More freedom during hot filling
Be free!
Who says hotfill bottles absolutely need compensating panels? We definitely don't! With the NitroHotfill process, just a little bit of nitrogen is added to the bottle after filling. This increases the interior pressure and balances the shrinking behaviour – even when it comes to light-weight containers. A clever design for all who do not want to be restricted in their packaging design any longer.
At a glance
- Bottling of hot products of up to 90 °C into PET containers
- No more restrictions to the bottle design through panels
- Blowing and filling with outputs of up to 70,000 containers per hour
- Suitable for:
- Bottle volumes of up to 2.0 litres
- 38 mm neck finish diameter
- Standard and lightweight containers
NitroHotfill in the entire line
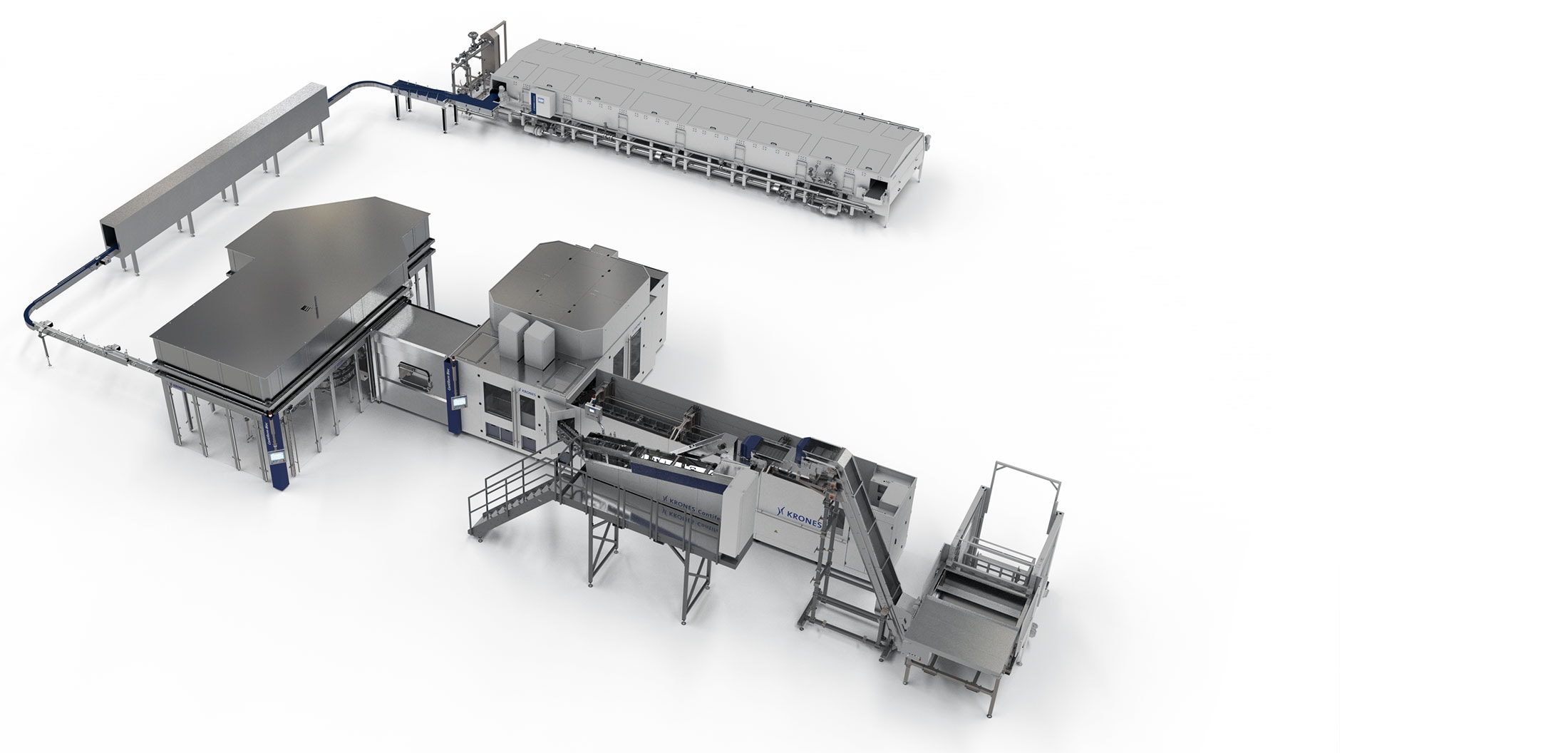
Bottle inverter
Capper
Nitrogen dosing system
Modulfill filler
Container base cooling system
Benefits to you
NitroHotfill is an especially economic and flexible alternative to the conventional hot filling process.
This process...
- enables material savings of up to 30 percent.
- no longer requires the panel design for compensating the vacuum pressure.
- reduces both, the rinsing air consumption and the rinsing times during the stretching process.
- enables station outputs of 2,500 containers per hour during stretch blow moulding.
- reduces the change-over times for moulds via quick-change systems.
- increases the stability of light-weight PET bottles and the transport properties.
How can we help you?
Additional information
Download
Do you have any questions?
Contact
Krones nearby you
Sales network
Come and visit us
Events