Children are bound to grow up. And the same appears to be true of many craft breweries around the world. It certainly is true of Sevenbräu, also known as 7Bräu. Since its founding 20 years ago – in 2003 –, as a small alehouse in the Gangseo district of Seoul, it has grown into South Korea’s biggest craft brewery. The newest of its three production plants is the greenfield brewery in Iksan-si in the province of Jeollabuk-do. For this facility, Sevenbräu contracted Krones and Steinecker, the beer expert of the Krones Group to install the entire brewhouse, the cold block and the can filler.
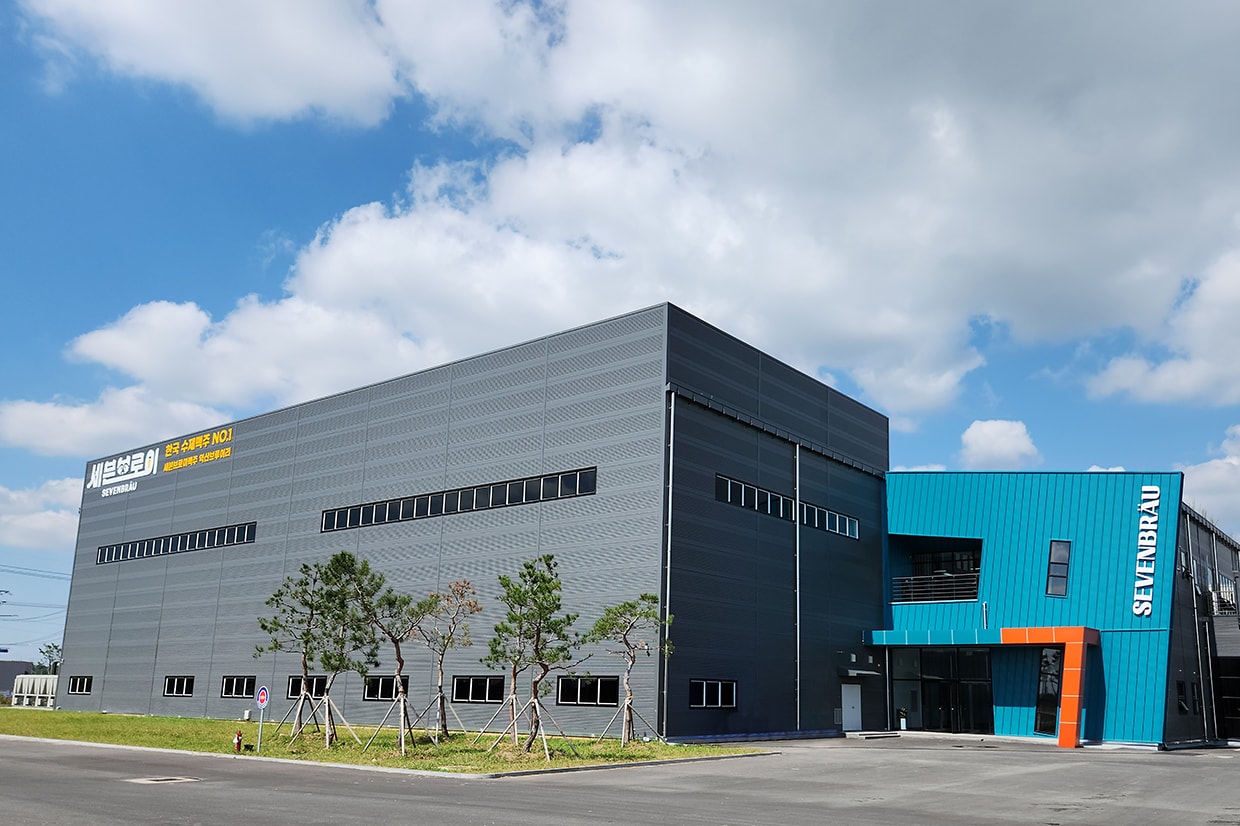
Sevenbräu