Filling of beer into glass in a sustainable and flexible way
Further developments for filling beer
We at Krones have been continuously working on further developing our solutions for a wide range of beverage producers. Inspired by the challenges of the future in terms of sustainability and Krones' corporate goals, we have been working on taking our Modulfill HES for beer filling to the next level in terms of flexibility, sustainability and machine output.
At a glance
- Optimisation and automation of operator interventions for more flexible production
- Innovations to save media for more sustainable production
- Revisions to realise more compact machine sizes with automatic CIP cups at the same output
The new features at a glance
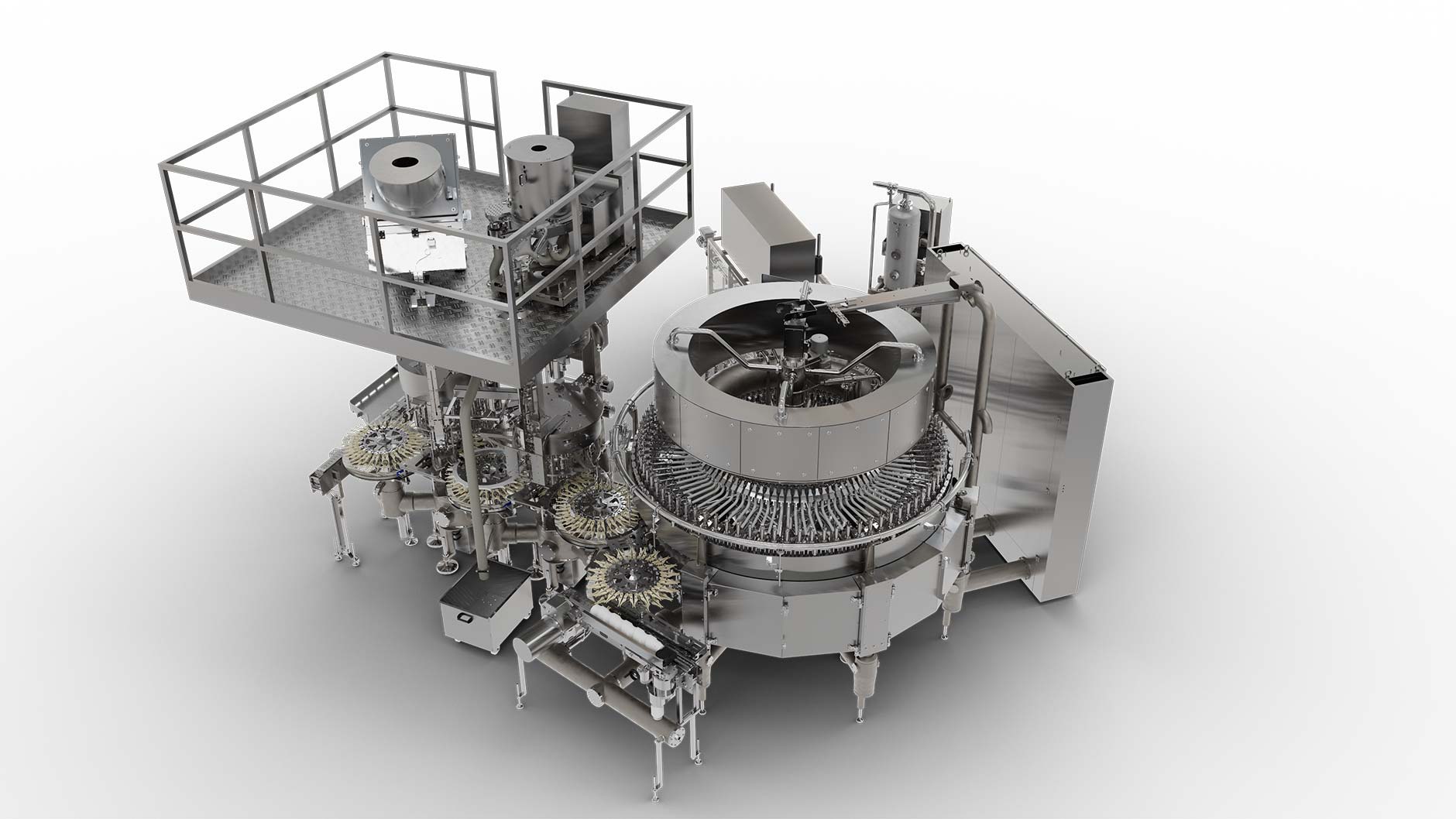
"Facelift" for the HES filling valve
As the central element of the machine, the filling valve is an important component that is continuously being developed and optimised. In order to improve the filling process, the arrangement and cross-sections of the gas channels have been rethought - which not only improves the cleaning result, but also reduces the CO2 consumption during bottle flushing.
