Injection moulding systems for preforms and caps
Most bottlers and beverage manufacturers purchase their preforms and caps. Why is that?
In-house production offers you all sorts of benefits, mainly:
- Greater independence from external influences
- Individual design flexibility in line with your requirements
- Total control over production processes and their results
- Security and flexibility for the future
It is easy to become your own supplier
You can obtain the right injection moulding machine for PET preforms with Prefero by Krones, for caps from our group subsidiary Netstal, including know-how on how to operate these systems ideally and much more. This includes everything from the preform and cap design all the way to the overhaul or replacement of older systems: You can always count on the individual support of our injection moulding professionals.
The spectrum and services comprises, among other things:
- Individual preform and cap design
- Development of a tailor-made production concept
- TCO and sustainability analyses
- Planning, configuration and integration of product technology
- System installation and commissioning
- Comprehensive training measures for your production team
- Maintenance and support for the entire system life cycle
- Upgrades and overhauls for a long service life
- Expansion or replacement of existing systems
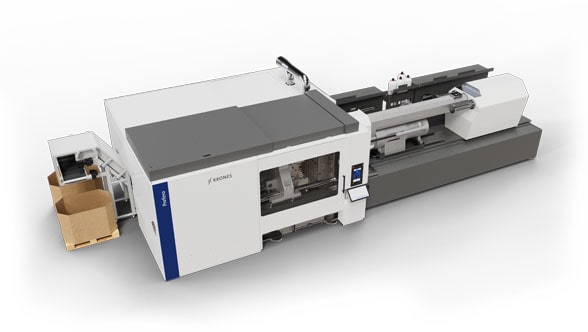
