News from the Krones Lifecycle Service
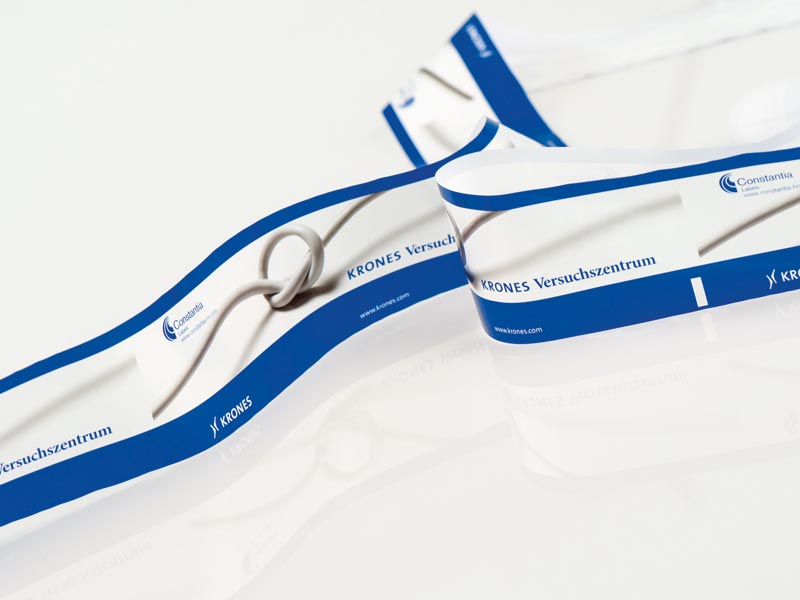
Krones is always there to help its clients, not least after they have purchased a new machine – not only as a service provider, but also as a partner they can always rely on. Ever since last year’s BrauBeviale, Krones has defined its role as a “Partner for Performance” to its clients. The focus here is invariably on a profitable, dependable, cost-saving, efficient production process. And this year, too, the Krones LCS will be showcasing new products and services that meet precisely these requirements:
Upgrades for the Contiroll HS labelling Station
In order to keep the field-proven technology of the Contiroll HS labeller in line with the latest state of the art at all times, Krones offers numerous updates for the hotmelt station: the improved design of the spring-loaded feed roller, for example, enhances the dependability and ergonomics of the production process. The markless sensor is an alternative to existing UV register mark detectors, one that cuts the material costs involved: since a register mark for defining the cut-off point is no longer required, the overlap of the wrap-around labels can be reduced to a technically viable minimum. What’s more, the client thus acquires more freedom for designing his labels. There’s an update for the station’s hotmelt unit, too: the glue roller’s innovative surface structure, plus a new glue scraper, reduce glue consumption by up to 30 per cent, for example. The degree of soiling around the labelling station, can likewise be perceptibly downsized, which in its turn is reflected in reduced maintenance and cleaning intervals.
Line relocation
Investing in pre-owned machines instead of new ones is quite a common practice – not least because of the persuasively favourable time and cost factors involved. But it’s not quite so usual to dismantle an existing line at its old production facility and install it again in its entirety at a new location. But this is precisely the concept behind the line relocation option. To make sure the entire removal runs smoothly, right from the very first minute an experienced Krones project team handles concept formulation, planning, and execution of the line relocation job. Krones will, of course, also overhaul individual assemblies on request, or support the client in integrating additional new or pre-owned machines.
Embedded staff
With both new and existing lines, questions or problems can repeatedly be encountered among the production staff. With embedded staff, Krones offers direct support from its own machinery experts: a service technician accompanies the client’s own team on site over a lengthy period, and assists them with their daily tasks in the bottling hall, and will, for example, give them a hand in trouble-shooting, maintenance planning, or operating the machines. The synergetic effects are obvious: the production staff learn how questions or problems can be solved quite simply on the spot, and improvements can be lastingly implemented as a joint effort.
Download
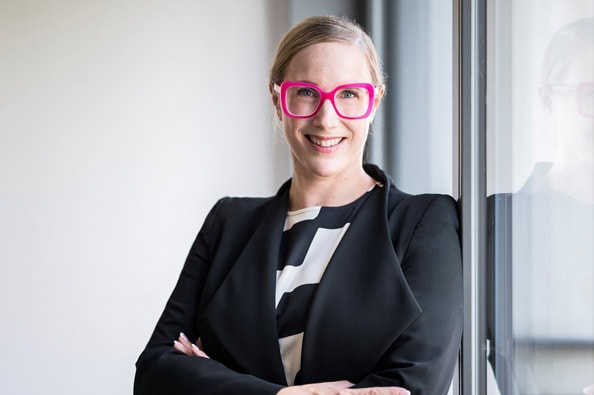
Dr. Anne-Kathrin Bräu
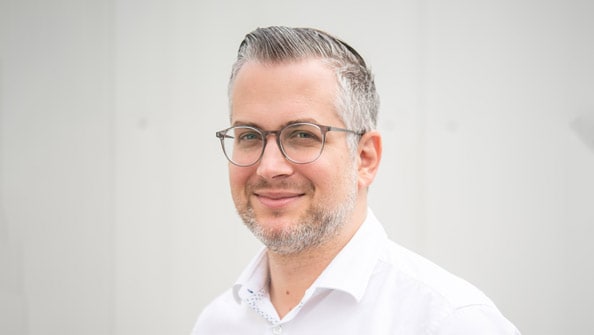
Peter Mörtl