The newest generation of high-performance blow moulders
Sustainable and flexible
Your efficiency sets new standards. In terms of high-pressure air and energy consumption, it once again undercuts everything that came before it: The fourth generation of the Contiform is here! It uses the market-proven technology of its predecessor - but only as a basis. For be it flexibility, hygiene, user-friendliness or digitalisation: In the course of a complex development project, the blow moulder has been given a whole series of new features and optimisations.
At a glance
- Container and product range
- Container volumes of 0.1 to 3.5 litres
- Cylindrical, square and rectangular containers
- For still and carbonated products
- Machine portfolio
- 4 to 28 blowing stations
- Output per hour
- Production of 4,000 to 70,000 containers per hour
The newest generation of Contiform
The design
The Contiform has a modular design and can be individually equipped for to meet all requirements.
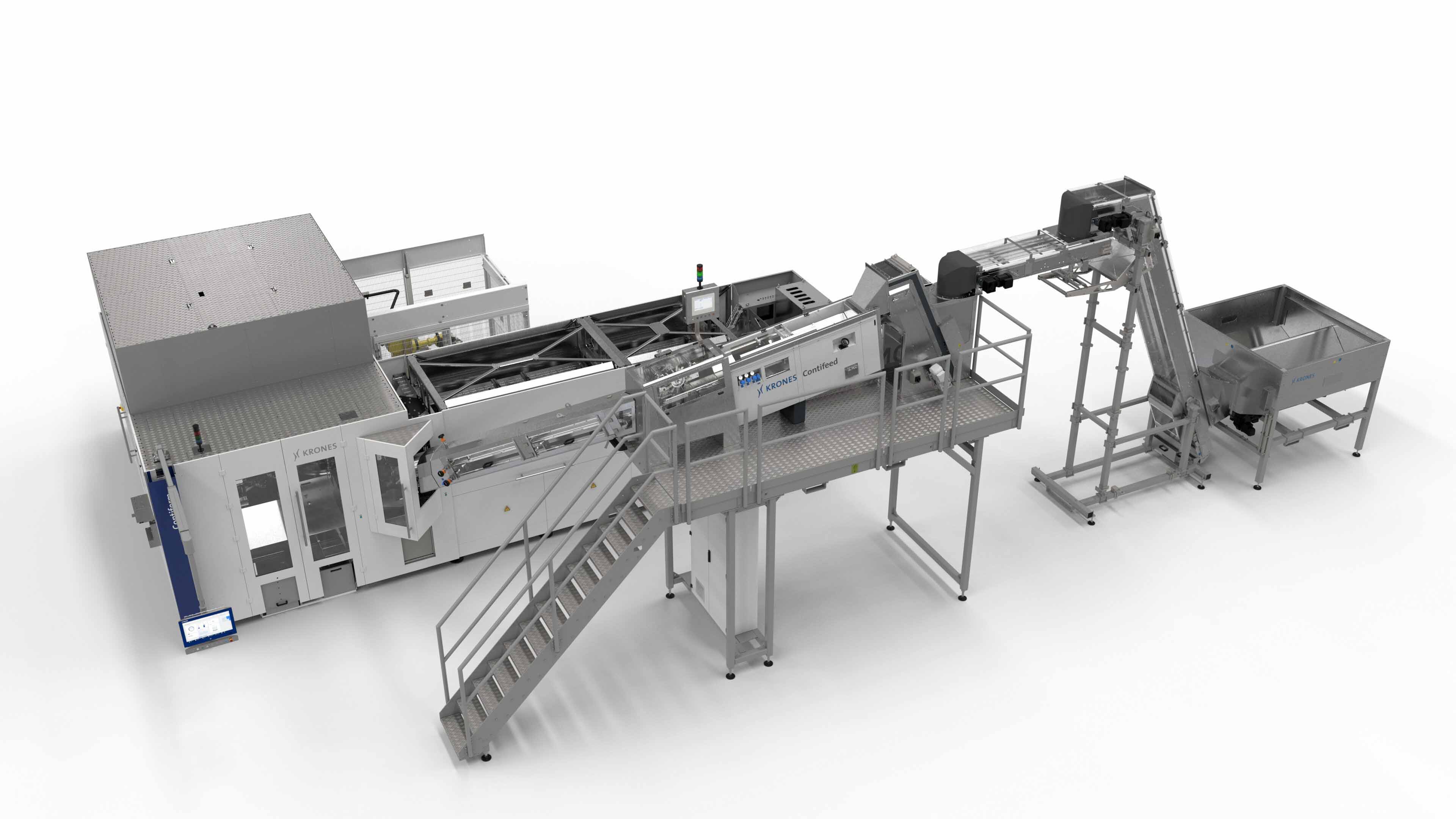
Preform feed system
* Options
Basic machine
- Linear infrared heating module for processing preforms with a length of up to 160 mm and a support ledge diameter of up to 48,5 mm
- Blowing module with blowing stations for manufacturing containers of up to 3.5 litres
Optional modules
- Prejet preform interior cleaning system for pre-cleaning the incoming preforms
- PET-View inspection system for the integral quality control of preforms and containers
- MouldXpress Robot automatic mould changer for highly efficient change-over without manual intervention
- Self-learning Contiloop AI process control for fully automatic and intelligent parameter adjustment
Modules
Focussed on performance right from the beginning
At a glance
- Applicable with lightweight, standard and heavy preforms
- Three models – suitable for the respective blow moulder output
- Two variants of the feed rail:
- Gravity system for all common preform types
- Air-assisted – ideal for lightweight preforms and high-speed applications
Optional:
- Hygienic design
- Soft-tilting preform tipper for a particularly gentle preform infeed
Benefits to you
- Automatic troubleshooting
- Quick and infinitely variable adjustment to every preform type
Efficient and flexible
Heating tunnel
- Very small oven chain (36.4 mm or 50 mm)
- Additional reduction of the heating room
- Adjustable base reflectors: adjustable to the respective preform length
- Maintenance-free system of ceramic reflectors
Heaters
- Parabolic reflector for the top infrared emitter
- Longer infrared emitters and smaller dead spaces between the heaters
Benefits to you
- Up to 15 percent smaller footprint thanks to reduced deadspaces
- Improved lightweighting potential through targeted heating of the preforms directly below the support ledge
- Up to 5 percent lower heating energy consumption due to shorter distances and parabolic emitter technology
Robust and precise
Transfer system
- Five-point heating mandrel in the linear oven
- Only four internal horizontal preform and container transfer points
- Actively controlled transfer grippers
Platform and drive technology
- Torsion-resistant platform construction with skip-and-run technology
- Five high-precision Monotec servo motors with real-time synchronisation
Benefits to you
- Precise transfer of preforms and bottles
