Capper models for a wide range of applications
Good, reliable sealing
Beverage containers are used in various sizes and shapes worldwide and accordingly there is great diversity in container closures. With the Krones cappers, you can reliably apply all common cap types to containers.
At a glance:
- Wide portfolio
- Plastic screw caps (incl. tethered caps)
- Crowns and ring-pull caps
- Aluminium roll-on caps
- Press-on caps
- Suitable for both neck handling and base handling
Attached caps: Tethered caps
To ensure that the caps on beverage containers of PET no longer get lost so easily and end up as waste in the environment, and as of 2024, in the EU, they will have to remain connected (tethered) to the packaging once opened.
Basically, at tethered caps, a distinction must be made between hinged caps and screw caps:
- Hinged caps – also known as flip lids, flip tops and thumb-ups – have a design which keeps them permanently connected to the bottle right from the outset.
- With screw caps, on the other hand, the connection between container and cap must be realised by an additional feature.
Krones offers just the right sorting and capping technology for every variant.
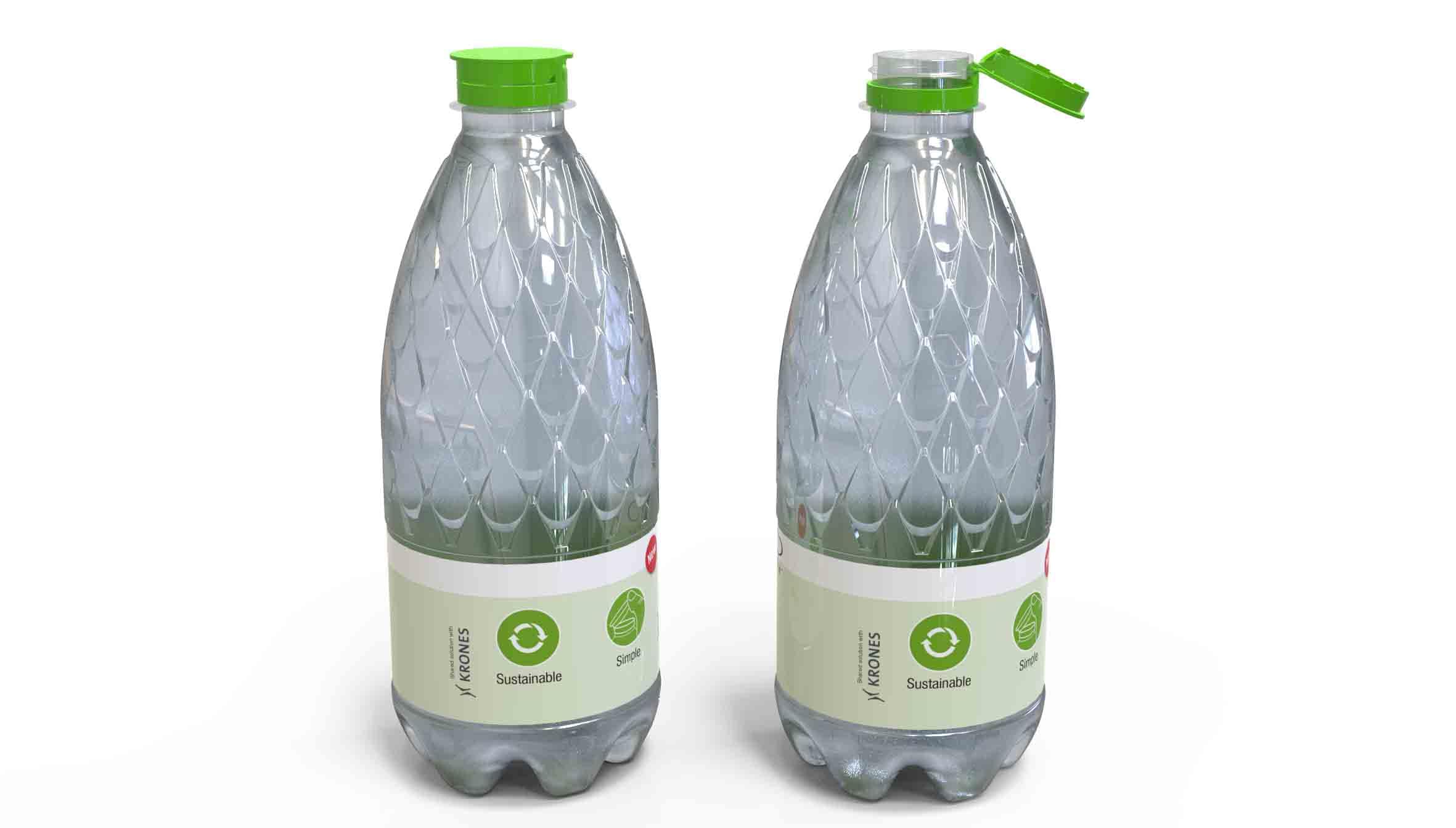
"Tethered" stands for connected: For caps, this means that they remain connected to the bottle even after opening.
