The intelligent blow moulder process control
Automatic monitoring and intelligent control of the blow moulding process
Ambient temperature or air humidity, preform weight or percentage of recyclate: if such environmental parameters change, for example, then the blow moulding process must also be readjusted or even reset. But instead of using the operators, this job is now taken over by the Contiloop AI intelligent control system – precisely, quickly and fully automatically thanks to artificial intelligence.
At a glance
- Combination of hardware and software: intelligent process control based on artificial intelligence (AI)
- In everyday operation: Contiloop AI measures the most important container parameters, and also the environmental parameters inline and readjusts the blow moulding process if necessary.
- If major changes are planned: the system is retrained via the Krones IIoT platform and thus learns how to adjust the blow moulding process precisely to the perfect bottle quality under the new conditions.
Today’s challenges for the manufacture of PET containers
The unwavering trend toward lightweight containers and the requirement to use up to 100 percent rPET
- Less material and fluctuating material properties place even greater demands on process guidance
The solution: Contiloop AI
The combination of AI-based software and newly developed hardware make it possible to already adjust the crucial blow moulding parameters automatically upon detection of the most minor deviations – and thus maintain the best possible bottle quality.
Continually increasing outputs per blowing station: from 2,000 containers per hour in the year 2000 up to 2,750 today
- The most minor deviations during bottle manufacture have a major impact on the production result very quickly.
The solution: Contiloop AI
The combination of AI-based software and newly developed hardware make it possible to already adjust the crucial blow moulding parameters automatically upon detection of the most minor deviations – and thus maintain the best possible bottle quality.
The operators can work with multiple machines and systems at the same time
- There is less time for manual process guidance and inspection.
The solution: Contiloop AI
The combination of AI-based software and newly developed hardware make it possible to already adjust the crucial blow moulding parameters automatically upon detection of the most minor deviations – and thus maintain the best possible bottle quality.
Contiloop AI at a glance
- In the blow moulder discharge starwheel, the light transmission value of each container are measured at up to 32 position.
- Additional sensor values supply additional information during production, such as:
- Ambient temperature
- Ambient air humidity
- Preform infeed and discharge temperature
- The control system operates on a separate device and compensates production disturbance variables fully automatically.
- The measuring and control data are used for further optimisation and transmitted to the Krones IIoT platform for quality assurance reasons.
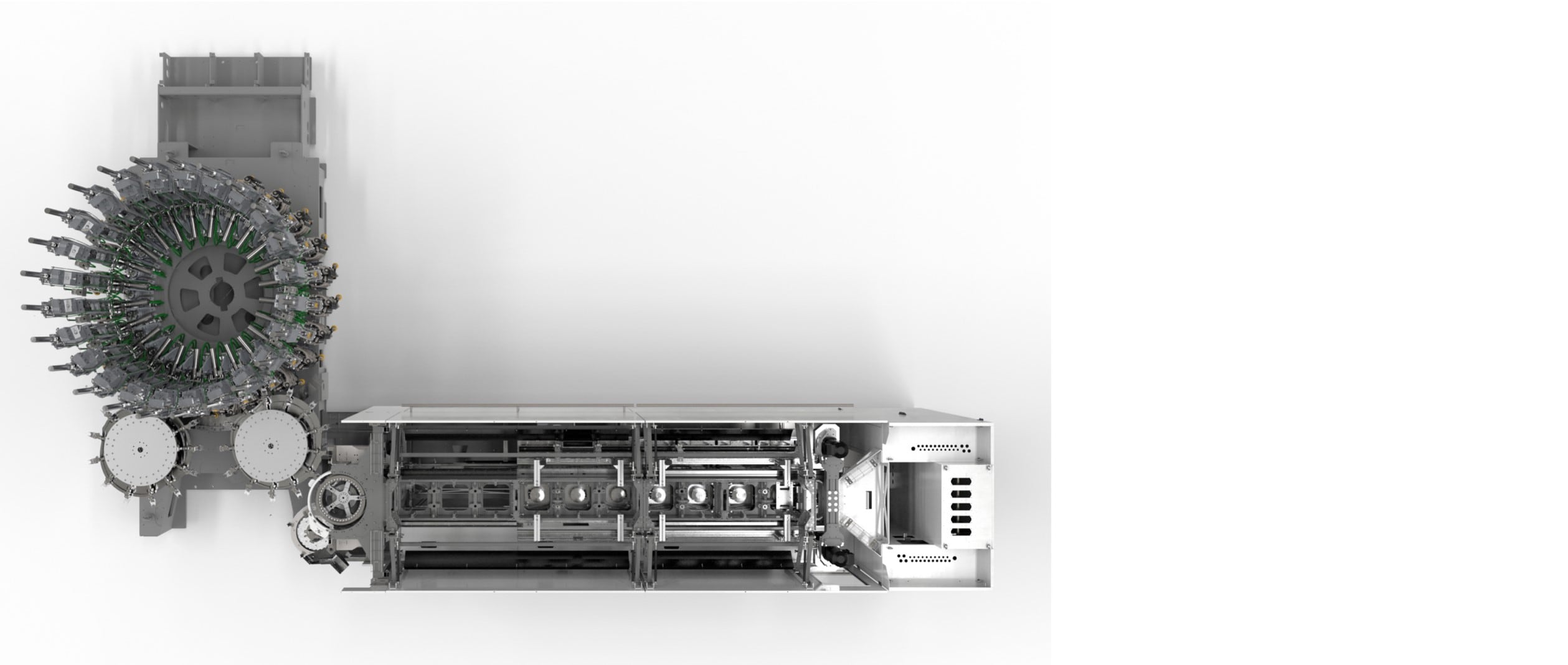
ContiloopAI system with connection to the Krones IIoTplatform
Light transmission measuring unit
Measurement of the ambient temperature and air humidity
Measurement of the preform discharge temperature
Measurement of the preform infeed temperature
Contiloop AI – during production
Contiloop AI – for training and optimising the system
Benefits to you
Less operator intervention
Contiloop AI reacts to changed environmental parameters and automatically readjusts the blow moulding process. As a result, different process profiles (e.g. for day/night shift) do not need to be adjusted, meaning the manual work needed to do so can be avoided.
Independent of operator know-how and experience
The risk of operators making incorrect process adjustments is lowered thanks to the greatest possible omission of manual interventions. A blow moulder with Contiloop AI can therefore also be operated by people who do not have any special process know-how. Personnel costs can also be reduced depending on the line constellation.
Highest container quality
A consistent, very high bottle quality is achieved and the scrap rate greatly reduced thanks to the 100 percent light transmission value measurement and automatic process control using artificial intelligence. A random check will therefore suffice, where necessary.
Production of lightweight and rPET containers possible
Predominantly when using rPET, the process window available is mostly very small. Contiloop AI remains precisely within this narrow corridor and thus ensures that the container quality is not influenced negatively by incorrect manual interventions. Keeping process variation low using Contiloop AI means it is possible to operate at a minimum weight without generating a scrap rate.*
* Compared to blow moulders without Contiloop AI