Aseptic system with H₂O₂ bottle sterilisation
Compact and completely dry for all aseptic products
PET-Asept D takes the consistent road from the very beginning. The system relies one hundred percent on a dry sterilising medium and germs are not given a chance.
At a glance
- Filling of aseptic products
- Suitable for all bottle shapes
- Bottle sterilisation by means of hydrogen peroxide (H2O2)
- Output range from 12,000 to 36,000 bottles per hour*
- Particle filling of up to 10 x 10 x 10 millimetres possible
- Also available as PET-AseptBloc D with blow moulder
D = Dry
*Based on: 500 ml bottle
The key components
Variant: PET-Asept D without blow moulder
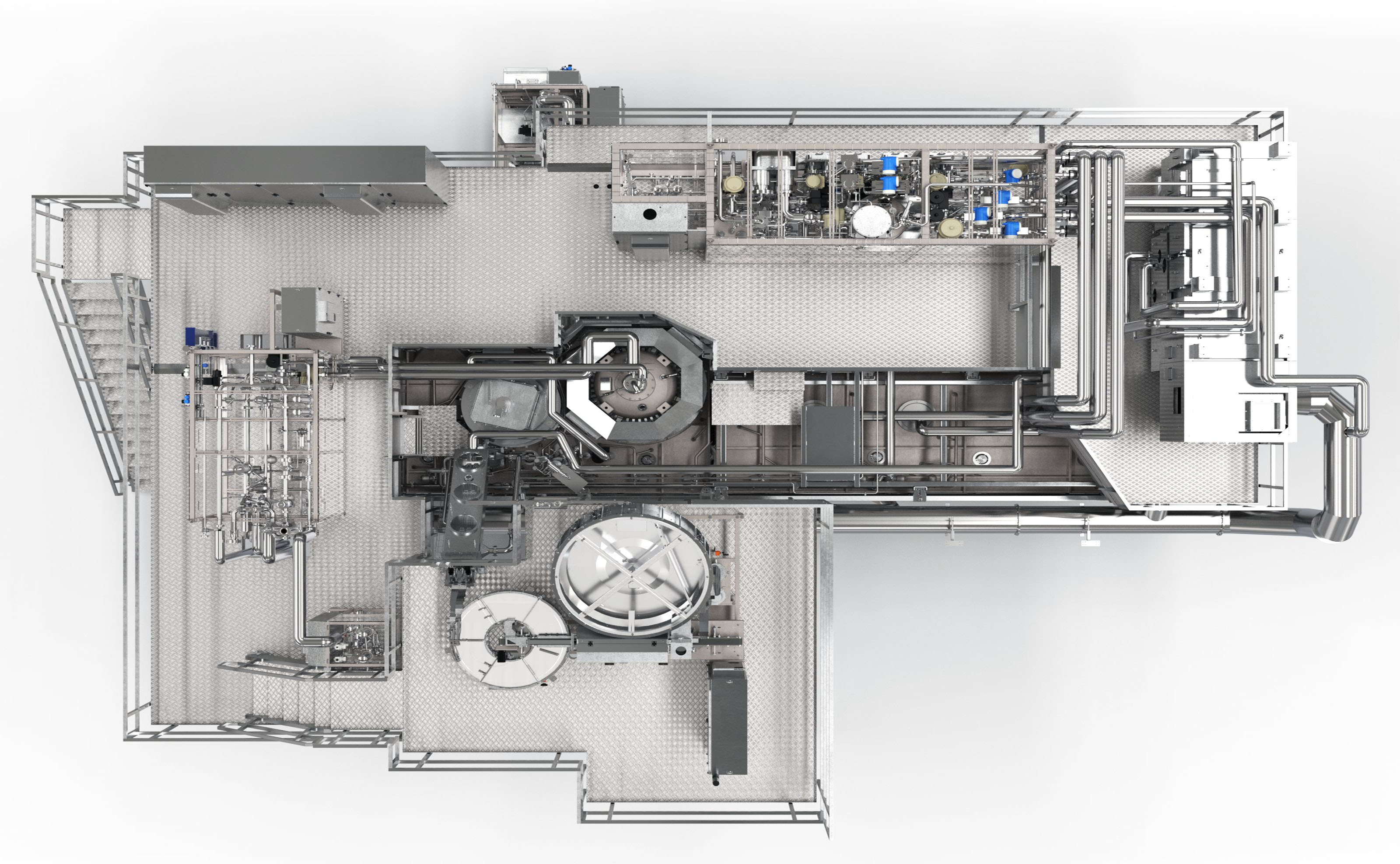
Air Handling Unit
- All filters and ventilators in one unit
- Piping as integrated component of the air handling unit
- Centralised exhaust air pipe system
- Direct air guidance, no pressure cascade required
- Simple sterilisability of the HEPA filters
Cap sterilisation module
Aseptic capper
- Every capping head has its own separate servo drive.
- A transfer tunnel separates the sterile area from the outside area.
- The proper technique for every cap – overcaps with round bottle possible!
Aseptic filler
- The appropriate filling valve for the most wide range of products – still and carbonated
- It is also suitable for beverages with (fruit) pieces of a size of up to 10 x 10 x 10 millimetres
Benefits to you
Pinpoint production
Filling to the last drop: The system uses the remaining product quantity in order to calculate exactly how many more PET containers and caps are still to be sterilised.
Fully-automatic change-over
Handling parts change-over at the filler and the capper can be performed up to a defined output without any manual interference.
Broad spectrum
The line covers outputs of 12,000 to 36,000 bottles per hour and is also suitable for filling products containing particles.
High availability
The PET-Asept D system produces continuously for up to one week at a time! The subsequent cleaning cycle from the last to the first bottle is done within 150 minutes.
No condensation
Clever: The treatment of warm bottles with warm gas prevents the occurrence of condensation. A fast and efficient sterilisation process results.