Whereas capacity for swing-stopper bottles was at one million hectolitres per year with the first new line from Krones and an existing combined line handling both NRW and swing-stopper bottles, the Kulmbacher Brauerei is now planning for an annual output of 1.5 million hectolitres. It isn’t hard to realise that this is impossible without installing further bottling capacities. The brewery therefore placed an order with Krones for an identical line, likewise rated at 50,000 bottles per hour.
So it can safely be assumed that the Kulmbacher Brauerei was fully satisfied with its first line. “We entered into negotiations bestowed with a vote of confidence,” admits Berthold Stock, a Krones sales engineer. And Stefan Simon, Head of Production & Engineering and at the same time Project Manager at the Kulmbacher Brauerei, adds: “True to the motto of ‘Never change a winning team’, it was clear to us, the brewery’s technology crew, that the new challenge in this output category could be successfully mastered only together with Krones.”
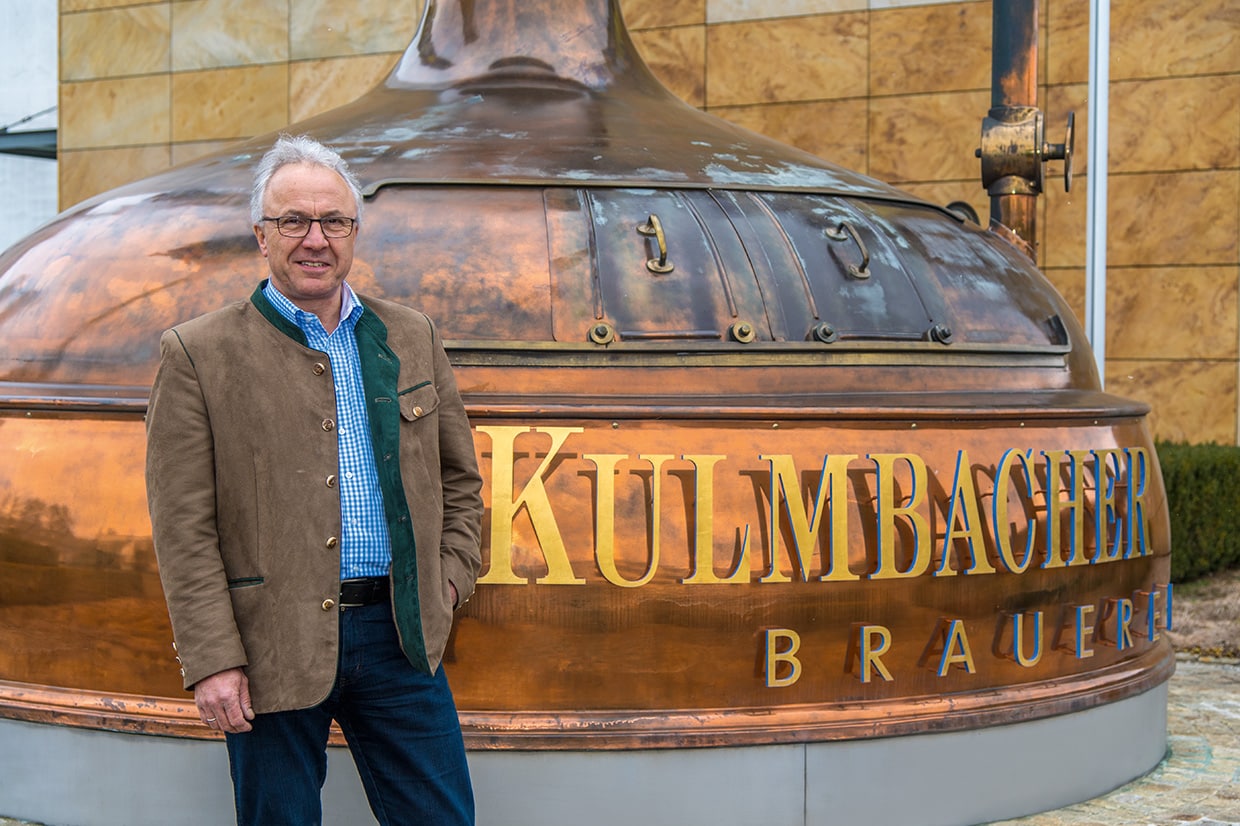