Ultrahygienic block for sensitive products
A protected atmosphere for your product
The Krones family includes experts for all kinds of different sterilisation methods and products to be filled. One of them is the Contipure Bloc P**: It is specialised on sensitive products and fully meets their requirements.
At a glance
- Design:
- Preform sterilisation module
- Blow moulder
- Aseptic filler and capper
- Suitable for:
- Aseptic filling
- Sensitive products
- Round, square and rectangular PET containers
- Standard and lightweight containers
- Output: Up to 72,000* containers per hour
* Depending on the container size and product | ** P=Performance
Buying time during cleaning
The performance variant uses hot caustic for machine surface disinfection and reliably sterilises the product channels with steam. This process guarantees microbiologically safe filling in the fastest cleaning and sterilisation times.
The benefits
- Timespan from last to first bottle:
- only 90 minutes – including cleaning and sterilisation
- Saving a full hour compared to other systems
- Only 30 minutes intermediate sterilisation after manual interventions in the block
- Handling parts change-over at the blow moulder:
- Without intervention in the sterile area
- Therefore no intermediate sterilisation required
The key components
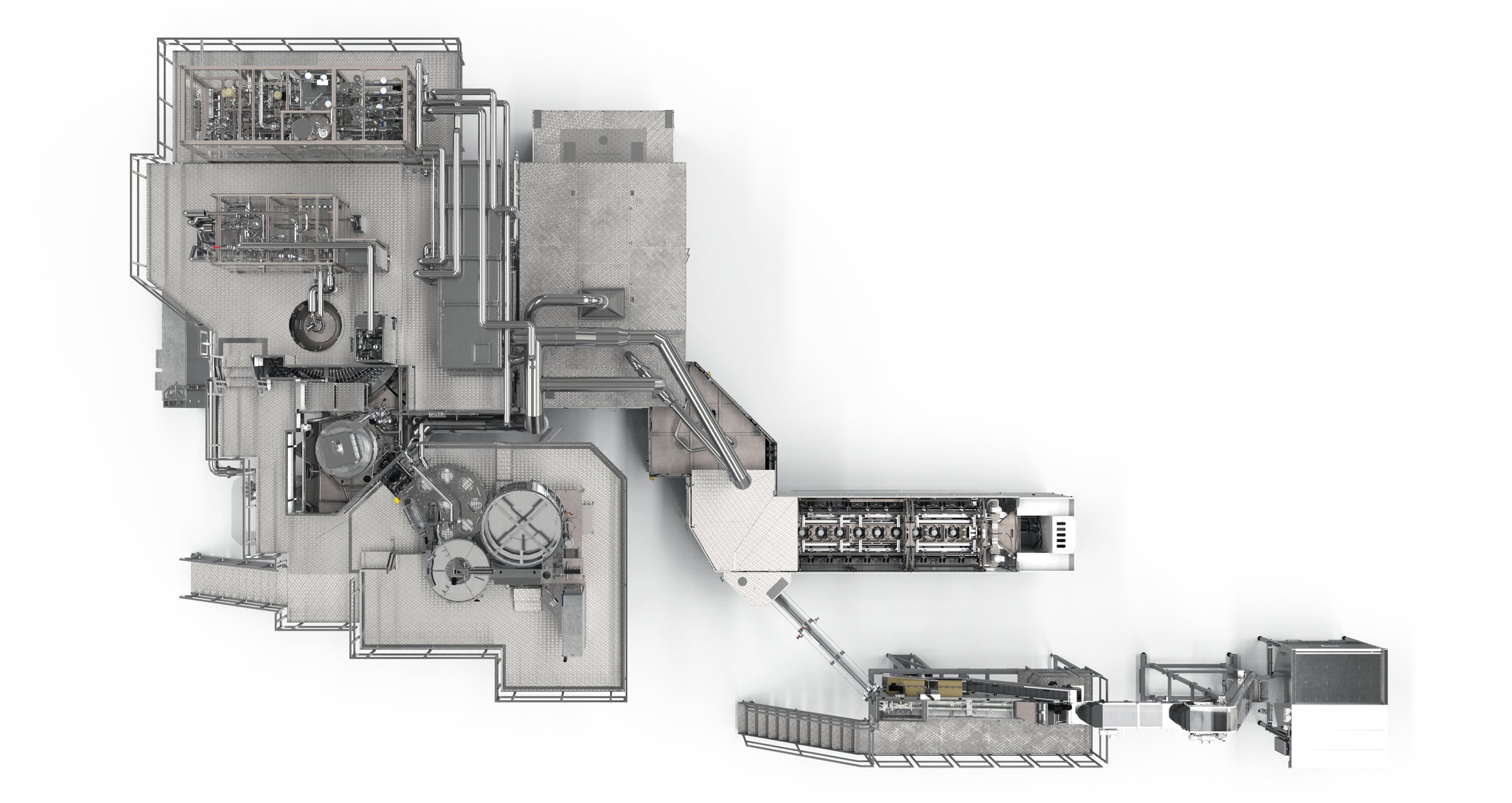
Prejet Preform rotary rinser
Compact one-starwheel concept at ground level
Method of operation:
- Immersion of the rinser lances in the preforms
- Blowing out of the particles with pre-filtered andionised sterile air
- Simultaneous to particle blow out: Extraction of themix of air and dirt
Contifeed preform feed system
- Thanks to hygienic design optimal for the Contipure Bloc P
- Variants adjustable depending on the installation position
Infrared oven
Servo-controlled oven of the Contiform standard series with efficient and pre-filtered preform air cooling system
Option: Tool-free quick-change of the protective plates of the oven heating mandrels
Optimised in terms of energy:
- Low dead spaces between the heaters
- Longer infrared radiators
- Use of parabolic mirrors
Preform sterilisation module
Contipure D preform sterilisation module
- The module is between infrared oven and blowing module.
- Via nozzles, a targeted and directed feed of gaseous hydrogen peroxide (H₂O₂).
- This provides overflow and thus results in a simultaneous internal and external preform sterilisation.
Blowing module
- Improved hygiene standard
