Adaptation of brewing technology enables production of vegan food alternatives
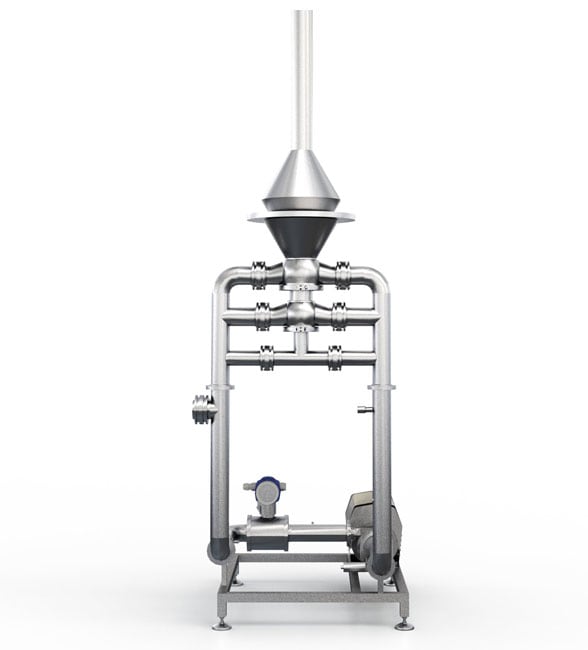
Vegan alternatives to meat, dairy and eggs are gaining popularity around the world – and the resulting market potential is enormous. The Krones Group offers producers numerous options to help them utilise the full potential of alternative proteins. For plant-based products such as oat drinks, Krones has been offering the requisite process technology, in different variants with suitable line layouts, for some time now. In early 2023, the portfolio was expanded to include technology for precision fermentation.
In precision fermentation, animal or plant cells are programmed or optimised to create certain products like enzymes, fats, proteins, vitamins, flavourings and natural pigments. Proteins made by fermentation can then be combined with other ingredients and further processed to imitate meat, egg or milk products.
Biomass production using Steinecker Poseidon technology
A concrete example for cultivating and replicating such proteins is biomass production. For this process, cells are placed in a tank, where their growth is stimulated. And that is where Steinecker comes in, with its own bioreactor. Developed on the basis of the Poseidon fermentation unit, which has proven its useful-ness in the brewing arena, the bioreactor uses a circulation system instead of an agitator. The circulation system is equipped with aseptic valve technology from Evoguard and a low-shear aseptic pump. With this technology built into a sterile tank with familiar steam and condensate barriers, the system is ideal for both cell cultivation and fermentation.
The bioreactor from Steinecker is especially well suited for producers wanting to operate on a large scale. That is because, for tanks larger than 25,000 litres especially, it is far easier and more cost effective to integrate a circulation system than an agitator. That being said, Steinecker always designs its bioreactors to precisely match the fermentation process and the customer’s wishes and seamlessly integrates them into an overall line concept. Steinecker always takes a flexible approach, accounting for each customer’s indi-vidual specifications. As such, the company can also deliver conventional bioreactors featuring an agitator instead of a circulation system.
Download
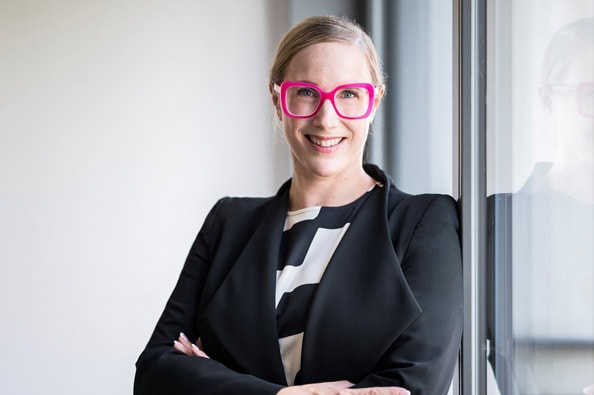
Dr. Anne-Kathrin Bräu
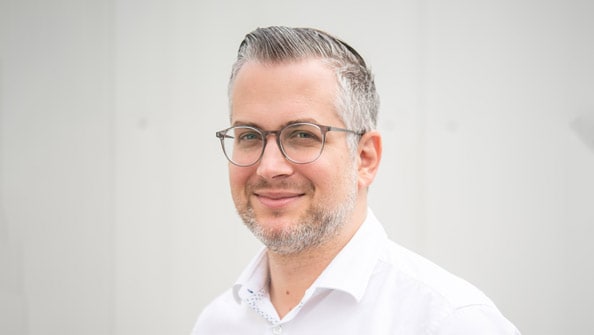
Peter Mörtl