Wet bottle sterilisation for aseptic products
Absolute product safety, even under extreme conditions
The PET-Asept L system has proved its worth among beverage producers all over the world. It provides reliable results, even under problematic ambient conditions and, at the same time, requires amazingly low maintenance.
At a glance
- Latest version of a system proven all over the world
- Aseptic filling of all products
- Suitable for all bottle shapes
- Bottle sterilisation by means of peracetic acid (PAA)
- Output up to 65,000 bottles per hour*
- Re-use of rinsing water
- Integrated, decentralised ventilation technology by Krones
- Also available as PET-AseptBloc L with blow moulder
L = Liquid
* Based on: 500 ml bottle
The key components
The design: PET-AseptBloc L with blow moulder
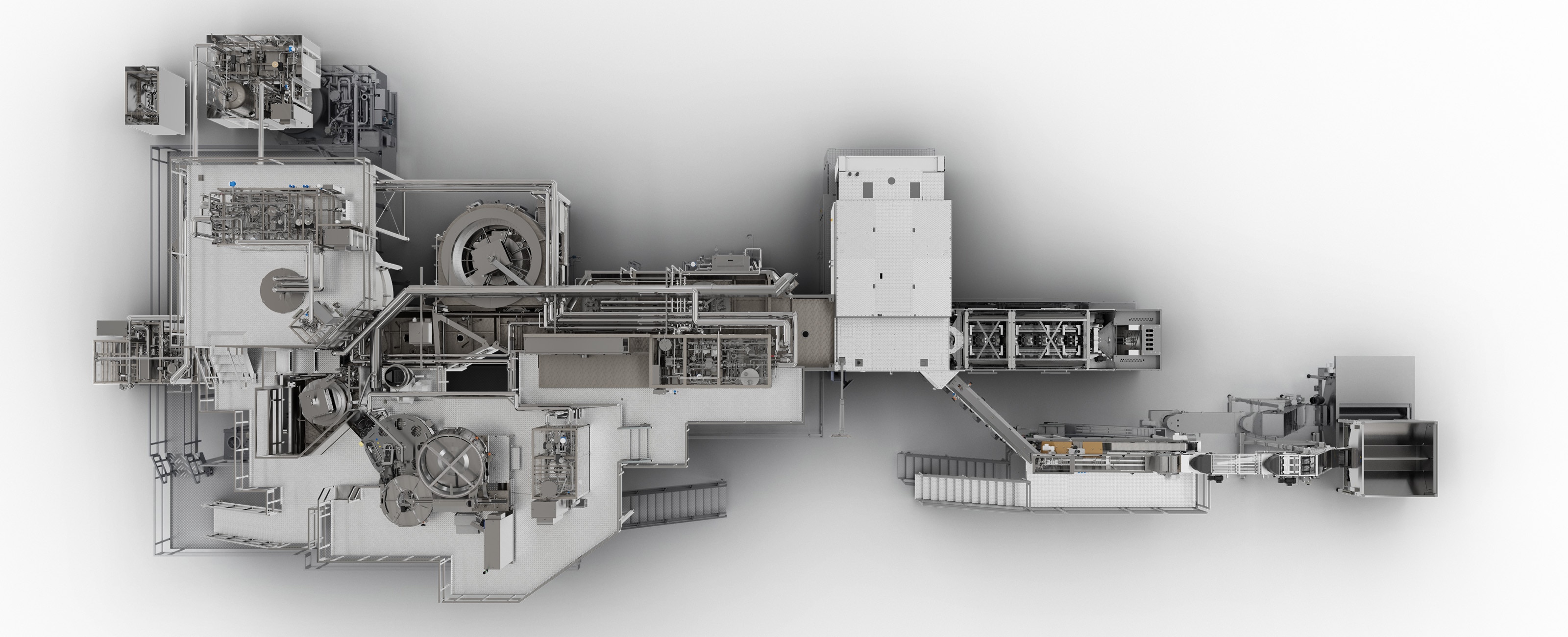
Aseptic filler
- The appropriate filling valve for the most wide range of products – still and carbonated
- It is also suitable for beverages with (fruit) pieces of a size of up to 10 x 10 x 10 millimetres
Aseptic capper
- Every capping head has its own separate servo drive.
- A transfer tunnel separates the sterile area from the outside area.
- The proper technique for every cap – overcaps with round bottle possible!
Cap sterilisation module – two variants
- After cap inspection, the caps are sterilised with the appropriate system
- Cap inspection unit checks caps for: Deformation, ovality, intact cap tamper-evident rings and correct orientation
- For all sterilisable caps: dry cap sterilisation by means of H₂O₂
- For submergible caps: PAA immersion bath
Rinser
- Removes residual peracetic acid from the containers
- Efficient single-channel full cone nozzle with adjusted dimensions
- Without CIP cups
- Open SIP in the clean room housing
- Reduced water consumption
- Time saved during rinsing and cleaning
- Recycling of the peracetic acid
- Recycling of sterile water
Container sterilizer
- Re-use of the liquid peracetic acid from steriliser and rinser for the exterior treatment of the containers
- Best draining properties thanks to a Krones Tabletec table top inclined on one side
- No use of surface-active agents
Blow moulder
Preform feed system
Benefits to you
Smaller installation surface
- Linear machine design
- Integration of the valve block into the machine frame
- Unburdened rinser
- Reduction of the sterilisation modules from three to one
- Integrated, decentralised ventilation technology – no additional controller required
Reduced operation and maintenance work involved
- Tabletec table top inclined to one side
- Integration of the valve block into the machine frame
- Capper in hygienic design
Highly efficient and safe sterilisation
- Spreader-type nozzles for reliable interior treatment of the containers, even in the neck-finish area
- No surface-active agents required
- Hermetically isolated sterile areas
Energy efficiency and environmental friendliness
- No surface-active agents required
- Re-use of rinsing water
- The single-channel rinser with improved nozzles reduces the air consumption
- Lower energy consumption thanks to a modified ventilation system
High output
- Minimum loss of product during type change-over by product supply to the filler from the top
- Reduced SIP time by steam sterilisation of the filling valves
- No CIP cups therefore faster and easier operation
- Product change-over: from the last bottle to the first within a mere 150 minutes
How can we help you?
Additional information
Download
Do you have any questions?
Contact
Krones nearby you
Sales network
Come and visit us
Events