Dustin Olson, Chief Executive Officer of PureCycle, explains: “The polypropylene market produces 200 billion pounds of plastics per year, and because there simply has not been the appropriate technology, less than 10 percent of that material is recycled. PureCycle has developed groundbreaking technologies that enable us to clean these plastics at the molecular level, removing color, odor, and contaminants.”
PureCycle’s advanced solvent-based technology converts polypropylene feed stock into a sustainable, ultra-pure recycled resin with like-new characteristics that can be used infinitely. Within the new end-to-end facility, PureCycle has invested in Krones MetaPure technology to wash and prepare all polypropylene stock materials for processing.
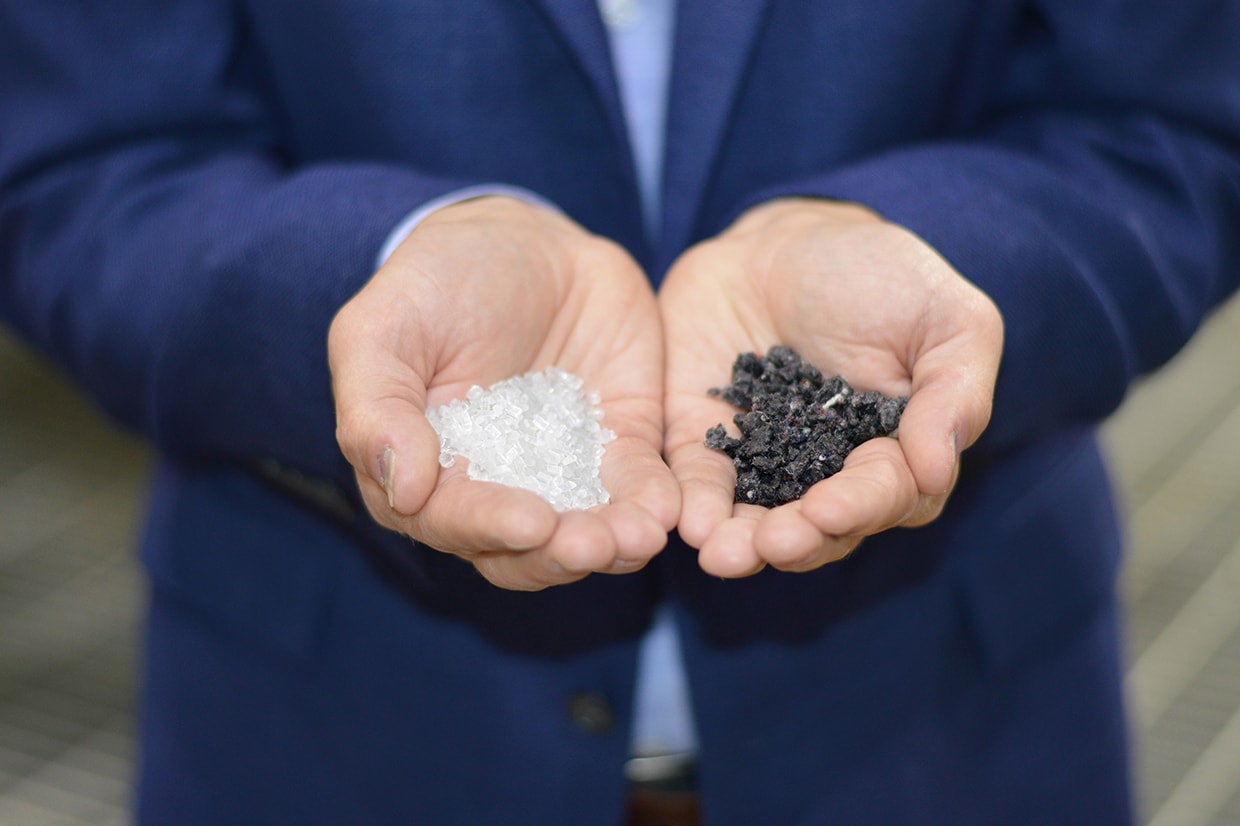
PureCycle