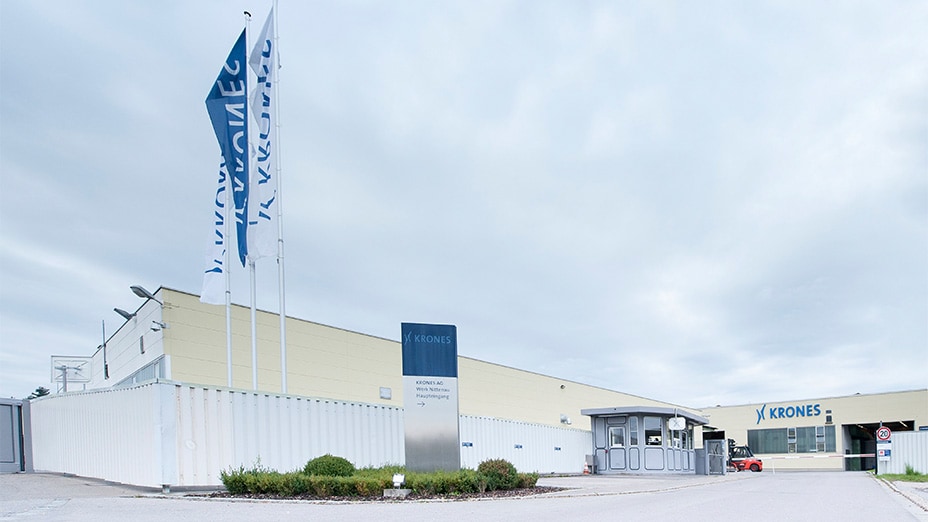
With an extensive investment programme totalling 20 million euros, Krones AG is clearly committed to its production facility in Nittenau. The first step was to order a new laser welding system for large parts. This was followed in 2021 by a 32-metre-long and 14-metre-wide large-scale machining line for turning and milling.
Climate-conscious corporate success
In an independent survey, Statista, one of the leading providers of market and consumer data, together with the business magazine Capital, examined the relationship between sales growth and the reduction of CO2 emissions at German companies. The result was Germany's top 100 climate-conscious companies. Krones AG achieved 48th place in the ranking.
Stories from the Krones world online in future
After more than 33 years, an era is coming to an end - and a new one is beginning. The printed Krones magazine is being replaced by an online platform.
Instead of being sent by post, the latest stories from the Krones world will in future be available quickly and easily with just one click.
As in the printed edition, the online platform will also feature exciting stories on client projects, as well as new technologies and solutions from the Krones Group. But that's not all! Krones magazine now also offers a look behind the scenes at Krones.
Large in action
In 2018, the Contiform 3 Speed set an industry speed record with an output of 2,750 containers per cavity per hour. Less than three years later, the 100th high-performance blow-moulding machine was sold.
Mechanical engineering and digitalization are moving closer together
In keeping with its role as a system supplier, Krones is bringing the fields of mechanical engineering and digitalization even closer together. Starting now, everything will take place within the Krones Ecosystem, which will stretch over all the Group’s new machines like an invisible dome and interlink them at the data level. The resulting line and production data will provide the basis for using existing cloud services and other digital solutions that Krones will be offering in future.
The Krones Ecosystem is the first building block of the new portal Krones.world, which will provide clients with central access to digital Krones solutions in future.
2022
Upcycling brewing residues to CO₂ neutrality
One of the last Brewnomic building blocks is being implemented at the Ustersbach brewery: As part of a Steinecker development project, a holistic solution for the material upcycling and energy recovery of brewing residues is being investigated and optimised on a pilot plant.
Among other things, brewer's grains can be used to produce protein, which is currently in high demand in the beverage and food industry, but also by producers of food supplements or cosmetics.
After separating the valuable ingredients, the remaining biomass can be converted much more easily in a biogas plant.
Krones showroom - an excellent solution
Stroll through a beverage line, view machine details in three-dimensional space and discuss the layout of an entire line from different perspectives: since 2020, the Krones showroom has offered a genuine virtual experience - right from your own desk.
Not only those who already use and experience the showroom live are enthusiastic - the jury of the German Brand Awards also liked the concept and implementation so much that they awarded the Krones Showroom the German Brand Award 2022 as "Winner" in the category "Excellence in Brand Strategy and Creation - Brand Communication - Point of Sale".
Krones – New target picture
We do more." becomes "Solutions beyond tomorrow" - in mid-2022, Krones not only gives itself a new claim, but also formulates a new vision.
In it, Krones shows its vision and the way in which these ambitious goals can be fulfilled. The result is solutions for customers, humanity and the planet that respond to the three challenges facing humanity.
The biggest driver of innovation in this context is sustainability, which now occupies a major place among clients' operations. Krones will consistently apply this sustainability standard to its entire portfolio in the fields of process technology, filling and packaging technology, and intralogistics. In this context, digitalization and fully comprehensive services play a decisive role in the production processes of our clients, both to increase performance and to reduce resource consumption.
Quantum leap in block technology
Krones has set a new milestone in monobloc technology with the world's first wet-end monobloc capable of producing 100,000 0.5-litre water bottles per hour. The filler posed the biggest challenge during development. For there are physical limits to the standard approach of "a bigger carousel equals more output". This is why the monobloc was equipped with two modular filling and capping units.
A success story goes into the next round
Since its introduction 25 years ago, the Contiform stretch blow-moulding machine has been continuously developed. In addition to further generations, the product range has also been expanded: in 2015, the Contiform 3 Pro came onto the market, in 2019 the Contiform 3 Speed or in 2021 the Contiform 3 Big Bottle. One thing remained the same with all developments: the Contiform always sets new standards.
The fourth generation of the success story has been ready since 2022. With the new Contiform, too, environmentally friendly, sustainable and at the same time economical operation is the top priority: this was one of the most important goals in the further development of the Contiform.
Precise, fast and fully automatic
Ambient temperature or humidity, preform weight or recycled material content: if such frame parameters change, for example, the stretch blow-moulding process always has to be readjusted or even reset. But instead of being done manually by the operating personnel, this task is now performed by the intelligent Contiloop AI control system - precisely, quickly and fully automatically thanks to artificial intelligence.