The line concept enhanced to include injection moulding.
The Krones preform system provides you with reliable technology producing at maximum speed and utmost precision. The Krones Prefero injection moulding machine constitutes the core of the line. Among other things, it impresses with a lock-to-lock time of 1.9 seconds (400 t) and short cycle times. And the best thing is: Thanks to a recovery system, the energy consumption is reduced by up to 20 percent as compared to other, comparable, machines of the competition.
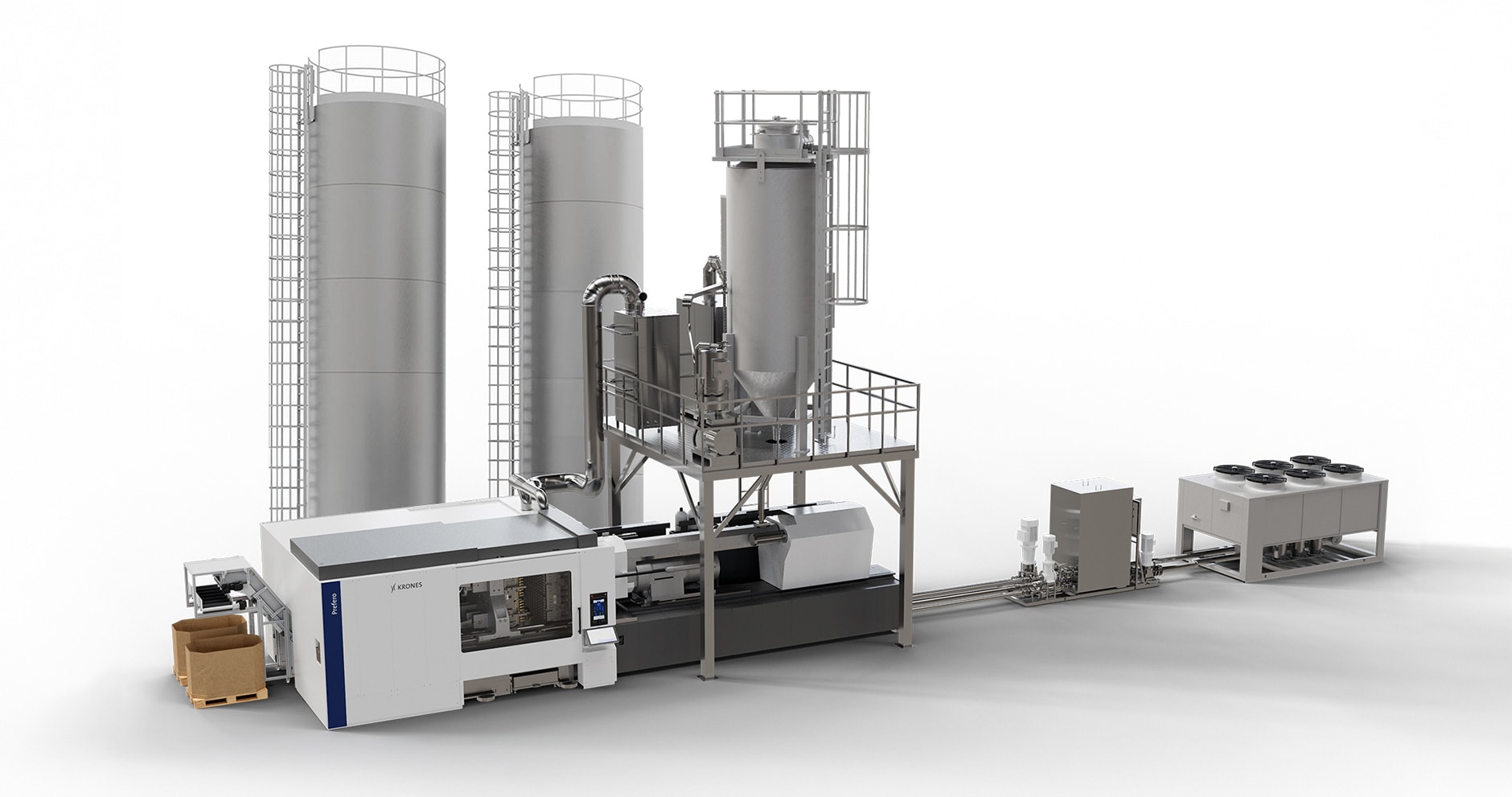
Injection moulding machine “IMM”
- E-clamp with recuperation
- Smart operation
- Sutiable for 100 percent rPET
Dryer concept/platform
- Silo on top and booster options
- Customized platforms
- Suitable for 100 percent rPET
Chiller system and T/P
- Air-, dry-, or water condensed
- Tank/Pump unit on a skid
- Piping and insulation
Dehumidifier
- Dry air with dew point control
- Additional option for cool air
Mould and robot
- EOT with inner cooling
- Optimized hotrunner for rPET
Conveyor
- Box loading
- Inline and offline inspection systems
- Various preform handling systems
Material handling
- Silos and big-bag unloading stations
- Distribution and conveying
- Dedusting and mixing
Additive device
- Masterbatch or liquid
- Volumetric and gravimetric solution
