Many process and technology firsts
Pressure-sensitive labels
With the commissioning of the new line, Winzer Krems has switched over from traditional cold-glue labels to pressure-sensitive labels made of paper. Bottles will typically be dressed in a shoulder label and a back label, each applied by a dedicated labeling station. The two other labeling stations can be loaded with labels for the next fill order. That saves on changeover time since different export requirements necessitate frequent label changes – up to ten of them per day.
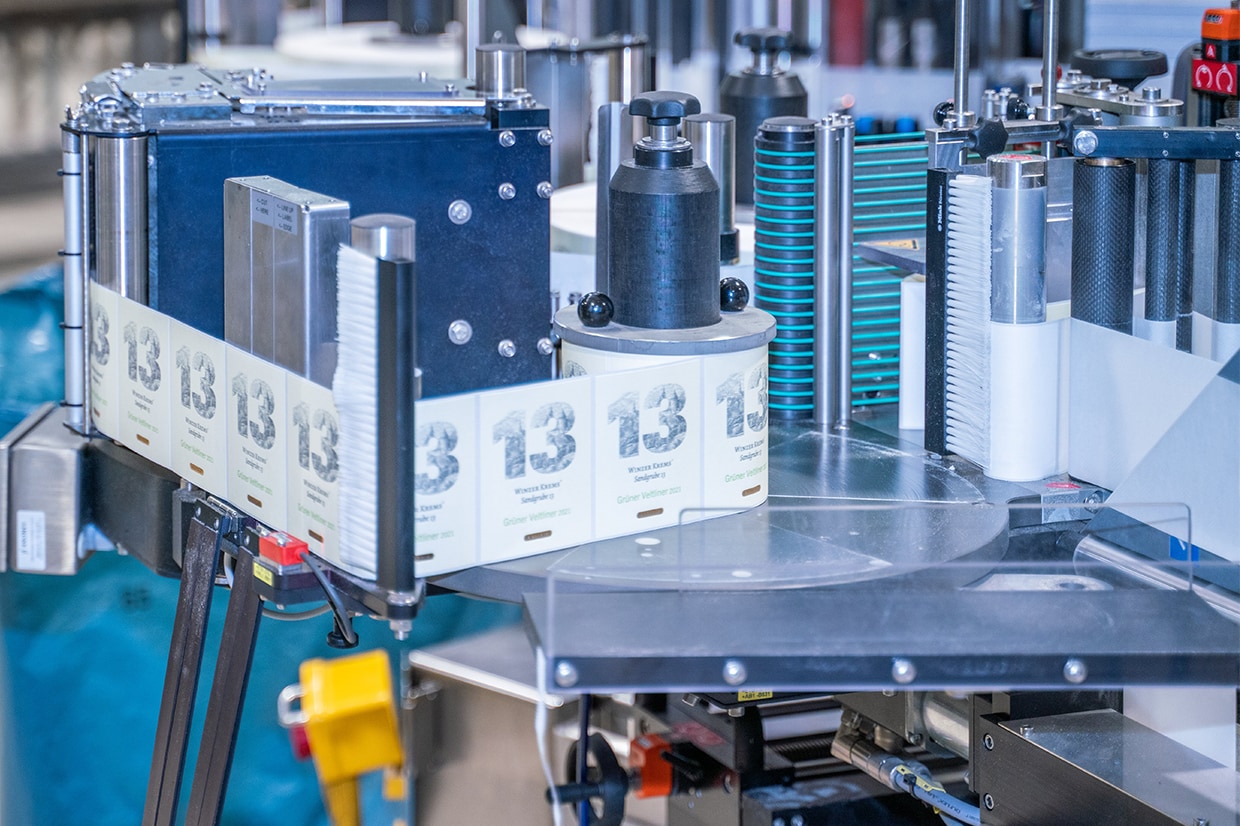