The portfolio
Field of applications | Output range | |
---|---|---|
Modulcap CM* screw capper for plastic caps
* C: Chucks (cap retainers), M: Mechanical |
Single-threaded and multi-threaded caps**:
|
Up to 84,000 containers/h (depending on the cap type) |
Modulcap CS* screw capper for plastic caps
* C: Chucks (cap retainers), S: Servo motor |
Single-threaded and multi-threaded caps**:
|
Up to 84,000 containers per hour |
Modulcap GS* screw capper for plastic caps * G: Grippers (gripping head), S: Servo motor |
With the servo-driven screw capper for plastic caps, there is also an optional variant with gripper in addition to the one with cap retainer: This way, non-rotationally symmetric caps such as caps with flaps or recessed grips can be processed as well. Tethered caps can also be processed with the Modulcap GS. Apart from this special feature, this machine type is similar to the Modulcap CS in terms of design and mode of operation. |
Up to 84,000 containers per hour |
Modulcap CP/GP* press-on capper for plastic caps * CP: Chucks (cap retainers), Press-on cap | GP: Grippers (gripping head), Press-on cap |
Non-screw caps |
Up to 84,000 containers per hour |
Modulcap CLR* Krones screw capper with rotary lift motors * CLR: Chucks (cap retainers), Linear Rotary |
Screw and press-on caps (without orientation) |
Up to 84,000 containers per hour |
Modulcrown crowner |
|
Between 10,000 and 120,900 bottles per hour |
Aluminium Roll-On Capper |
|
Between 10,000 and 60,000 bottles per hour |
** With the appropriate change parts
Benefits
Caps are fitted perfectly
Use of a hysteresis clutch ensures screw caps are applied at a constant force.
Can be optimally cleaned
The capping heads can be cleaned perfectly with hot water or foam.
Hygienically optimised design
The drives are positioned to reliably prevent germs from being spread into bottles while they are still open.
Caps are fitted perfectly
The servo controller for the capping process precisely monitors the application torque. This ensures that roll-on caps are applied at a constant force.
Reliable cap feed
The caps are hygienically conveyed to the pick station.
Easy maintenance
All component groups have a lubrication-free and maintenance-free design
Can be optimally cleaned
The machine can be cleaned very effectively with foam and spray disinfection. The open design of the pick station and capping cone ensures that individual parts are readily accessible.
- Fully controllable capping process (at the version with servo drive)
- Version in hygienic design: Machine to be cleaned completely
- Robust design
- Freely programmable and individually adjustable capping movements (independent of contour and cap type)
- Highest degree of freedom in cap design and unscrew values
- Targeted data analysis possible
- Low installation height thanks to compact design
- Better heat dissipation due to optimised housing
Precision
Crowns enter the line with a defined alignment and are precisely positioned on the transfer plate by a draw-in magnet.
Designed for practical applications
Bottle-neck centring ensures that even bottles with inaccurate dimensions are reliable sealed.
Hygiene
Numerous refinements and optional equipment on the agitator, feed chute, top part and capping heads themselves deliver a major hygiene boost during production.
Suitability for retrofitting
Numerous new features can also be retrofitted to existing crowners from Krones.
Flexibility
The thread and tuck-under roller arms can be quickly adjusted to the plunger dimension.
Can be optimally cleaned
The capping heads can be cleaned perfectly with hot water or foam.
Retains its value
The stainless steel design of the roll-on capper is highly resistant to cleaning agents and disinfectants.