The next evolutionary step in filling beer and CSDs into glass bottles
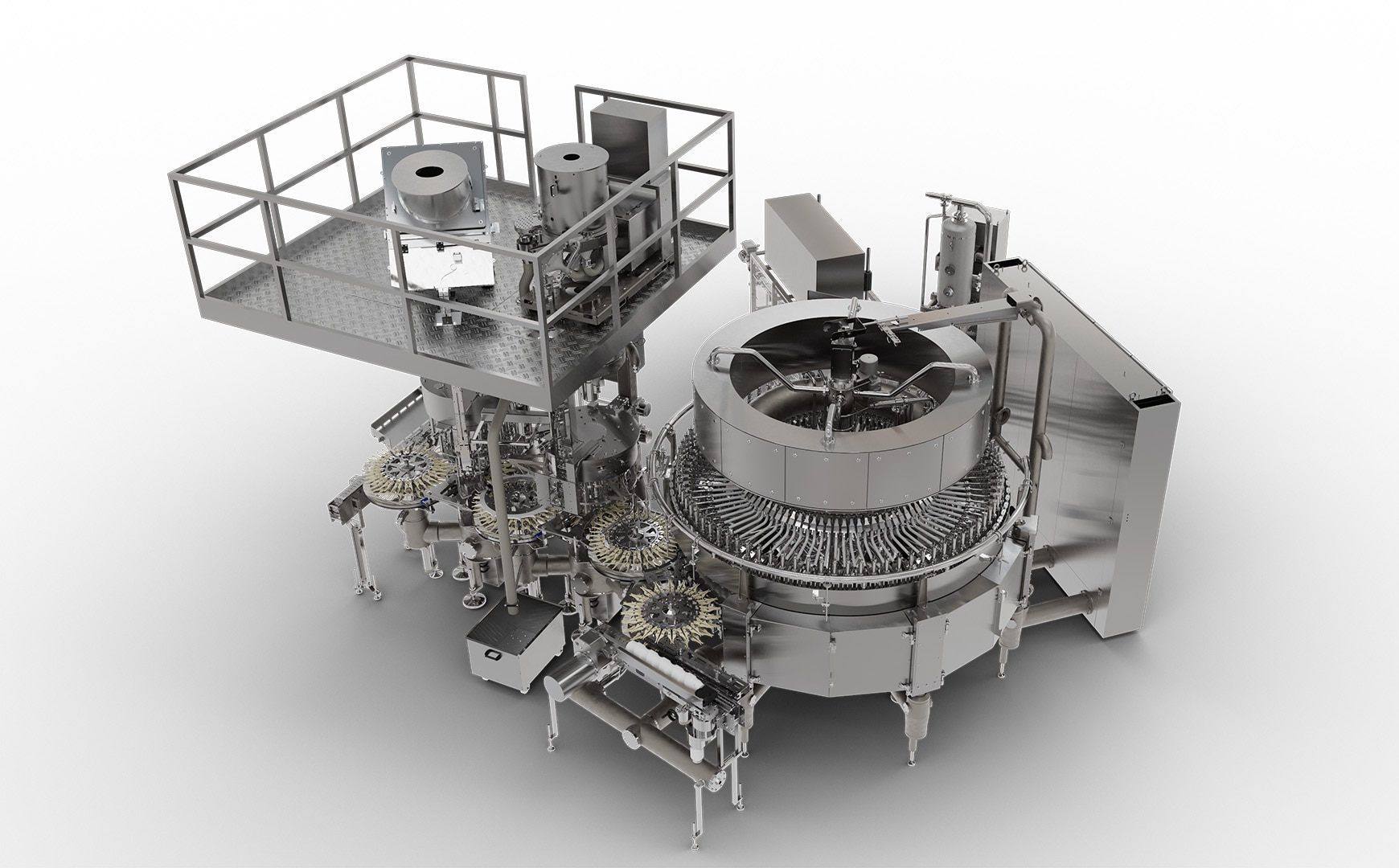
- Increased flexibility in production thanks to optimised and automated operator interventions
- Sustainable filling and capping thanks to new media-saving options
- More compact machine delivers the same performance thanks to new automatic CIP cups
rones works continuously to make its products and solutions more and more sustainable. And now the Krones team has succeeded in taking the Modulfill HES beer filler to the next level with respect to flexibility, sustainability and machine output.
Outstanding results on both oxygen pickup and CO2 consumption
For the first time, Krones is combining the redesigned HES filling valve with a dry-running vacuum pump to synergise the advantages of both systems. For example, a revamped arrangement of the individual functions within the filling valve results in optimised flow conditions. That, combined with “lower” vacuum levels in the filling process, enable the Modulfill HES to set entirely new standards for oxygen pickup and CO2 consumption in conventional beer filling.
Yet another plus in terms of product quality is the intelligent process-gas control system. A sensor measures the residual oxygen in the headspace of the filler bowl and thus makes it possible to monitor and dynamically regulate oxygen pickup to the desired level.
Digital features reduce the need for manual interventions
Krones has added automation to the probe adjustment and to the CIP cups. That makes it possible to achieve the same performance on a more compact machine using the automated CIP cups. During cleaning, the necessary interventions are reduced to an absolute minimum, which in turn significantly shortens scheduled machine downtimes and increases overall equipment effectiveness (OEE). Machine change-over times are likewise shortened thanks to the use of the latest generation of the MultiGuide Base multi-functional clamping star-wheel.
A further digital feature is the automatic filling-pressure control system. Inline measurement of the product temperature inside the filler bowl and information on the CO2 content (based on the product at hand) can be combined to calculate the real saturation pressure and thus regulate the filling pressure. This reduces the need for operator interventions when restarting the machine, for instance in order to prevent foam-over.
Download
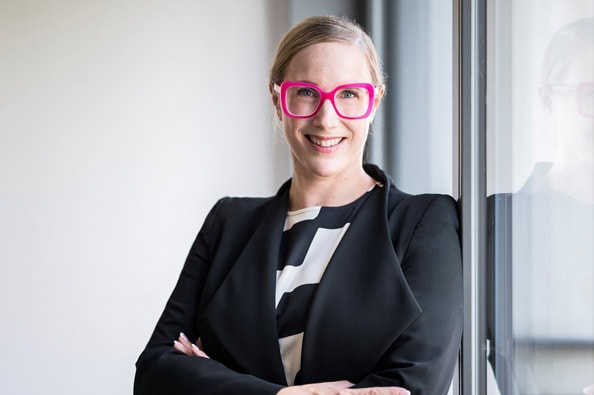
Dr. Anne-Kathrin Bräu
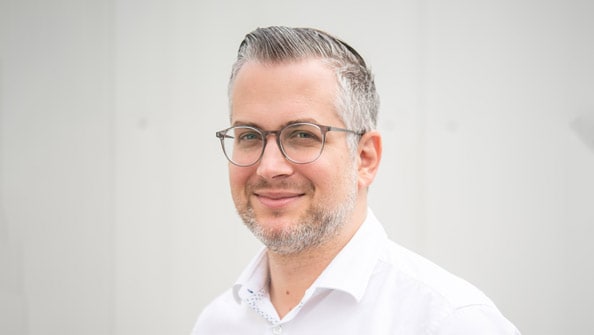
Peter Mörtl