Krones' subsidiary Netstal can supply you with the appropriate injection moulding machine for manufacturing closures – whether for beverage bottles or applications in the food or non-food sectors.
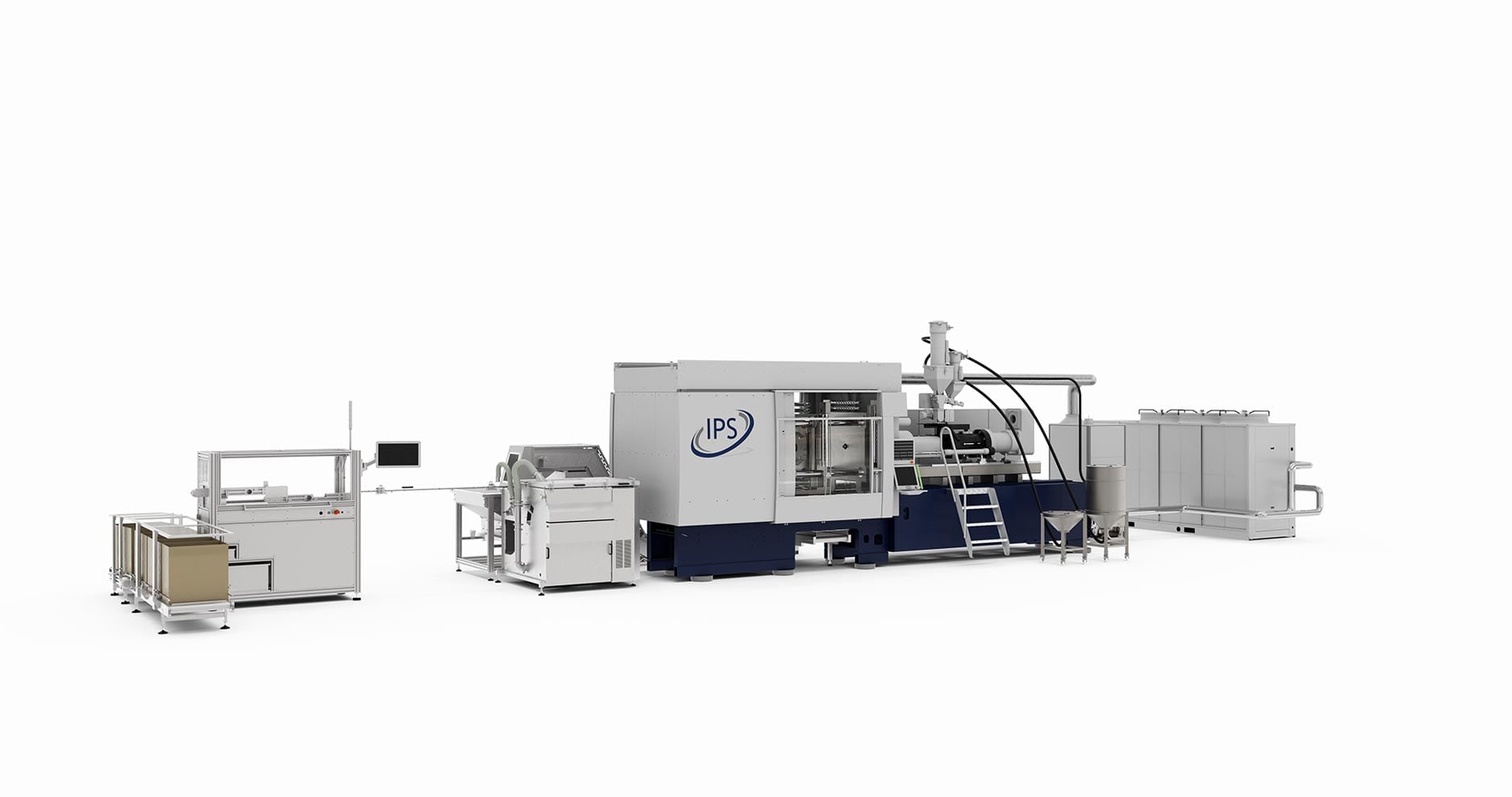
Inline inspection system
- 100 percent inspection: inside and outside
- Pinhole and cavity reading
- Up to 3.600 caps per minute
Cap conveyor and sorting system
- Cap cooler
- Bad part chute
- CAP orientation with bunker
Injection moulding machine “IMM”
- E-clamp with recuperation
- Smart operation
- Integrated downstream
Closure mould
- Up to 128 cavity
- Integrated hotrunner (in IMM)
- Optimized gate area
Dehumidifier
- Dry air with dew point control
- Additional option for cool air
Material handling/Additive
- Loading station with bins
- Master batches and additive
- Volumetric and gravimetric options
Chiller system
- Air-, dry-, or water condensed
- Piping and insulation
Injection moulding tools for each system type
They are at the heart of every preform production process: injection moulding tools have a considerable impact on the process quality, output and sustainability of your line. To ensure that you can get the maximum benefit despite all these factors, the tools are designed and manufactured to suit your individual needs. Krones subsidiary, MHT Mold & Hotrunner Technology AG, has specialised in precisely this. As an independent supplier, it equips all the familiar machine systems with custom-fit tools.
