It is a place of contrasts: viewed from outside, the Adelholzener plant blends almost inconspicuously into the surrounding landscape. Against the imposing backdrop of the Bavarian Alps, its white-grey buildings seem like brightly polished, carefully positioned toy blocks. But as you take your first step into the bottling hall, this impression is abruptly changed: an intricate network of stainless steel extends over two levels. You can only guess where the beginning and end of the convoluted line construction might be. The path between the machines includes numerous flights of steps, crossovers and platforms. Quite obviously, all of this follows a sophisticated logic, well thought-out down to the tiniest detail. Any outsider trying to understand it will feel helplessly out of his depth – both at first and second glance. “Only he who knows his tracks knows where he comes from”: this sentence taken from Adelholzener’s current advertising spot can in this context also be applied quite literally.
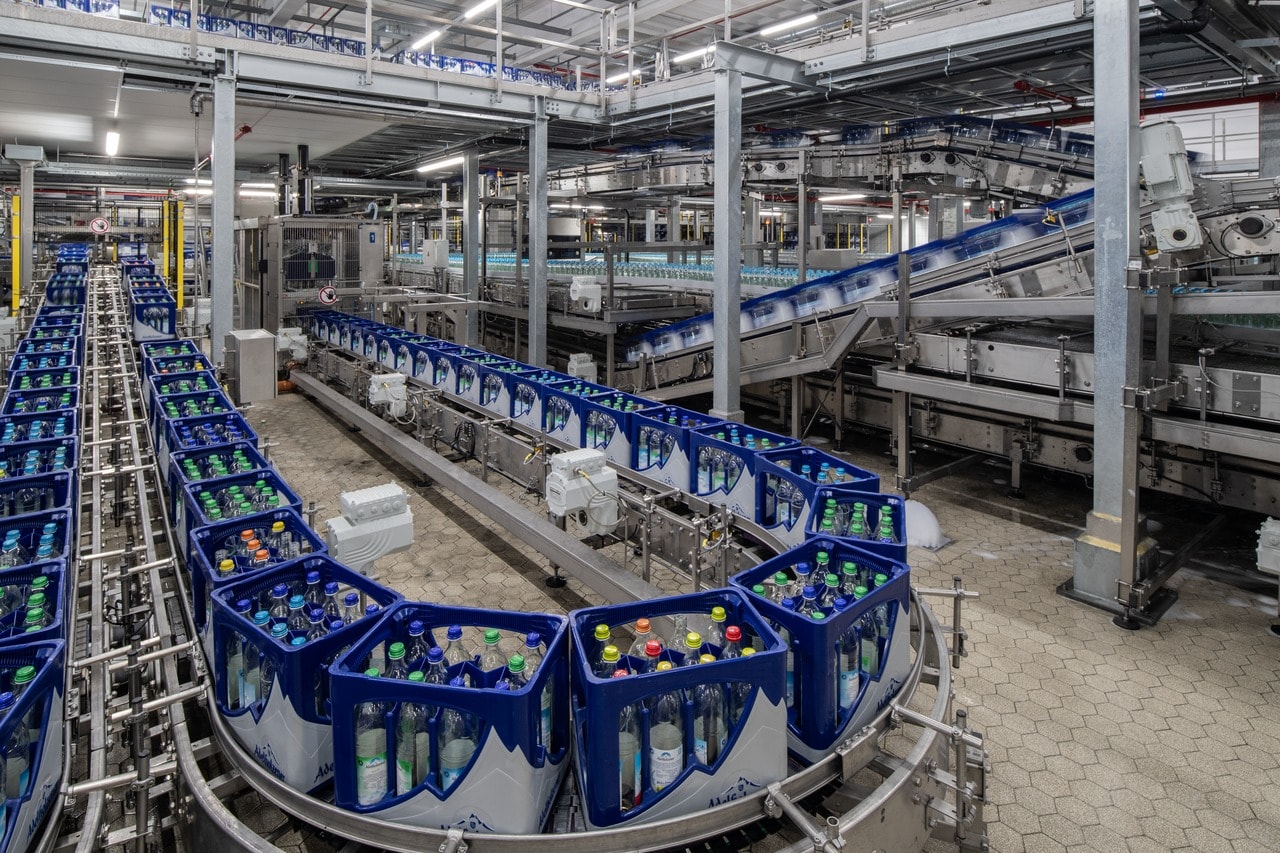