Benefits to you
- More sustainable production and improved machine hygiene by eliminating water lubrication for the centring bell lifting cam
- Optimisation of product safety by eliminating wear parts above the filling valve (e.g. rollers of the centring bell lifting unit)
- Optimal cleaning thanks to the hygienic one-piece swirl insert
- CO2 savings through flow optimisation
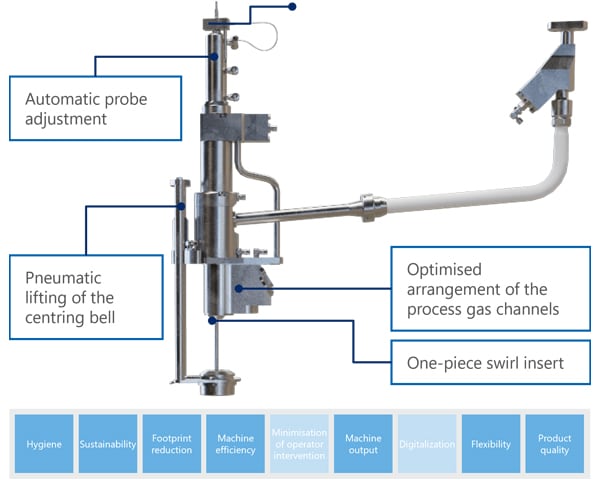
Pump unit with dry-running vacuum pump
By using a dry-running vacuum pump, not only the production can be more sustainable, but also a higher product quality can be achieved when filling beer.
Benefits to you
- Realisation of lower vacuum values during filling
- Optimum hygiene conditions in the machine, since the piping and foam separator are integrated into the CIP circuit as usual
- Significant minimisation of the water consumption during production
- Reduced energy consumption by up to 25 percent*
*during the production, compared to a conventional liquid ring vacuum pump with the same suction capacity
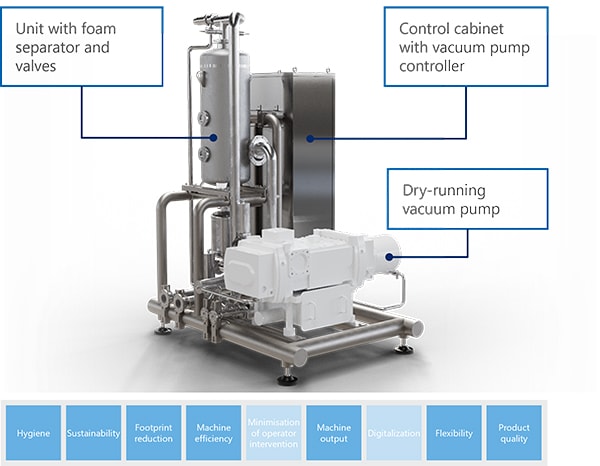
Benefits to you - Reduction of CO₂ and pick-up of oxygen
For the first time, Krones is combining the redesigned HES filling valve with a dry-running vacuum pump in order to maximise the advantages of both systems. A newly designed arrangement of the individual functions in the filling valve leads to optimised flows. Combined with the "lower" vacuum values, the Modulfill HES manages to set completely new standards in conventional beer filling in terms of oxygen pick-up and CO2 consumption.
Benefits to you
- Less oxygen pick-up and therefore a longer shelf life for the beer
- Lower CO2 consumption, which leads to resource savings during production
Automatic probe adjustment and automatically positioned CIP cups
Automated probe adjustment and CIP cups complement each other perfectly, meaning that manual operator intervention at the filling valve is no longer necessary for both type change-overs and cleaning. The new version of the automatic CIP cups for the small filler pitches (87 and 94 millimetres) is installed as part of the lifting cylinder. A pneumatic swivel mechanism swivels the container plate backwards and moves the CIP cup against the centring bell and the filling valve, creating a closed cleaning cycle.
Benefits to you
- More compact machine size possible with the same output
- Automatic and reproducible change-over when changing types with a different fill level
- Cleaning and change-over times reduced to a minimum
- Improved machine hygiene and product quality: No risk of recontamination of the filling valve and probe when the operator removes the CIP cups
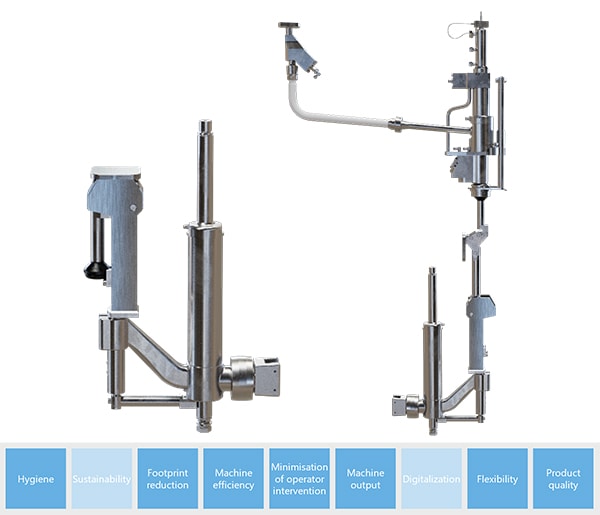
MultiGuide Base clamping starwheels
Not only for the HES filling system, but for bottle handling in general, Krones will be relying on the MultiGuide Base multifunctional clamping starwheels in future. Unlike the handling parts used so far which are designed for just one container format and size, the clamping starwheels can handle the entire range with all conventional bottle formats.
