Almacén autoportante de estantes elevados de System Logistics
A pesar de la larga y estrecha relación entre ambas empresas: al comienzo no se podía dar por descontado la adjudicación de la construcción del nuevo almacén autoportante de estantes elevados a Krones, al contrario. «Iniciamos el proceso de adjudicación muy abiertamente», comenta Hächl. «Pensamos para nosotros: la tecnología de transporte y almacenamiento no es tan complicada como la tecnología de envasado y embalado, por lo tanto también hay otros proveedores capaces de hacerlo bien». La System Logistics GmbH que al momento de la licitación era aún la división de intralogística de Syskron GmbH, era para Adelholzener un posible proveedor entre muchos. Después de varias rondas y planeaciones detalladas, la filial de Krones se impuso ante los demás competidores.
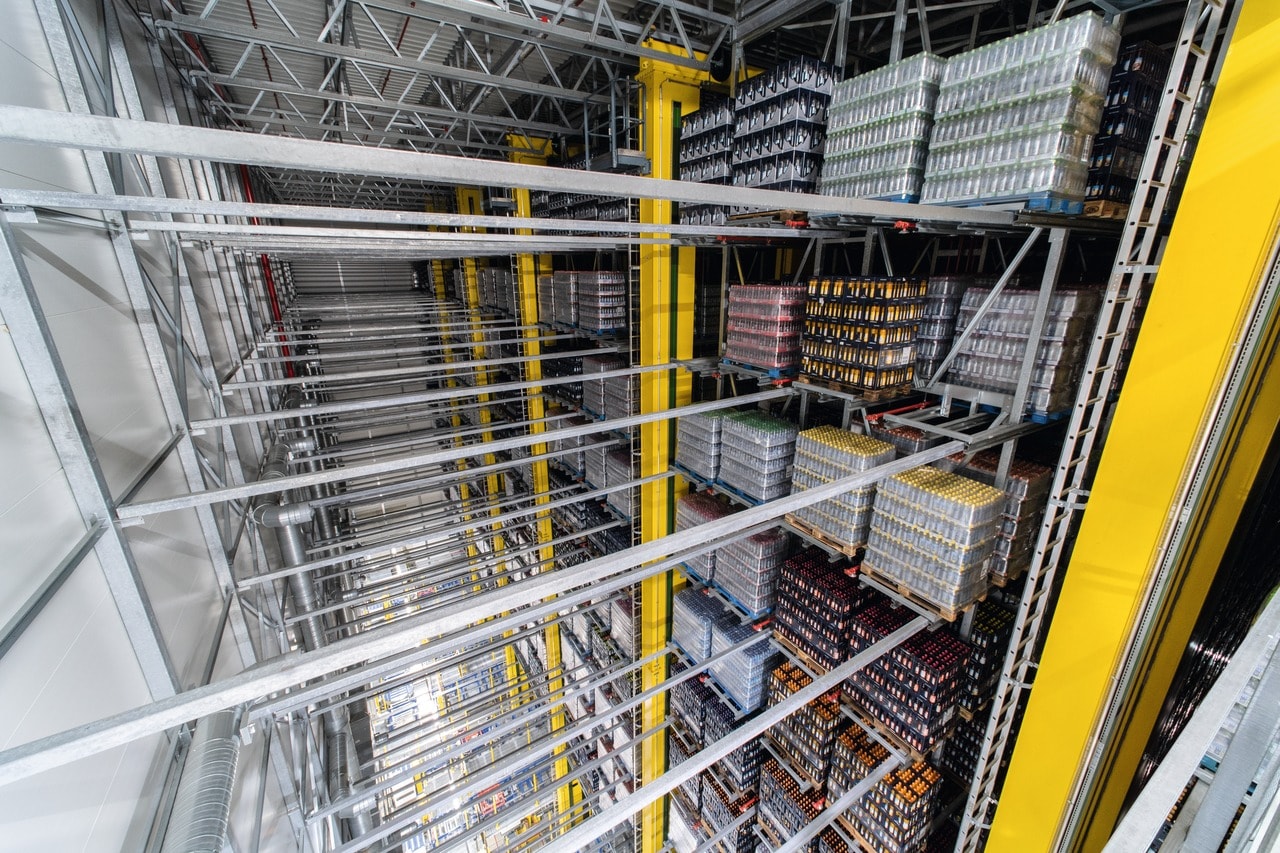