Can filler and seamer from a single source
Also available with a small clean room
With the Modulfill Bloc FS-C, Krones is expanding its expertise in can filling. The block solution contains an accumulation of Krones know-how combined with the latest technology. The tried and tested Modulfill VFS-C can filler is block-synchronised with Krones’ own Modulseam can seamer.
For sensitive beverages, such as teas and juices, the Modulfill Bloc FS-C is also available with a small clean room if requested. It does not only score in matters of hygiene, but also requires substantially less space than conventional arrangements.
At a glance
- Block solution comprising can filler and seamer from Krones
- For outputs of up to 135,000 cans per hour*
- Processes beer, carbonated soft drinks, water, juice (hot filling) and non-carbonated beverages
- Process technology according to the dry-floor concept
- Saving media thanks to a closed cleaning system
- Increased output thanks to minimised change-over times
FS-C: Filling Seaming Can | *Depending on the current can format, only with third-party filler
Structure in standard design
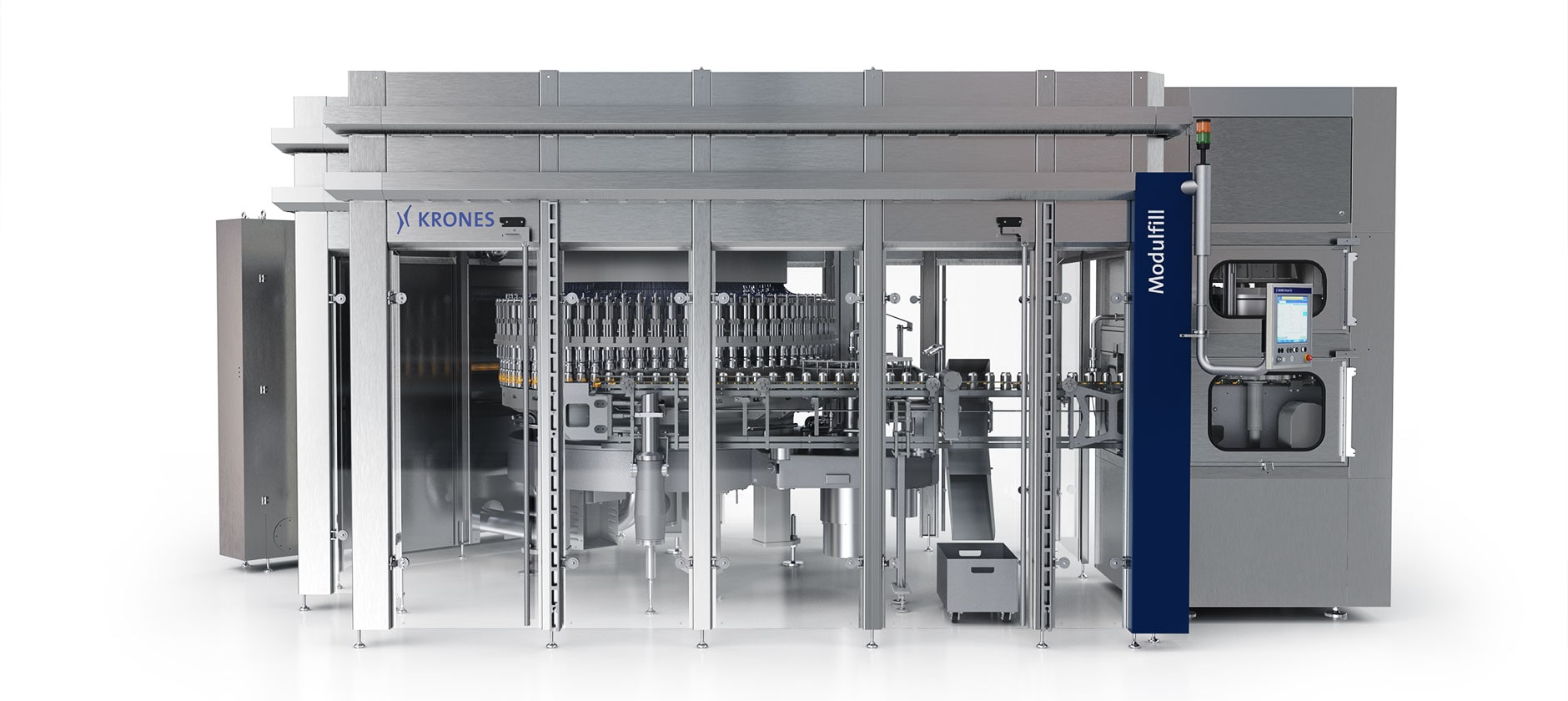
Design with compact clean room
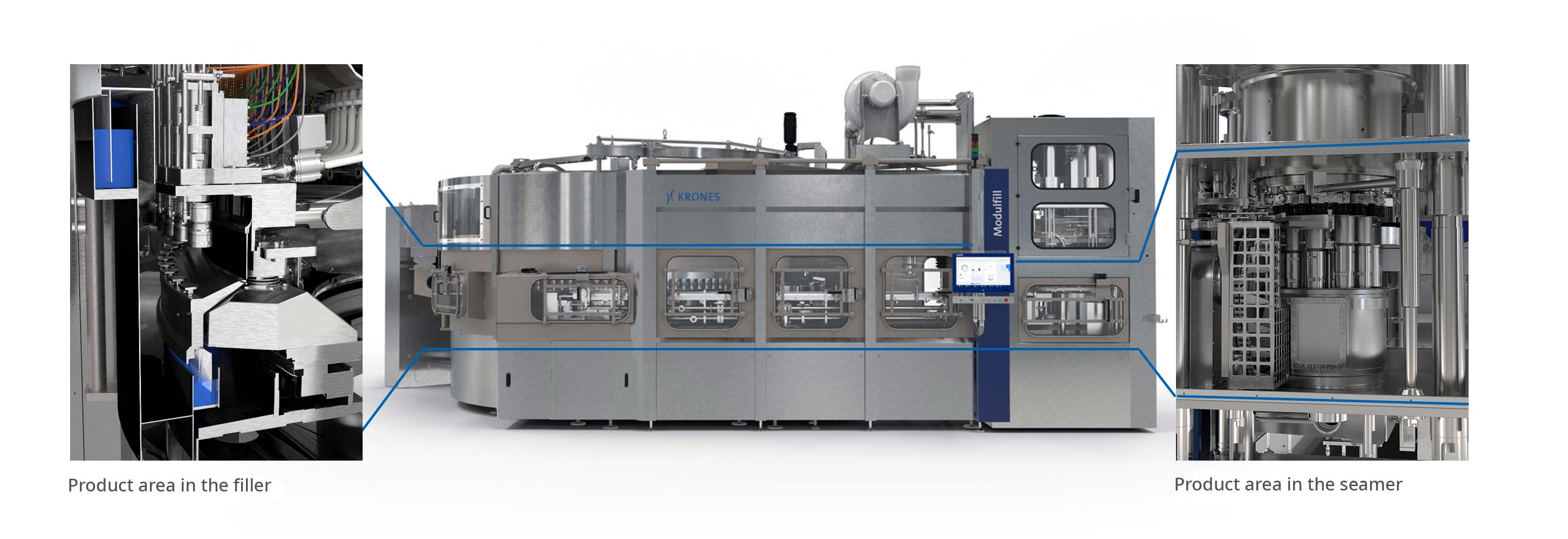
Ventilation system
Benefits to you – with and without compact clean room
Product quality
The volumetric filling valve with inductive flow meter ensures the highest accuracy during filling – and keeps the product quality high. Low oxygen values combined with a 40 percent lower CO₂ consumption ensure that the product quality is high while the media consumption remains low.
Ease of operation
The machines in the block share a joint control panel and the controller.
Quick change-over
Best equipped, even for type and format change-overs: the height adjustment is fully automatic, and quick-change handling parts keep change-over times short, while the combined centring bell can even be used for multiple can formats.
Easy to clean
The entire block has a hygienic design without table top in its standard version and, if required, can be directly connected to Krones CIP and foam-cleaning systems. In the variant with compact clean room, the exterior and interior cleaning are executed simultaneously.
High energy saving
A 30 percent energy saving (compared to conventional drive concepts) can be achieved thanks to the use of servo technology.
Everything from a single source
With its Modulfill Bloc FS-C Krones is offering its first ever block solution for the filling and sealing of cans.
The Modulfill VFS-C enviro stands for the following
Energy efficiency
- Use of the latest PM drives and pumps
- Air dryer with dew-point control (if required)
Media efficiency
- Reduced CO2 consumption
- Minimised water consumption