Benefits to you
- Change-over times are reduced to a minimum
- Less space required as the handling parts sets needed so far can be omitted
- No risk of contamination as operator intervention is no longer required in the filling and capping area
- Should a gripper need replacing: Extremely simple and reproducible assembly in just one minute; no fine adjustment necessary
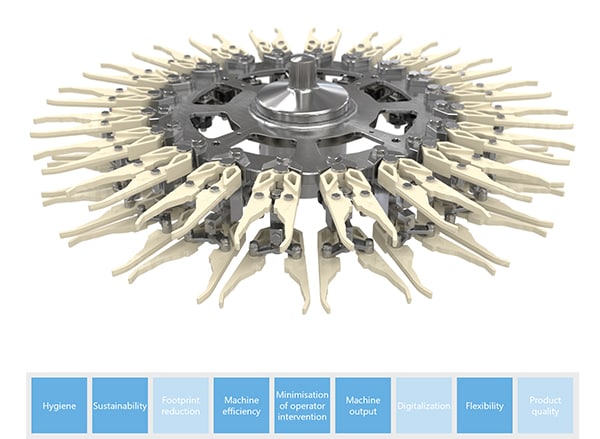
The benefits
Numerous plus points for more sustainability
Krones has tinkered around with scores of regulating screws in order to improve the Modulfill even further when it comes to sustainability. The most significant innovation is the reduction of resource consumption (CO2, water, energy) in the filling process: The optimised filling valve has been combined with a more efficient type of vacuum pump.
Automation and digitalization in the filling process
Product safety is the be-all and end-all when it comes to filling. In order to live up to this credo, Krones is committed to providing our customers with maximum transparency and safety in their production processes. This is made possible by oxygen monitoring, including process gas control and extended broken bottle detection. This way, the bottler knows at all times what is happening in the filling process and can leave the readjustment of any deviations entirely to the filler.
Improvements in flexibility and machine output
Time is money - and manual activities in particular are system downtimes that are planned but can easily be avoided completely. For example, the probes on the Modulfill HES can be adjusted automatically, CIP cups can be moved into position automatically, handling parts change-overs can be reduced to a minimum and emptying can be fully automated.
Improved product quality and machine hygiene
The lower oxygen pick-up with the revised HES filling valve enables our customers to achieve a longer shelf life for their products. Not only is the consumption of resources reduced, but also machine hygiene is significantly improved by eliminating wear parts and dispensing with water lubrication above the filling valve.
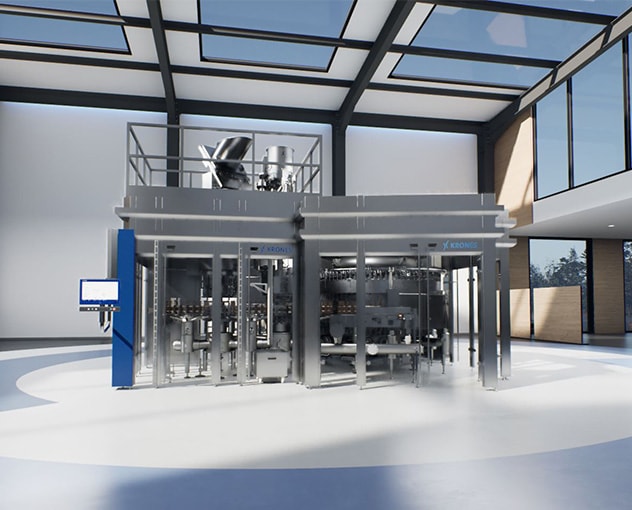
Inspired by the challenge of the future in terms of sustainability and Krones' corporate goals, we have been working on taking our Modulfill HES for beer filling to the next level in terms of flexibility, sustainability and machine output.
Inspired by the challenge of the future in terms of sustainability and Krones' corporate goals, we have been working on taking our Modulfill HES for beer filling to the next level in terms of flexibility, sustainability and machine output.