- Perfectly suited for very light preforms
- No PET dust deposit
- No change of handling parts if the neck finish remains the same
- Significantly reduced scrap rate thanks to skip-and-run technology
Intelligent while saving on compressed air
Blowing stations
- Electromagnetic stretching system without air consumption
- Extremely low dead space volume in the entire blowing station
Compressed-air recycling
- Once again a further developed compressed-air recycling system, the Air Wizard Triple
- With intermediate pressure stages for internal recovery of the compressed air
- Automatic self-optimisation of the blowing air recycling process
- Considerably lower valve switching time dispersion
Benefits to you
- Up to 30 percent less blowing air consumption in comparison to the valve technology used up to now
- Avoidance of potential incorrect settings
- Larger process windows thanks to increased accuracy of the blowing process
Bottle design and moulds
Creative and in line with the market
At a glance
- Four production centres worldwide with state-of-the-art manufacturing technology
- Container design experts at all four locations
- Design and production of mould types for all Contiform series
- Mould validation on our own technical centre systems
Benefits to you
- Customer-oriented consulting: Creative, functional, unique
- Individual designs with a view to customer requirements and feasibility in the beverage line
- Experience from more than 20,000 moulds per year
Better in combination: Contiform block solutions
Flexible block solutions
- Contiform Bloc: Blow moulder with filler or labeller
- ErgoBloc L: High-performance block consisting of blow moulder, labeller and filler
Compact block solutions for noncarbonated water filling
- Contiform Bloc BF-C: Blow moulder and filler
- ErgoBloc LM: Blow moulder, labeller and filler
- More than 50 years of experience in block technology
- More than 2,000 Contiform block solutions sold worldwide
- More than 80 percent of all Contiform blow moulders are supplied in block configurations.
Benefits to you
Reduced heating energy consumption
The further optimised infrared heating technology made it possible to reduce the energy consumption for heating the preforms by up to an additional 5 percent.
Production efficiency
With its sturdy design and new functions, such as skip-and-run, the new Contiform continues to operate with the utmost reliability and with even less interference than before.
High-pressure air efficiency
The Air Wizard Triple can achieve a high-pressure air saving of up to 30 percent compared to the previous generation.
Ergonomic design and user-friendliness
The servo drives in conjunction with the improved rotary joint continue to keep the noise level stress-free, even at the highest output rates. The new operating interface with large touch-screen allows for even more efficient working with the machine.
Why the new Contiform is enviro-classified
Energy efficiency
- Further optimised heating room and heaters for the lowest possible heating energy requirement
Compressed-air efficiency
- Further developed compressed-air recycling for the highest possible internal and external reuse of the blowing air
Environmental compatibility
- Further minimised lubricant consumption
- Use of components made of recycled material