More and more, consumers are reaching for minimally processed juices, dairy products or plant-based drinks from the refrigerated display cases – all of which fall into the category of “sensitive beverages”. According to market researchers, this trend is set to continue. The worldwide markets for sports and non-dairy drinks, yoghurt smoothies and ready-to-drink coffees and teas, in particular, exhibit above-average growth rates. That is reflected in an increased demand for aseptic filling lines, which make sure the sensitive products processed on them retain their top-notch quality all the way to the consumer. Krones’ response to this trend is the second generation of the Contipure AseptBloc, which combines stretch blow-moulder, filler and closer to fill the products into PET containers in an aseptically safe, closed process.
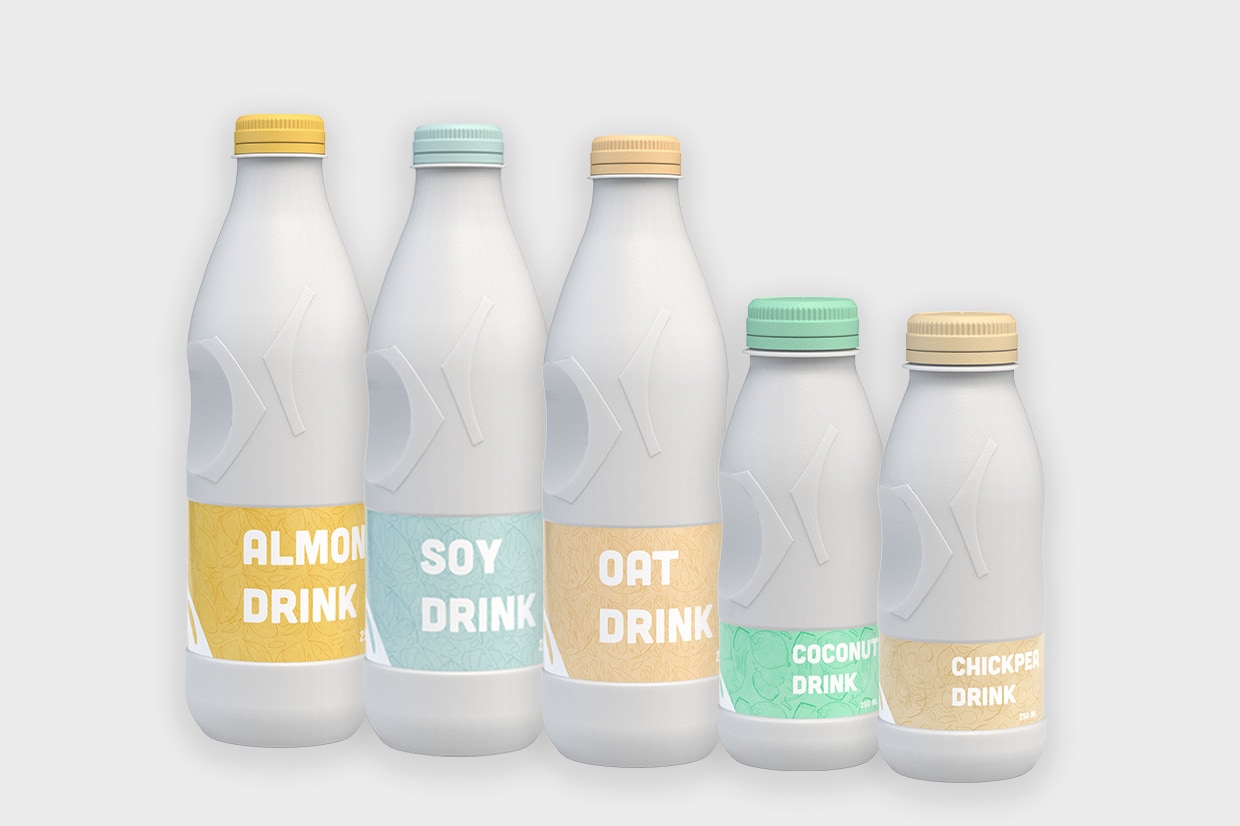