Blow-moulder-filler block for non-carbonated water
Well thought-out block philosophy
The Contiform Bloc BF-C promotes block technology decisively. How that? It represents the block concept with a determination that is unrivalled. Not only does the Contiform Bloc BF-C combine individual machines, but it also is designed as a holistic system with one central unit each for the control system, the drive and the operation.
At a glance
- Functions: Stretch blow moulding, filling and capping
- Output: up to 55,000 containers per hour*
- Processing range:
- Non-carbonated water
- Cylindrical and square PET containers
- Standard and lightweight containers
- Container volume up to 2.0 litres
- Containers of up to 100 percent rPET
BF-C = Blowing, Filling, Compact
*depending on the processing range
Functions and structure
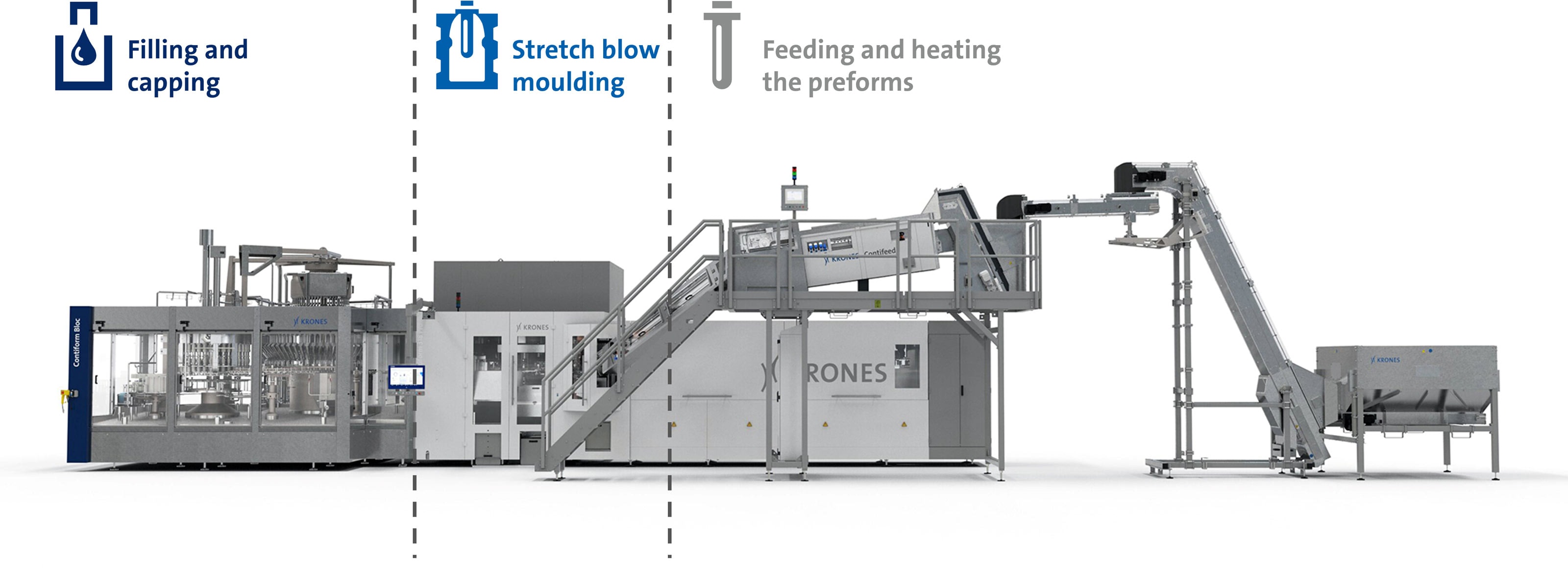
- Up to 30 per cent less space required in the line compared to individual machines
- Uniform lubrication and safety concept and drive control
- Central HMI for complete operation and PLC for all control functions
- No transfer starwheels between the main modules
- No rotary media manifold in the filler
- Operation possible with one single operator
You can be curious: The fourth generation of the Contiform is already in the starting blocks.
Bottle design and moulds
Creative and in line with the market
At a glance
- Four production centres worldwide with state-of-the-art manufacturing technology
- Container design experts at all four locations
- Design and production of mould types for all Contiform series
- Mould validation on our own technical centre systems
Benefits to you
- Customer-oriented consulting: Creative, functional, unique
- Individual designs with a view to customer requirements and feasibility in the beverage line
- Experience from more than 20,000 moulds per year
Benefits
Focus on the essentials
The Contiform Bloc BF-C has been planned as a single, integrated machine and it is designed exactly for one defined application. That's why it is particularly cost-efficient and has a central touch screen for all functions.
One operator for all machines
The block is designed as one unit in which all essential control and function elements are centrally combined. This way, just one operator can easily operate the entire Contiform Bloc BF-C on his own.
Efficiency on smallest space
The Contiform Bloc BF-C requires up to 30 % less space than a blow moulder and filler installed in a conventional single machine arrangement. In addition, the compact line layout reduces potential sources of interference.
Energy savings
From the servo drives to the electromagnetic and compressed-air free stretching systems: The topic energy efficiency goes all the way through the block just like a red thread. Particularly ambitious savings targets can also be achieved with the air recycling system, which is part of the energy-saving package.
Cost-efficient customisation
The pre-defined option packages enable to adapt the block to special requirements and keep the costs for the commissioning time low at the same time.
Beverage containers made from rPET
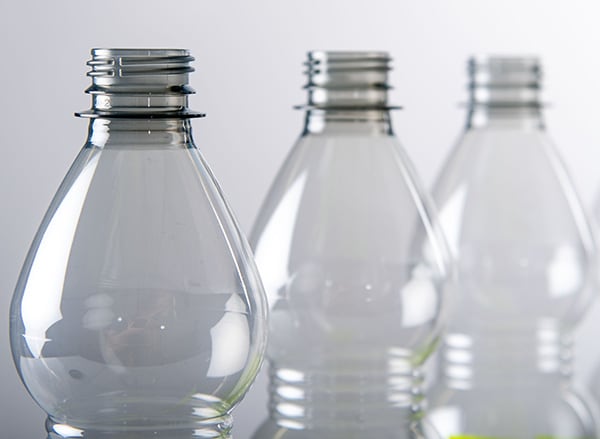
Material properties, processability, food grade quality: you can find all kinds of interesting facts about the use of recycled PET in our free white paper.
This is why the Contiform Bloc BF-C is enviro-classified
Energy efficiency
- Increased station performance during stretch blow moulding and labelling
- Reduced energy consumption thanks to the omission of transfer starwheels and redundant components
- Lowest possible heating energy requirement through energy optimisation of heating zone and heaters
- Energy-efficient separated vacuum during labelling
Media efficiency
- Efficient cooling of the entire block
- Air Wizard Triple air recovery system
- No compressed-air consumption during the filling process
Environmental compatibility
- Use of enviro-compliant lubricants
- Recoverable CIP media