With their up to 192 cavities, MHT tools are dedicated to working at high speed. They also provide each individual preform with an entire list of benefits, including:
- No crystallinity or scratches
- High surface quality
- Low acetaldehyde level
- Seamless mould partitions
- Minimum eccentricity
- High stability
- Consistent weight
PET tools for perfect preform quality
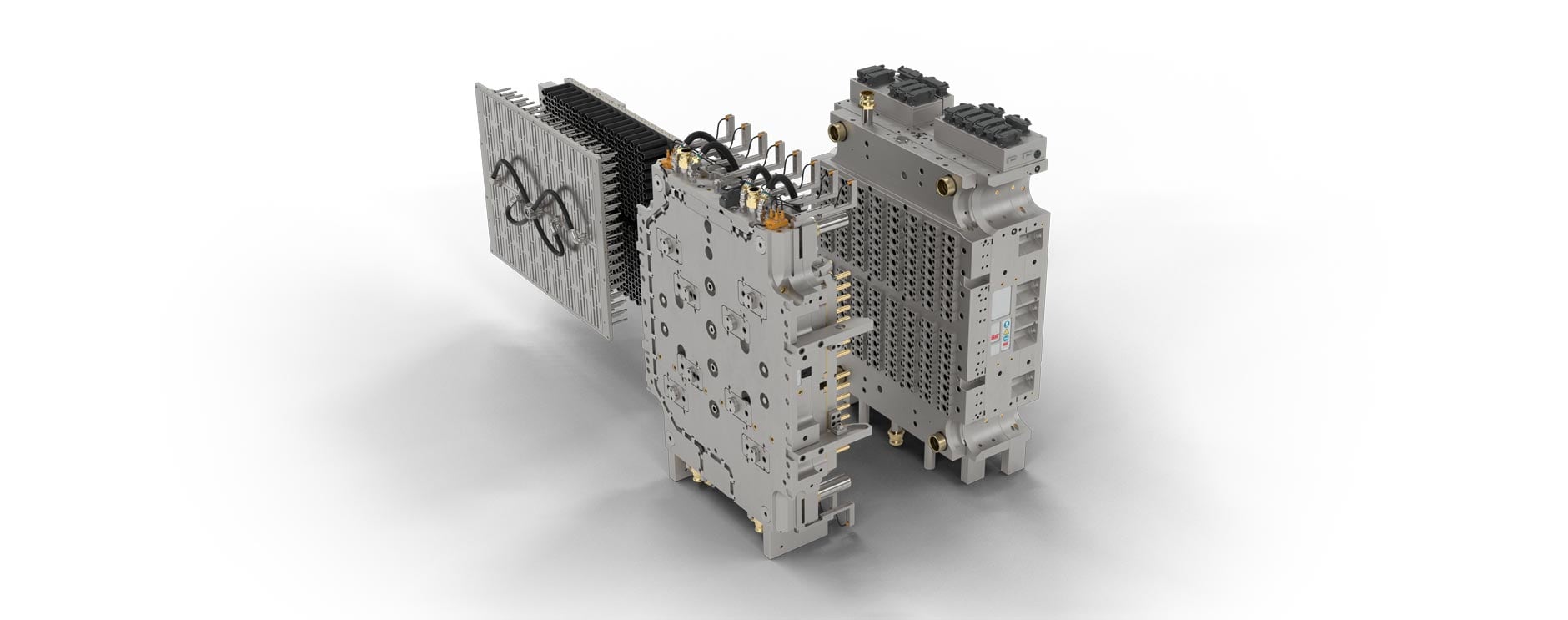
coolMAX
- Up to four stages
- Staggered version available
- Gripper pins, standard or spring loaded
- Air baffle (for thread cooling)
- For all cavitations
- Bladder function available
Take-OUT Plate
- Up to four stages EAOT
- Exchangeable cooling sleeves
- Cooling sleeves with MHTxCOOL
Cold half
- Up to 160 cavities
- Up to 750 g preforms, for bottles up to 30 l
- Preform molds for PE, PP, PLA
optiSTACK
- Innovative two-piece core design
- Increased standardized parts (warehouse stock)
- Quick and easy weight-change
- Quick and easy splitline refurbishment
- Advanced two-piece cooling tube design
- Proven MHT two-piece HP-Stack technology
optiRUN
- For molds from 48 to 160 cavities
- Modular hotrunner packages
- Small-volume individually regulated heating zones
- Perfectly balanced heat distribution
- Cooled adapter plates
- Vulcan II components by default