- The air used for stretch-blow moulding the PET bottles is filtered beforehand using a pre-filter unit with autoclaveable filters.
- A fine dust filter is also installed on the heating module to ensure that dirt particles such as coal dust, pollen or plant spores are filtered from the ambient air.
CapAsept D cap sterilisation module
- Caps are blown out with ionised air right in front of the unit.
- Sterilisation by means of gaseous H₂O₂
- No back-up pressure acting on the caps – no deformation
- Clocked feed of the caps on demand: No bottle – no cap
Aseptic capper
- Every capping head has its own separate servo drive.
- A transfer tunnel separates the sterile area from the outside area.
- The proper technique for every cap – overcaps with round bottle possible!
Aseptic filler
- The appropriate filling valve for the most wide range of products – still and carbonated
- It is also suitable for beverages with (fruit) pieces of a size of up to 10 x 10 x 10 millimetres
Benefits to you
Triple protection
The all-round treatment with gaseous H2O2 sterilises the entire preform surface at once: Inside, outside and in the neck area.
Gentle preform treatment
The sterilisation of the preforms hardly leaves any residues: This is because the surface enlarges by many times and the residues of the sterilisation medium are diluted accordingly.
Flexible production
The optional automation package allows change-overs to be performed on the entire block in under 20 minutes – including the emptying and starting up of the machines. This means that you gain an additional two hours of production time with each change-over – and operators have their hands free to perform other tasks.
Fully-automatic change-over
Handling parts change-over at the filler and the capper can be performed up to a defined output without any manual interference.
High availability
The complete block production can run for up to 120 hours at a time – and only a short 90 minute sterilisation break is required before it is back in action and ready for the next round. Intermediate cleaning after manual interventions also only takes 30 minutes.
Pinpoint production
Filling to the last drop: The system uses the remaining product quantity in order to calculate exactly how many more PET containers and caps are still to be sterilised.
Beverage containers made from rPET
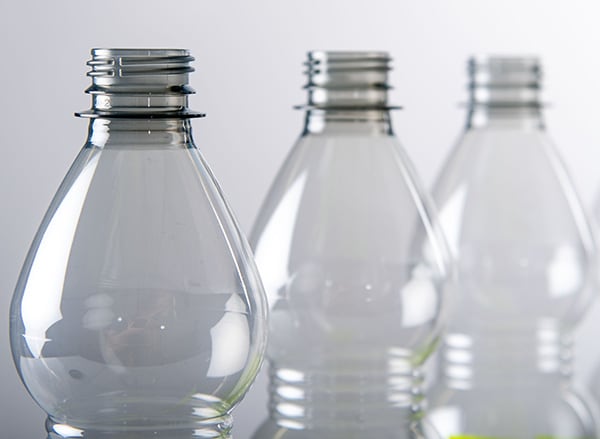
Material properties, processability, food grade quality: you can find all kinds of interesting facts about the use of recycled PET in our free white paper.