Digital operator support in your line
As a production plant, you can use Shopfloor Guidance to simplify the organisation, prioritisation, management and documentation of all pending tasks. Changes to the machine status are discovered early by the system: If an intervention is required, Shopfloor Guidance actively informs the responsible operators. With clear instructions, the responsible groups in production are supported in solving problems quickly and preventing negative effects on production.
At a glance:
- Automatically bundles and prioritises all tasks, informs the responsible personnel and thus helps to resolve problems in the line efficiently and at an early stage
- Detects anomalies in production by monitoring individual data and limit values
- Enables early reaction to required material interventions (processing and operating materials) and thereby prevents machine downtimes
Active notification for relevant interventions
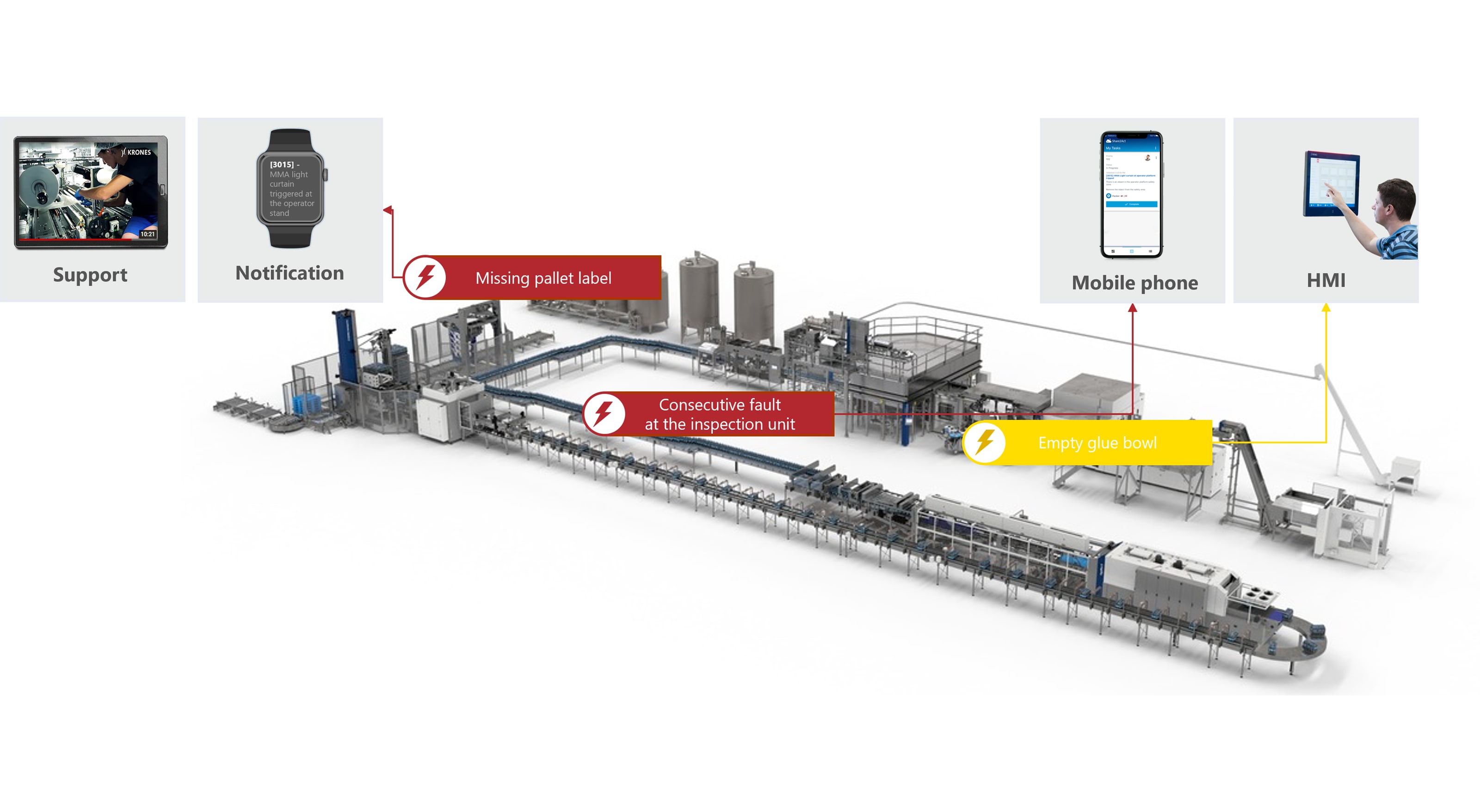
Use Case: Operator interventions
Pasteuriser:
- Tracking of the temperature logger and active information for the operator if the regular quality and process control is completed
Palletiser:
- Detection of a faulty layer during pallet loading → display on touch-screen and information to mobile end devices
Use Case: Consumption
Continuous monitoring of the fill levels to prevent downtimes due to lack of materials
Labeller:
- Labels
- Glue
Packer:
- Clips
- Glue
- Oil
- Film
- Carton blanks
- Dividers/divider inserters
- Lubrication
Depalletiser/palletiser:
- Empty pallet/layer pad/top frame magazine
- Lubrication
Use Case: Maintenance
Labeller:
- Flow meter for monitoring of the air consumption to detect incorrect settings, faults and leakages (entire machine and labelling stations)
- Monitoring of the rollers in the machine head for vibrations to detect anomalies
Use Case: Quality
Stretch blow moulder:
- Continuous monitoring of the pressure dew point temperature during the blowing sequence to ensure a high bottle quality
- Active notification if there is a machine downtime or if materials are required, regardless of where the operator is in the line
- Grouping and prioritisation of all necessary interventions
- Escalation path and forwarding option in the event of non-compliance
- Condition monitoring: Useful and proven use cases already integrated
- Digital knowledge database: Clear instructions for planned and unplanned interventions
Shopfloor Guidance in detail
Monitoring of machine conditions
Independent creation and management of alarms
- Definition of individual monitoring and escalation rules based on linked data points
- Condition monitoring systems can thereby be based on the following conditions:
- Limit value violations
- Comparisons
- Duration
- Frequencies
- Monitoring rules can include several data points with up to 72 conditions
- Calculated data points based on static methods (e.g. average, median, total)
Visualisation of machine data for improved transparency of production behaviour
The selected data points are visualised with a line diagram:
- Data points can be analysed across machines
- Historical display aggregated over the last few hours or with reference to a freely selectable time period
- Visualisation of real-time data
- Data export possible
- Interpretation of data facilitated through zoom function
Providing support in all areas of production
Benefits to you
Shortening downtimes
Shorten the time span in which employees are informed about relevant downtimes. Relevant downtimes refer to those where the machine does not restart automatically.
Minimum user inputs
Receive an overview of all of the interventions relevant at the current time. Completed tasks are automatically closed once the machine starts producing again or the message has been reset.
Preventing downtimes
Prevent the machine from stopping due to a lack of processing and operating materials (for examples labels or film). Use critical machine information effectively in the entire process.
Active notification
Be informed about tasks and anomalies directly via push notification (Android and iOS) or email.
Collaboration
Create the conditions for efficient teamwork through the continuous synchronisation of the task status and always see who is working on what and may possibly require support.
Keeping track
Work with a tool which helps you to manage, structure and complete your tasks. Create your own rules for monitoring limit values as required.